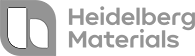
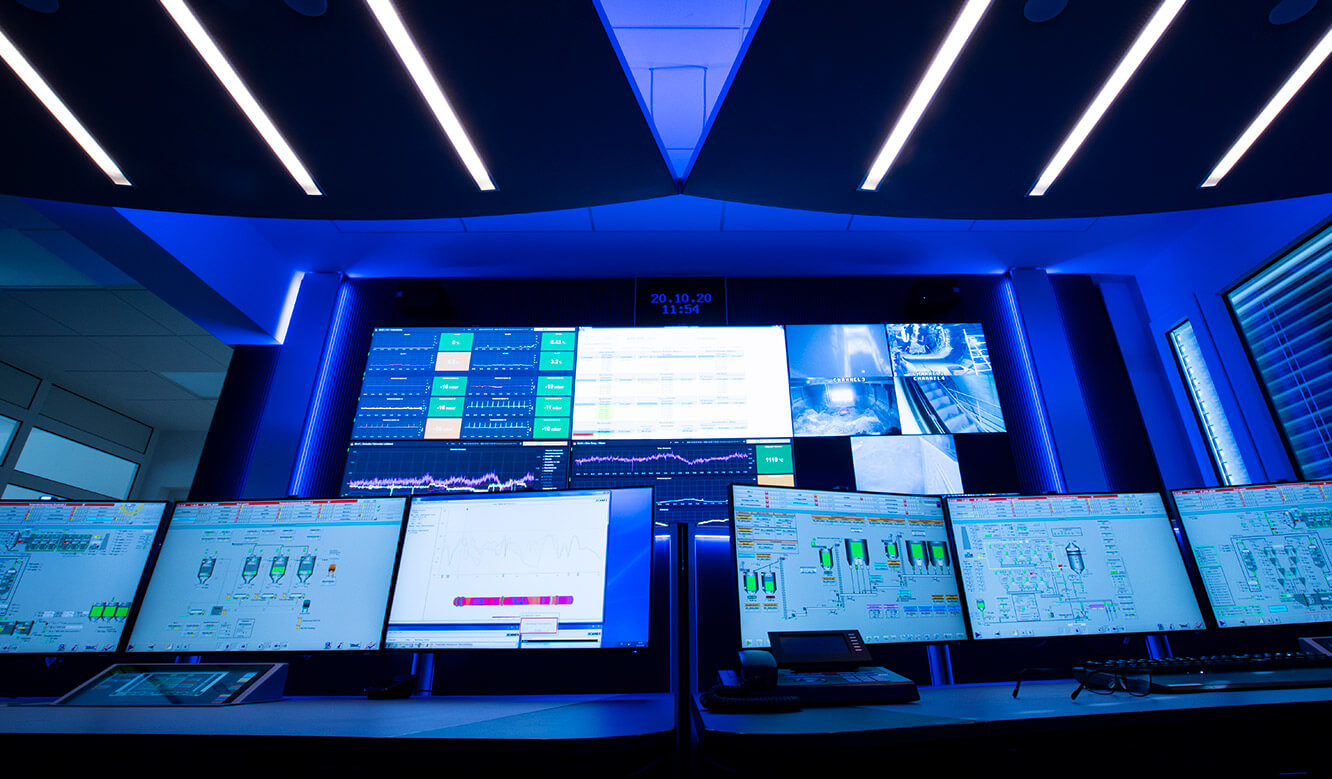
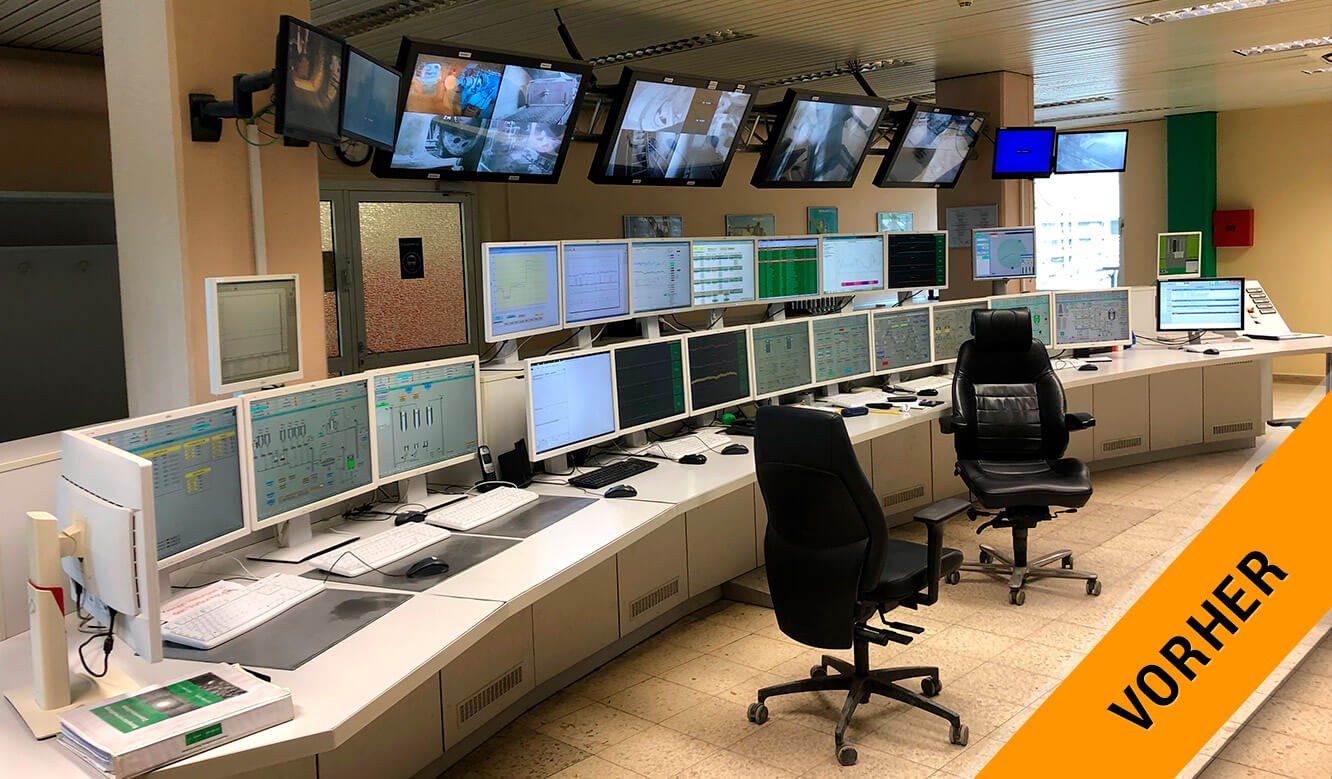
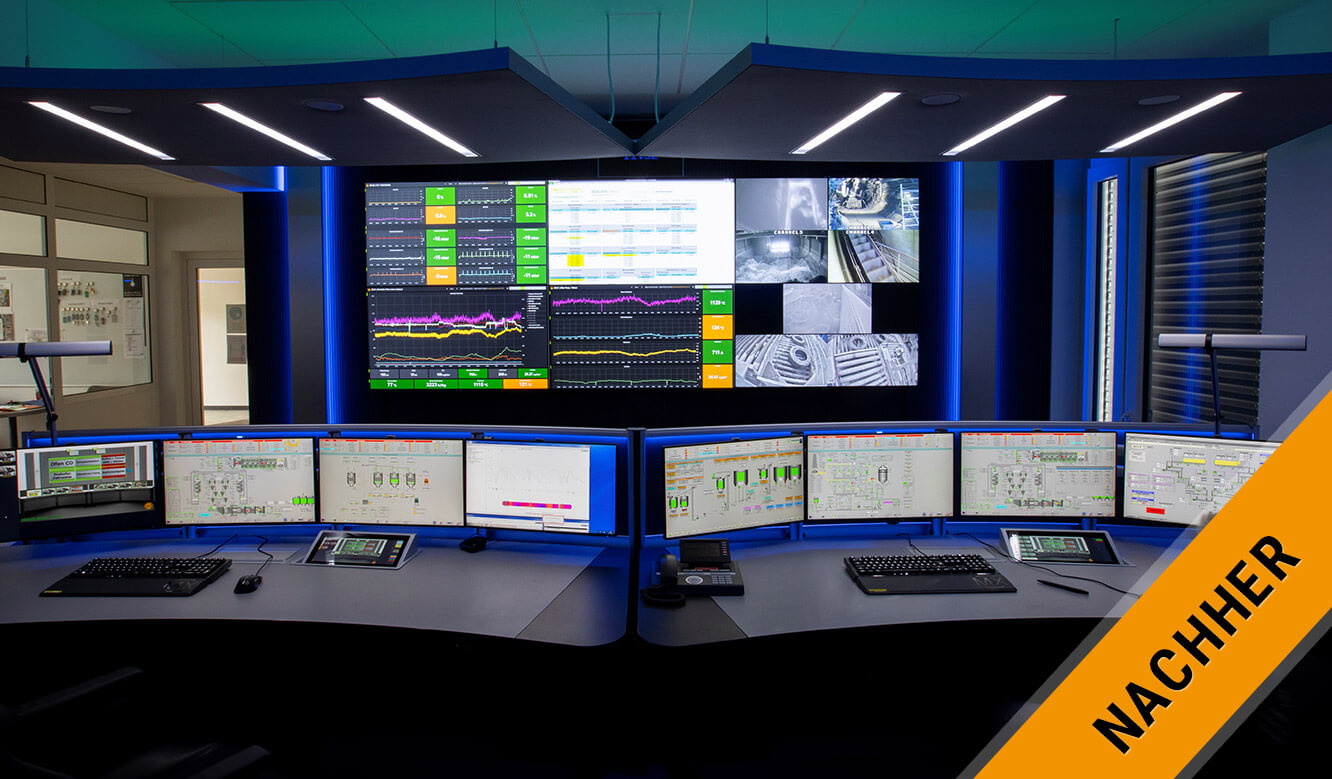
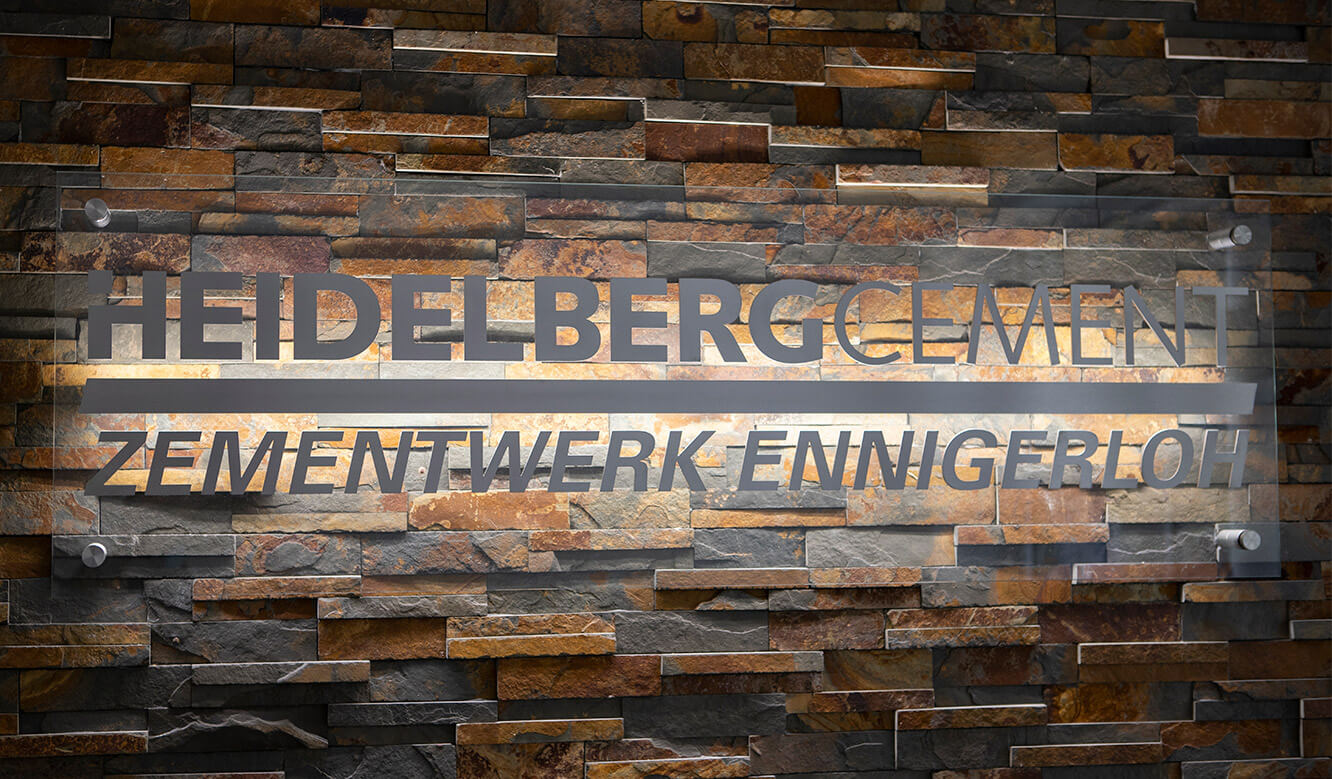
Photo 1 | JST control center: Futuristic design - the new control center at Heidelberg Materials in Ennigerloh is not only visually impressive. It's the inner values that count. Thus, the employees now benefit from the advantages of ergonomic furniture and a methodically thought-out technical control room concept.
Photo 2 | This clearly shows that more does not always mean better. The rigid displays on a confusing number of individual monitors in the former control room of the Ennigerloh cement plant made the operators' work unnecessarily complicated...
Photo 3 | ...With the installation of the new control room and the associated technology concept, workplace monitors could be saved thanks to the flexible MultiConsoling® control system, thus realising an optimised overview.
Photo 4 | Not only was the control room completely gutted in the course of the renovation work, the entrance area was also given an update with a visually effective wall logo.
Photo 5 | The cement plant in Ennigerloh: Founded in 1909 under the name Anneliese Portland-Cement und Wasserkalkwerke AG, the plant of today's Heidelberg Materials AG has been modernised many times over the decades. The control room now also meets the latest technical and ergonomic standards.
Photo 6 | JST Planning: An important step in involving all parties involved in the planning of the new control room at an early stage are the detailed 3D sketches. They provide photo-realistic impressions of the planned premises.
Photo 7 | JST control room planning: And here is the implementation of the previous 3D planning. The control room operators have a perfect view of the video wall from their workstations.
Photo 8 | Quarrying the natural stone in the Ennigerloh quarry: wheel loaders and trucks are then used to transport the large chunks of rock to the plant, where they are crushed and reduced to ballast size.
Photo 9 | Controlled in a fully automated process via the control center: the cement mill,which grinds the hard, spherical clinker from the cement kiln into the fine grey cement powder.
Photo 10 | JST 3D planning: Another example of the possibilities offered by pre-visualisation through realistic sketches in three-dimensional space.
Photo 11 | JST Planning: During the subsequent implementation of the preceding visualisation, it becomes apparent that spatial conditions are taken into account in the 3D modelling just as much as colours and light influences.
Photo 12 | JST control room furniture: Ergonomic aspects were clearly the focus of the control room concept at Heidelberg Materials AG. The electric height-adjustable operator consoles of the Stratos series, which were specially developed for control rooms, were convincing with their diverse possibilities.
Photo 13 | JST control stand tables: The Stratos X11® OperatorDesk not only meets the highest ergonomic and visual standards, ...
Photo 14 | JST control desk tables: ...behind the inspection flaps are generously proportioned, illuminated supply rooms that provide an important benefit thanks to cleanly installed technology - without visible cables.
Photo 15 | JST control room solutions: Acoustics, lighting, atmosphere - the OPAL ceiling canopy with integrated audio boxes creates a new level for the operator workplace. One of the decisive advantages - especially in shift work - is the integrated HCL light source (Human Centric Lighting), i.e. lighting that takes into account the visual, emotional and biological effects of light, whose colour values also have a positive influence on concentration and performance.
Photo 16 | JST TFT columns: Height-adjustable 3D articulated arms allow a parabolic arrangement of the monitors and thus offer the user an optimal field of view.
Photo 17 | JST furniture: Individually designed for the control center of HeidelbergCement in Ennigerloh - a cabinet solution with integrated galley kitchen.
Photo 18 | JST consultant Volker Weimer (left) - here talking to project and site manager Roland Jaeger from Heidelberg Materials - on the project: "Together, we developed the key data for an efficient concept both on site and in the control room simulator. The new control room is an asset in every respect. Not only the ergonomic aspects and the flexible technical possibilities are convincing; questions regarding 'air conditioning' and 'sound level' were also successfully solved."
Photo 19 | JST big screen: Visually and technically a successful solution: Der JST DisplaySuit with integrated AlarmLight provides the basis for the proven...
Photo 20 | … QuickOut assembly system perfect opportunities for service accessibility without interrupting operations. Individual displays can easily be pushed forward by pressing lightly on the outer edges.
Photo 21 | JST large-screen technology: The 46-inch displays of the Videowall are also suitable for large overviews (BigPictures), if required, thanks to their ultra-slim frames with a picture-to-picture distance of only 3.7 mm. Equipped with S-PVA panels, these LCDs have been specially developed for long-lasting operation in control rooms.
Photo 22 | JST MultiConsoling®: With the interactive MultiConsoling®-operator interface myGUI® the consoles of the workstations and the large display wall are displayed as a "control room image". All required sources are shown on the side and can be dragged and operated by the plant operators via their customisable icons onto any screen at their workstation or large screen wall with a simple mouse click.
Photo 23 | JST MultiConsoling®: With the JST CommandPad®, a control panel specially optimised for 24/7 operation, the employees in the Heidelberg Materials control center have the interactive myGUI® user interface and thus the entire control room control permanently in view.
Photo 24 | JST 3D planning: The arrangement of large-screen technology and workplace displays was also integrated into the planning with 3D visualisation...
Photo 25 | so all those involved were able to get an idea of the details of the new control room in advance.
Photo 26 | JST MouseHopping: Small light with a big effect: The component shown here makes it possible to guide the mouse conveniently over the individual workstation monitors and over the various displays of the large display wall.
Photo 27 | Retrospective view of the time before the control room implementation: On the right side, the large-volume silver-coloured supply air hoses are clearly visible.
Photo 28 | After installation: Behind the fronts of the DisplayWall are the components for the climate concept. The panels in the Rekton acoustic design not only have a positive effect on the sound level in the room, they...
Photo 29 | ...also conceal important components of JST climate planning. Cooled air exits through the large-volume air outlets at low velocity, hits the back of the operator desks and then swirls successively. The decisive advantage: Unpleasant nuisances caused by draughts are avoided.
Photo 30 | JST MultiConsoling®: Crucial hardware for installing the entire technology outside the control room via the JST MultiConsoling® : The MultiCenter provides ports to connect grabbers (computers) and multi-consoles to process signals in real time. Below this is the myGUI controller.
Photo 31 | JST Technik: Indispensable components for the effective use of the MultiConsoling® control system: The power unit located in the upper section of the 19-inch installation kit is decisive for the 230-volt supply of the grabbers below.
Quality and processes: dual mission for new control room
It is a long journey until blasted large-sized rock becomes usable cement. Crushing, grinding, drying and burning processes are necessary for this. In the new control center of Heidelberg Materials AG in the Ennigerloh cement plant, the quality of the product is now monitored in addition to these processes. Technical and ergonomic solutions from JST – Jungmann Systemtechnik® support smooth processes there.
A fully automated mechanism. In the raw mill, rock and lime are dried and finely processed like flour. Cement clinker is produced in burning processes, which is later ground into the final product cement. But in the event of a malfunction – for example if the temperature is exceeded – it is the control center drivers who have to decide what to do. 24 hours a day, seven days a week.
Interactive experience in the new control room: Zoom, rotate, nighttime view and change of perspective – here you can experience control room concepts in interactive 360 degree visualisations! How does the new control room look? How can the operator consoles be optimally positioned? How big should the monitor wall be? With professional 3D studies and virtual tours – here at Heidelberg Materials in Ennigerloh – these and many other questions can be answered at an early stage of the project. Light influences, colours, spatial conditions – there are almost no limits to the design possibilities. Go on a three-dimensional journey of discovery now!
"In the past, where all the cables ran together"
The task: product quality control and process monitoring – previously divided between two control room areas – are to be spatially bundled. “In the past, the control rooms were located where all the cables came together. For us, that was at the end of the kiln,” says Heinz Bröker, plant manager of the Ennigerloh cement plant. For us, that was at the end of the kiln,” says Heinz Bröker, plant manager of the Ennigerloh cement plant. “The control functions were very time-consuming for the staff,” explains the engineer.
The rigid displays on a confusing number of individual monitors in the former control room of the Ennigerloh cement plant made the operators’ work unnecessarily complicated… …With the installation of the new control room and the associated technology concept, workplace monitors could be saved thanks to the flexible MultiConsoling® control system, thus realising an optimised overview.
Tasks are bundled with new technology
With the new solutions from Jungmann Systemtechnik, Heidelberg Materials is now setting the course for the future at the Ennigerloh location. Heinz Bröker: “Only the JST technology gave us the opportunity to bundle the tasks from all control technologies and thus enable the transition to a relaxed working environment.”
High demands on ergonomics in the control room
In addition to the control room specialists’ furniture solutions , which have been tried and tested hundreds of times, another convincing component is used to optimise sound levels and lighting: the OPAL X11® acoustic ceiling canopy with integrated HCL light source (Human Centric Lighting) for more concentration and performance. The sails are not only a visual highlight, they also create a perfect room atmosphere. Glare-free light and optimal acoustics,” says Heinz Bröker.
With myGUI ® "all systems effortlessly under control".
This positive summary is also due to the advantages of the new large display wall and the associated flexible control by JST MultiConsoling®. JST consultant Volker Weimer explains what makes the operation so unique: “Special JST CommandPads® are integrated directly into the operator consoles. With the myGUI® interactive user interface, they reflect a 3D layout of the entire control room infrastructure. This way, the control room operator has all systems under control effortlessly.”
Temperature and sound level effectively reduced
Another advantage: With the MultiConsoling® system, it is possible to outsource the entire technology from the control room. Heat and noise emissions are significantly minimised. A climate concept adapted to the possibilities of JST technology brings additional plus points for the working environment. Cool air is directed into the room under the large display wall and distributed diagonally upwards. Heinz Bröker comments: “The new climate concept is absolutely convincing”.
With all senses: "OPAL X11®" - THE upgrade for light and acoustics
Efficient reduction of the sound level in the room and glare-free, natural workplace lighting are just two of the convincing benefits of the new “Operator Acoustics Light – OPAL X11®“. In cooperation with experts from the disciplines of room acoustics and lighting design, the JST experts closely oriented the development of the acoustic ceiling sail on the basis of occupational health specifications for shift operations to everyday control room conditions. The declared goal: a new level for the operator workplace. The result: an innovative and at the same time economical solution that serves to optimise concentration and performance with an integrated HCL light source (Human Centric Lighting). The choice of insulation materials used enables an 80 percent reduction in room sound. An integrated audio system also allows the user to receive visual as well as acoustic alarms.
Press review
Our references today (selection)
A
B
C
E
H
I
M
N
P
R
S
- s.Oliver, Rottendorf
- SachsenEnergie, Dresden
- SAG, Berlin
- SAG, Nürnberg / Nürnberg Messe
- Salzgitter Flachstahl
- Senvion SE, Osterrönfeld
- SGL Carbon Group, Bonn
- SIEMENS
- SIEMENS, Wegberg
- Spenner, Erwitte
- Städtische Werke Magdeburg
- Stadtwerke Gießen
- Stadtwerke Ratingen
- Stadtwerke Schwerin, Kraftwerk Süd
- Stadtwerke Steinburg GmbH, Itzehoe
- Stadtwerke Wolfenbüttel
- Starlim Sterner, Marchtrenk
- STORAG ETZEL, Friedeburg
- Straßenverkehrsamt Frankfurt am Main
V
Unsere Referenzen (Archive)