
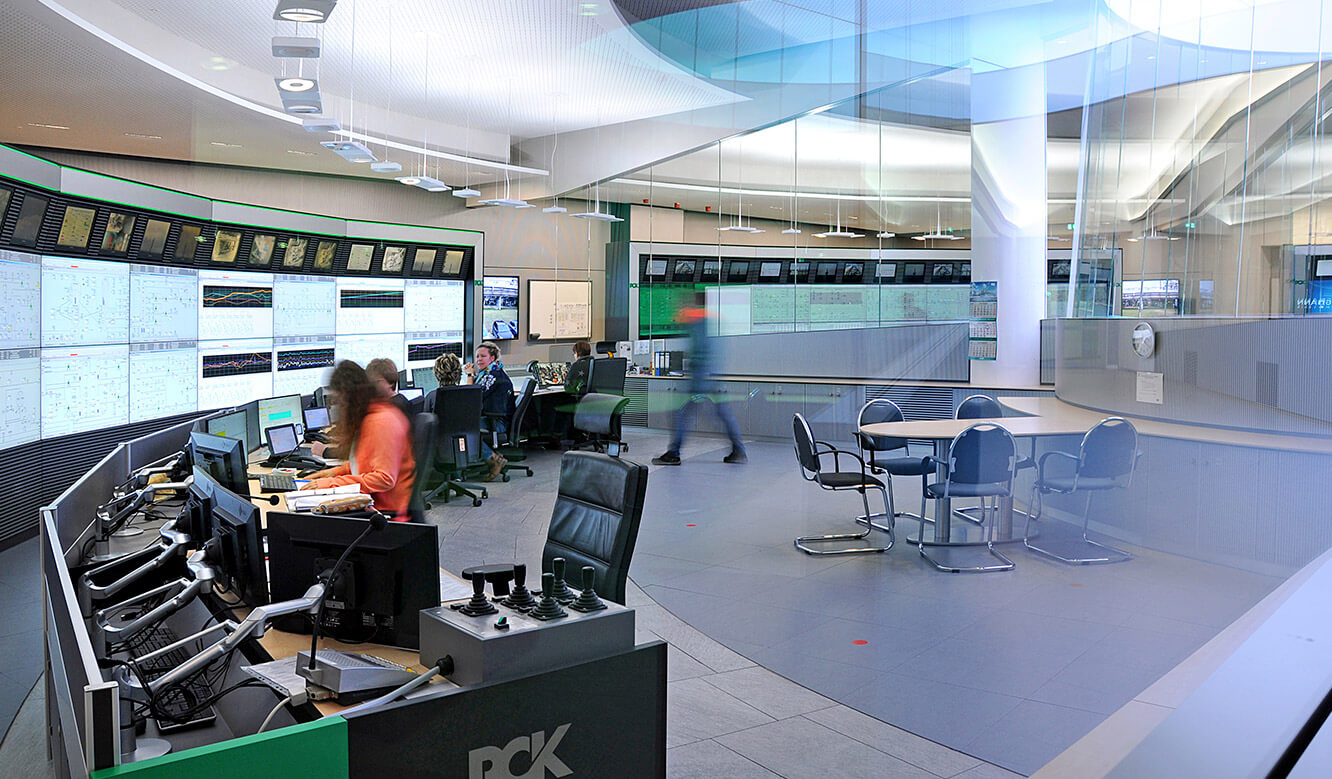
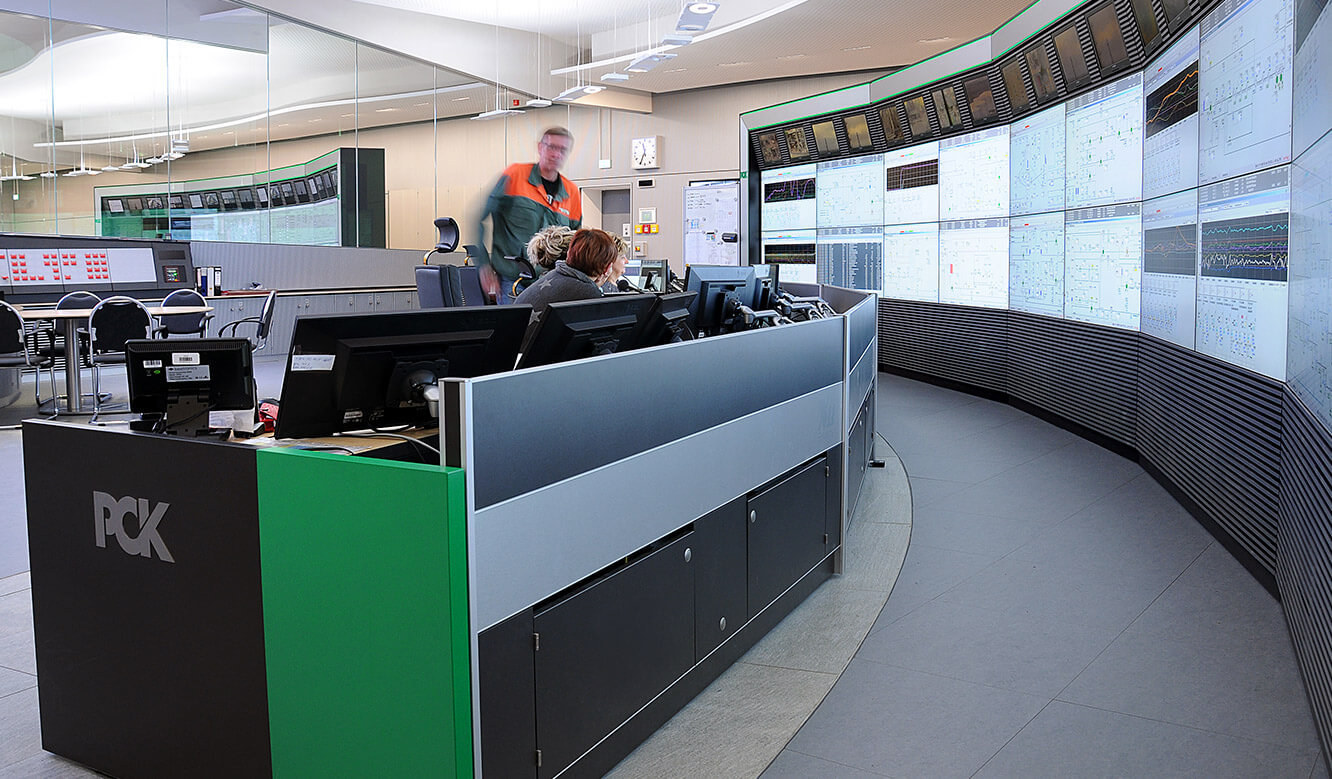
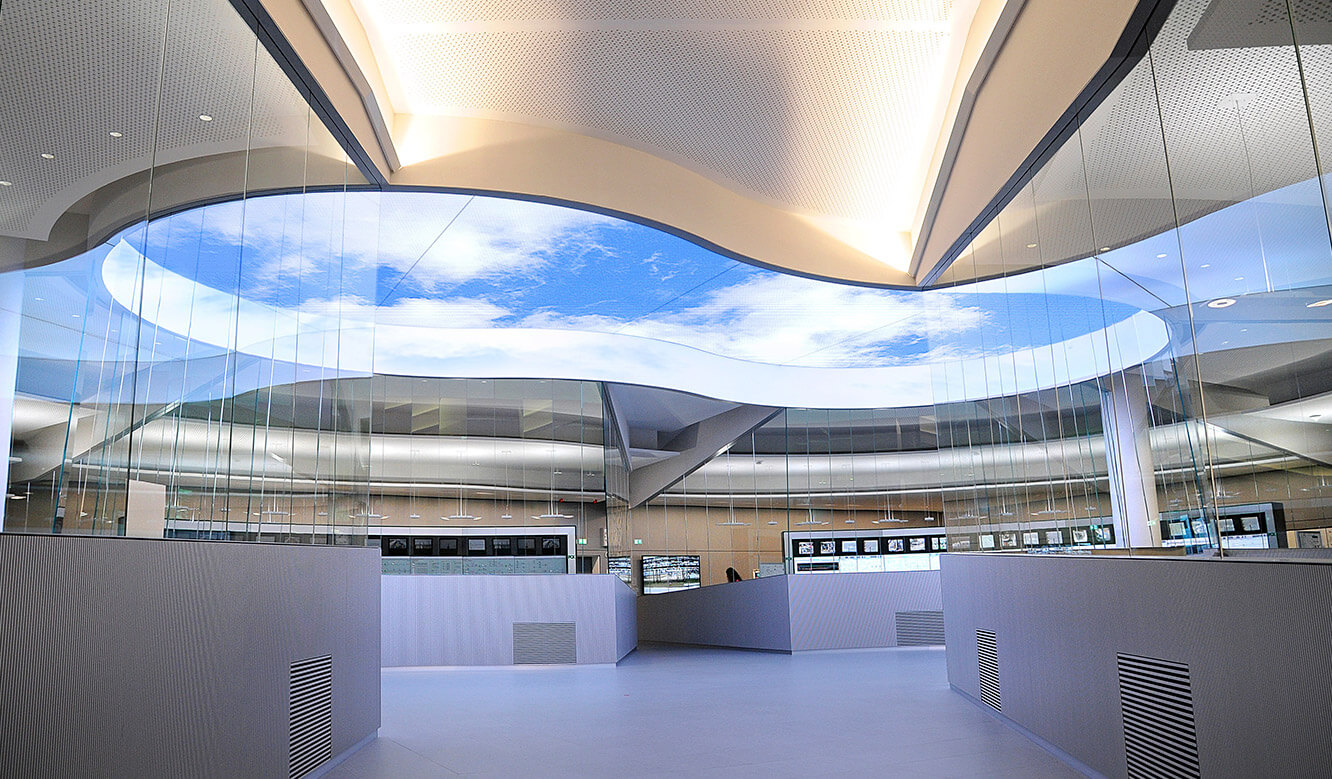
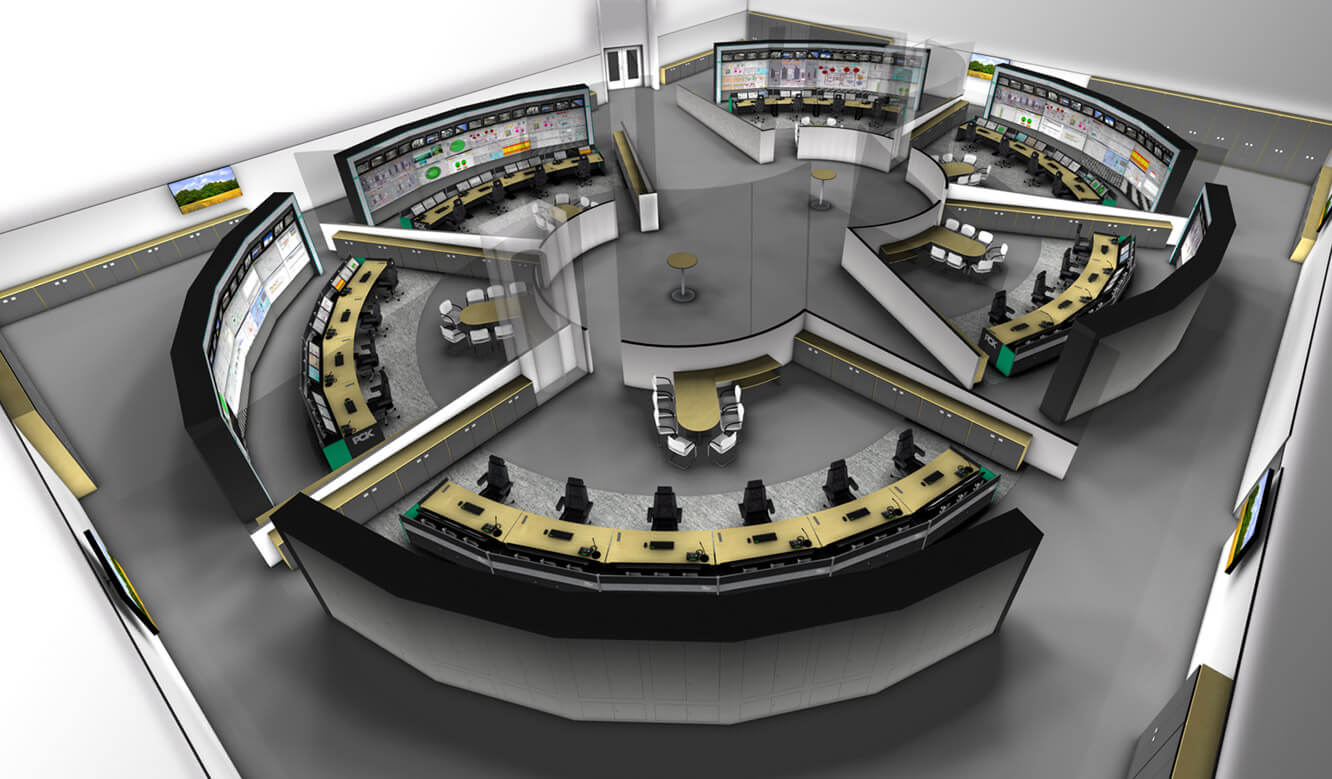
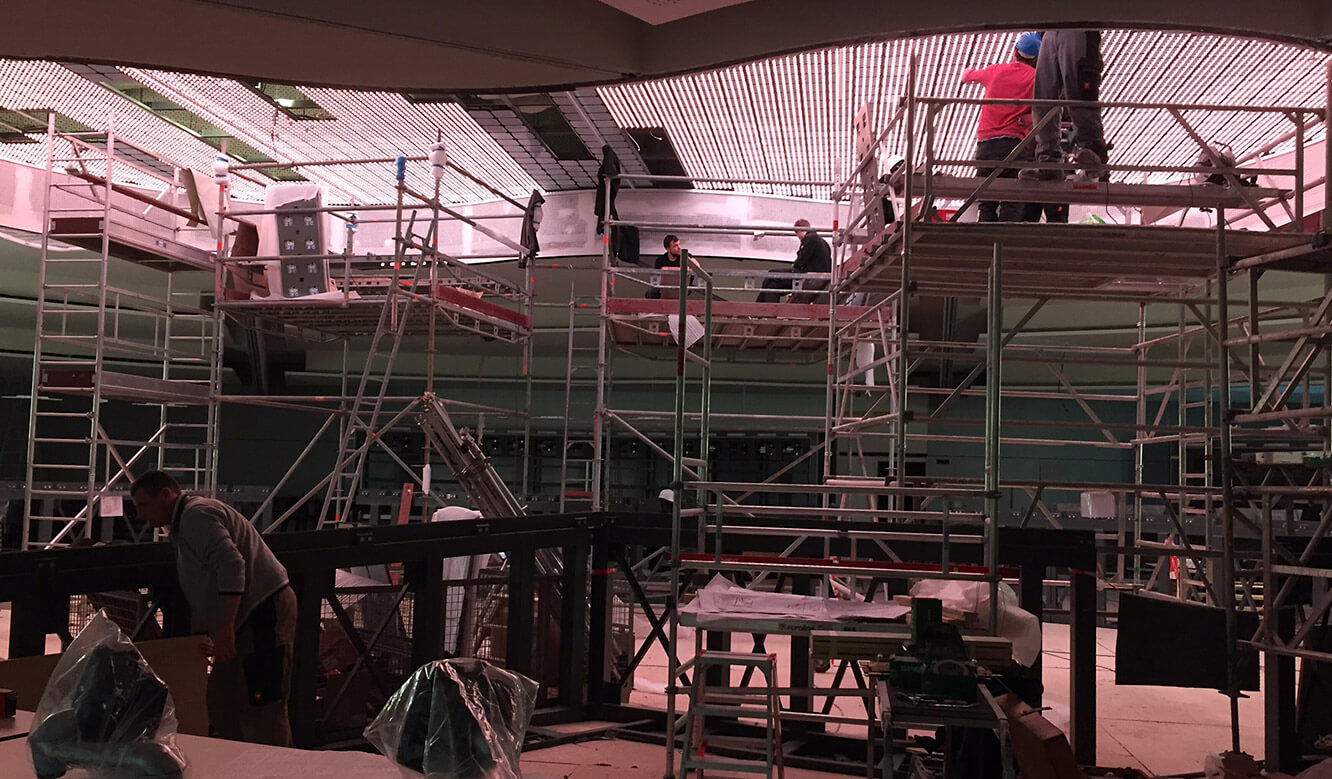
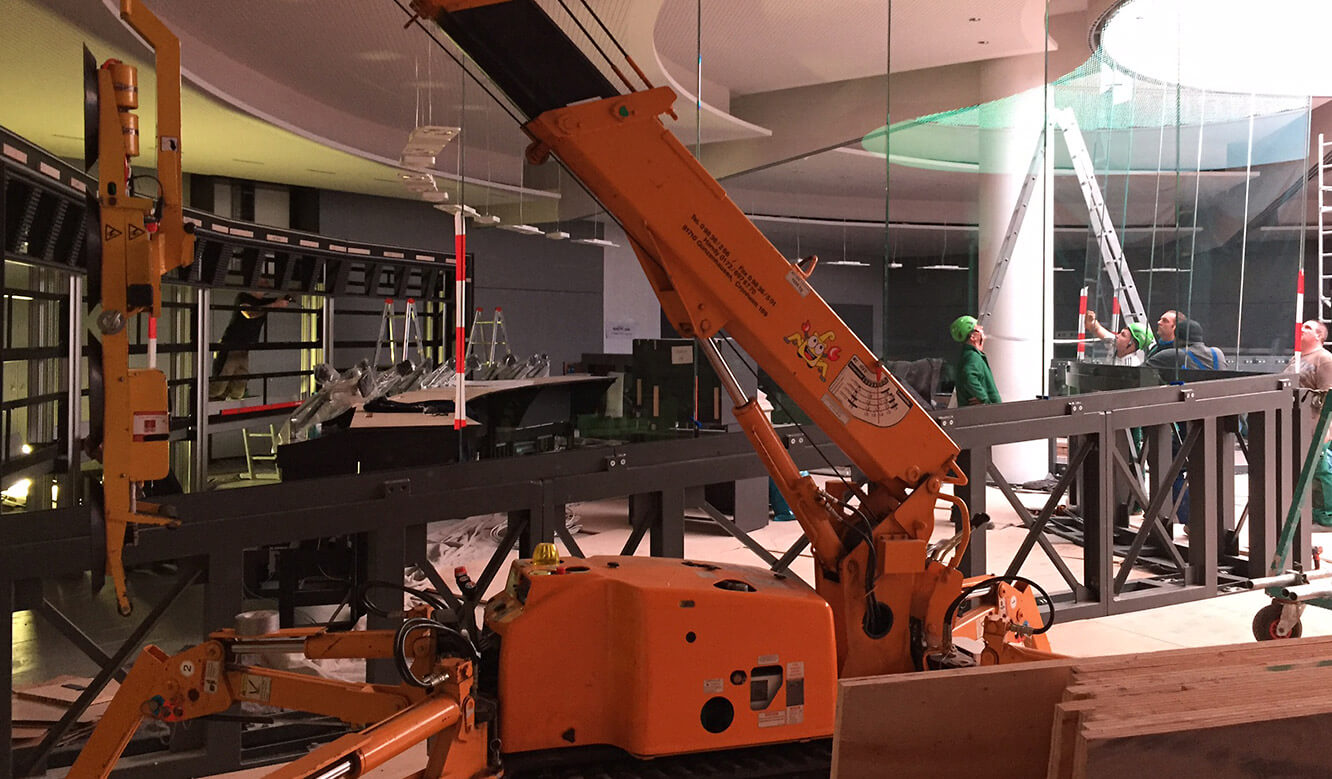
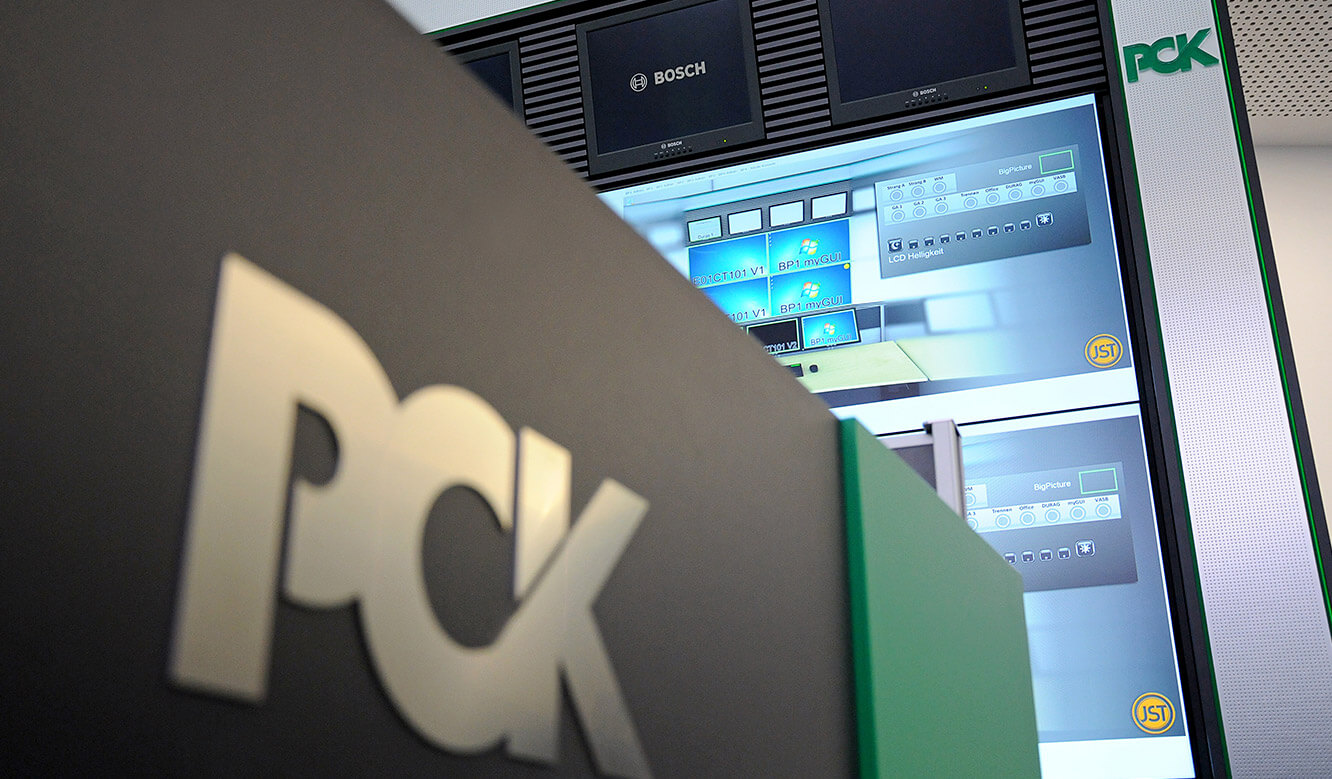
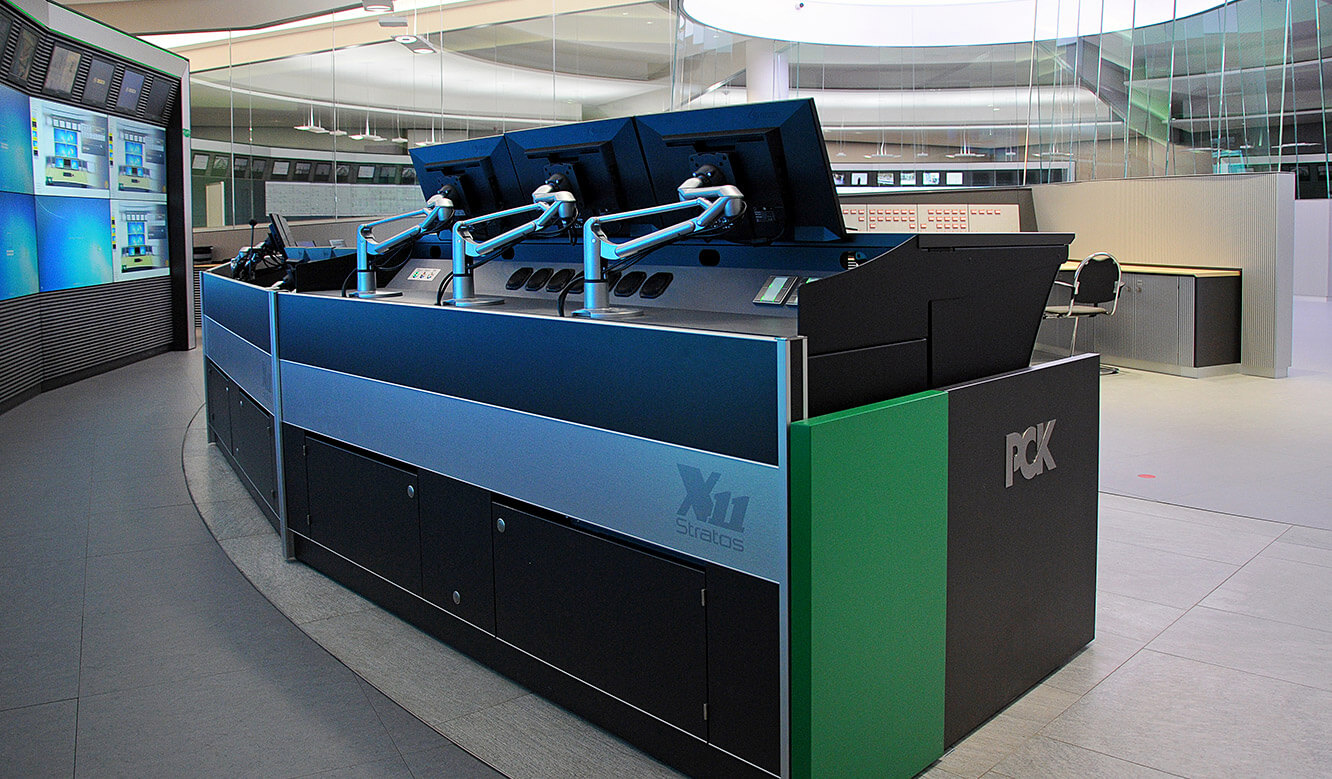
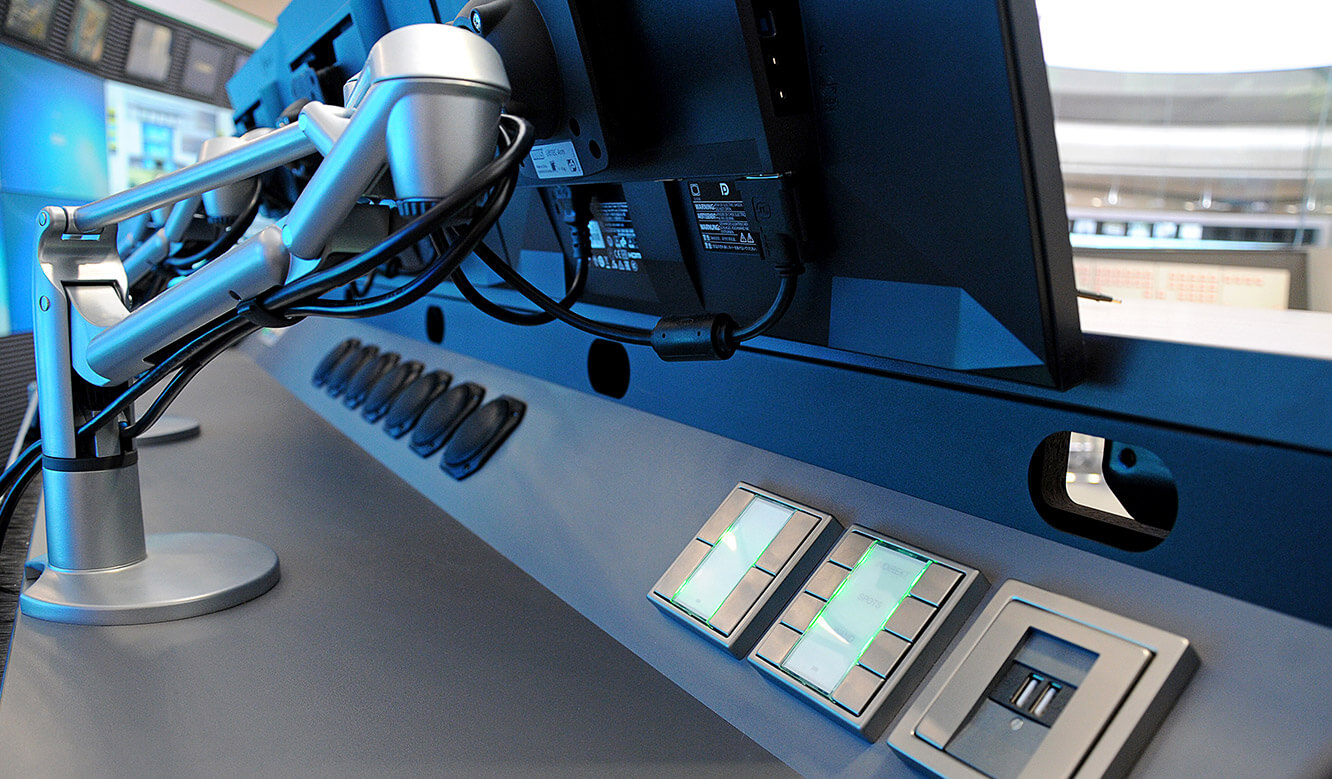
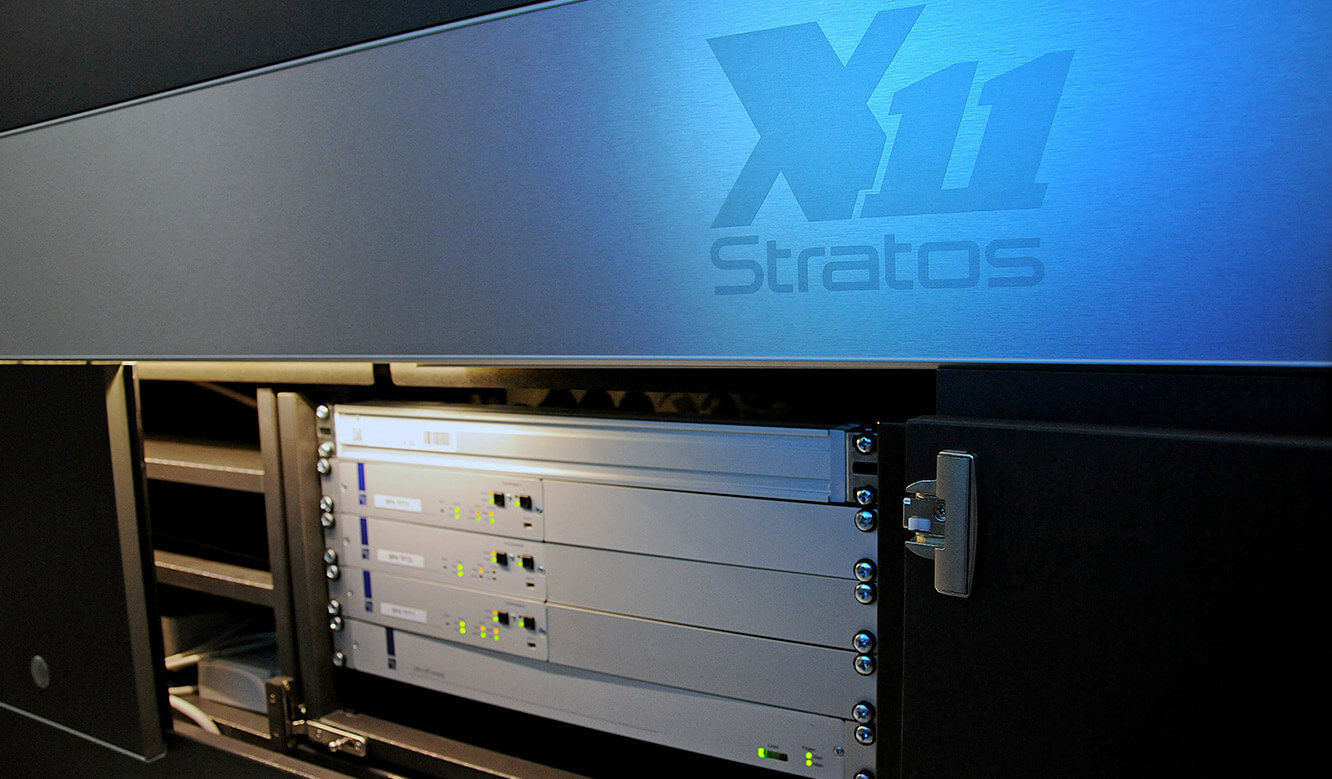
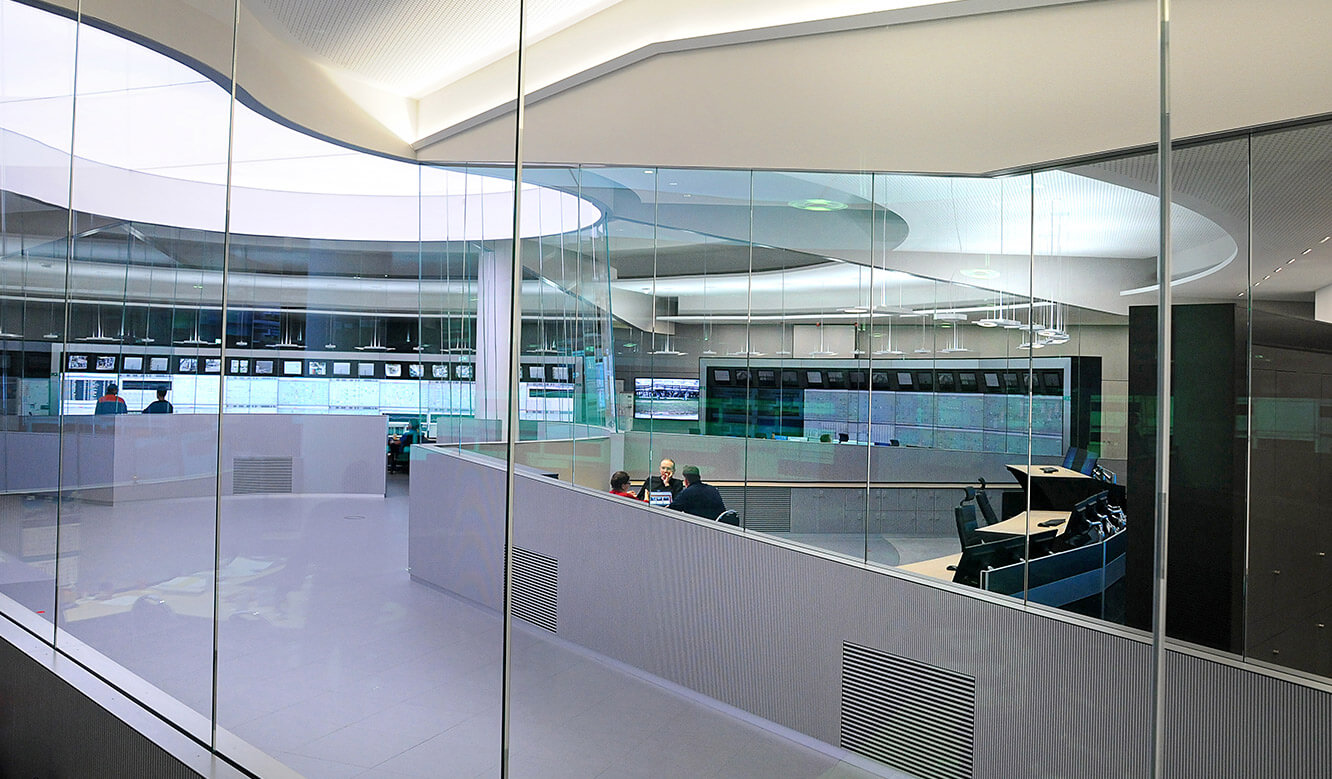
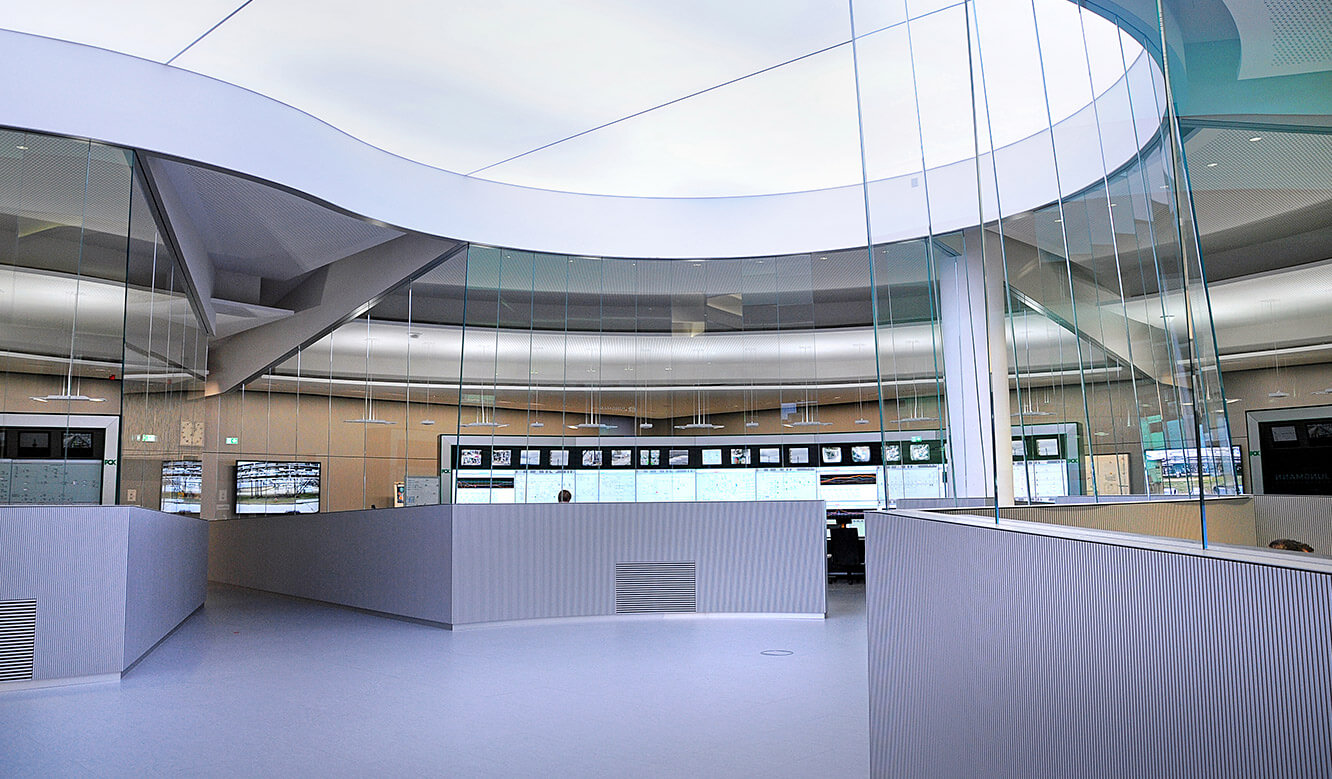
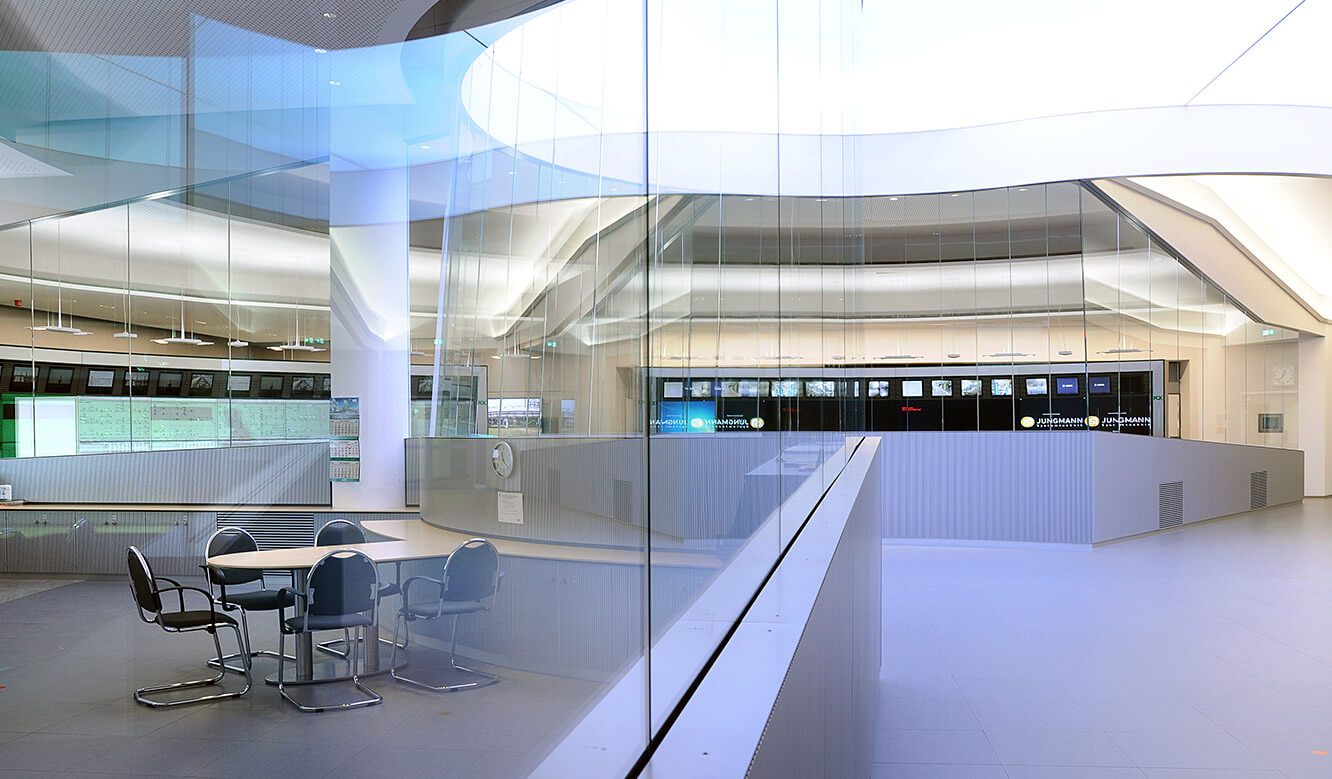
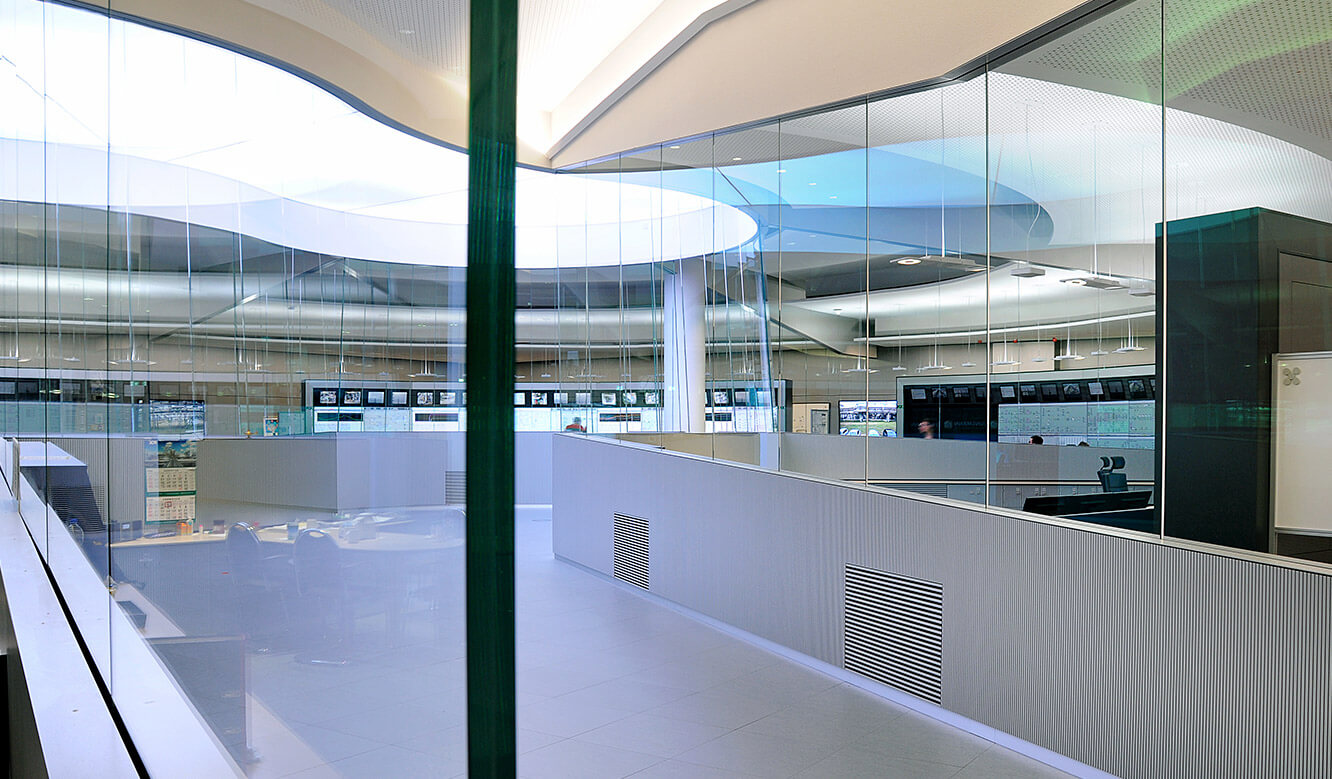
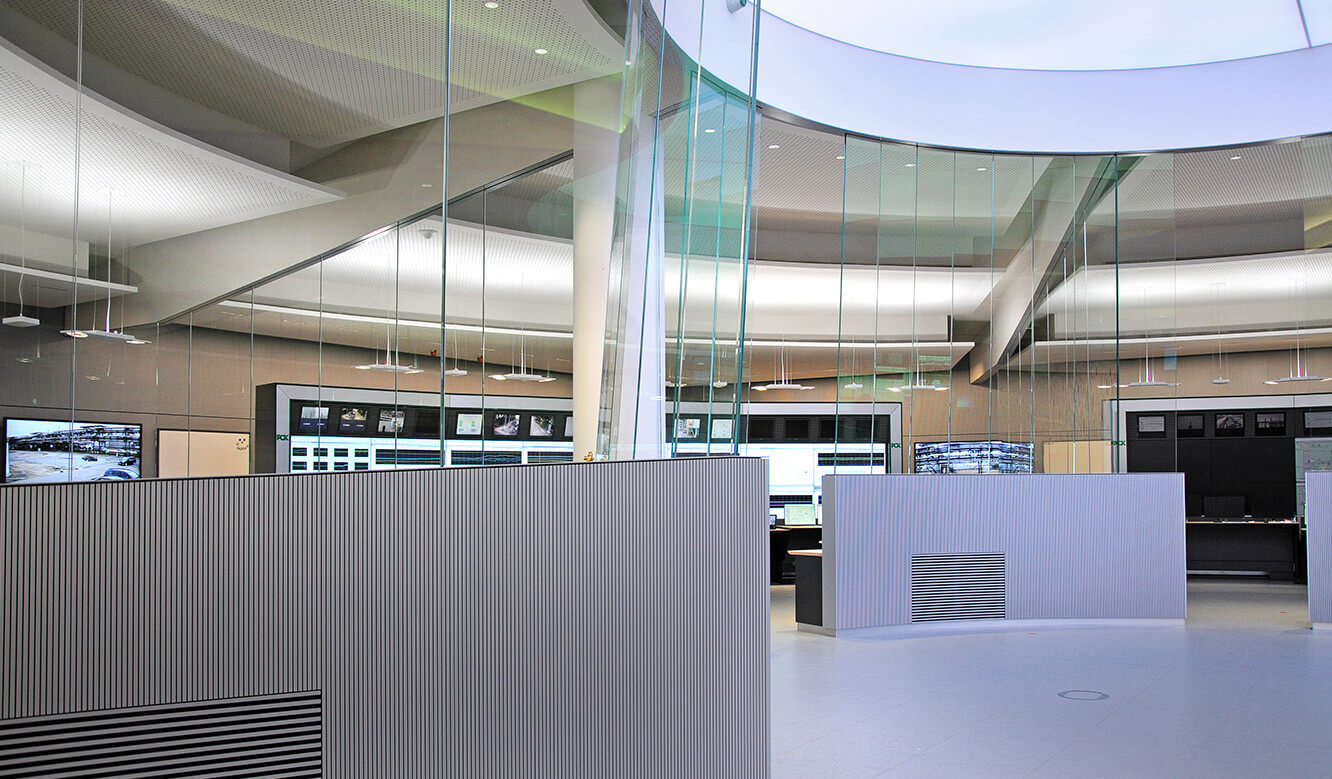
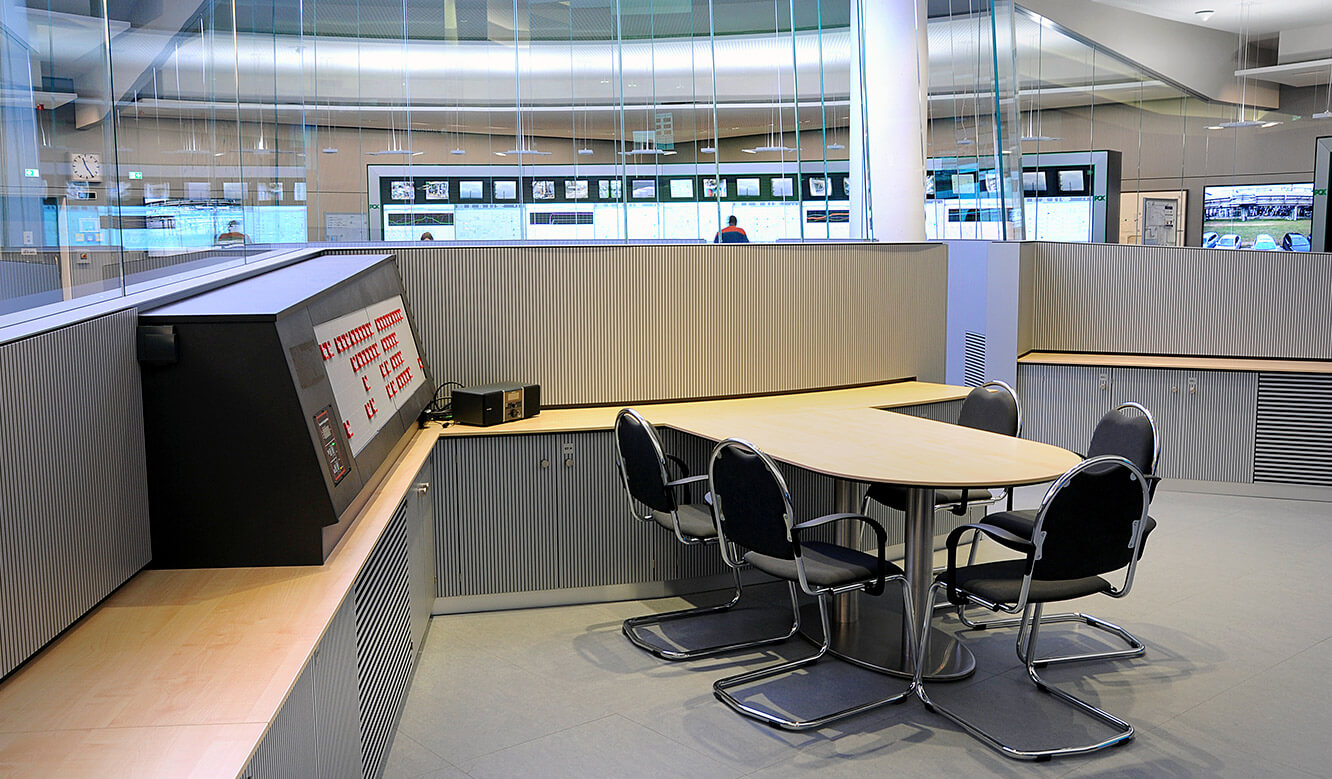
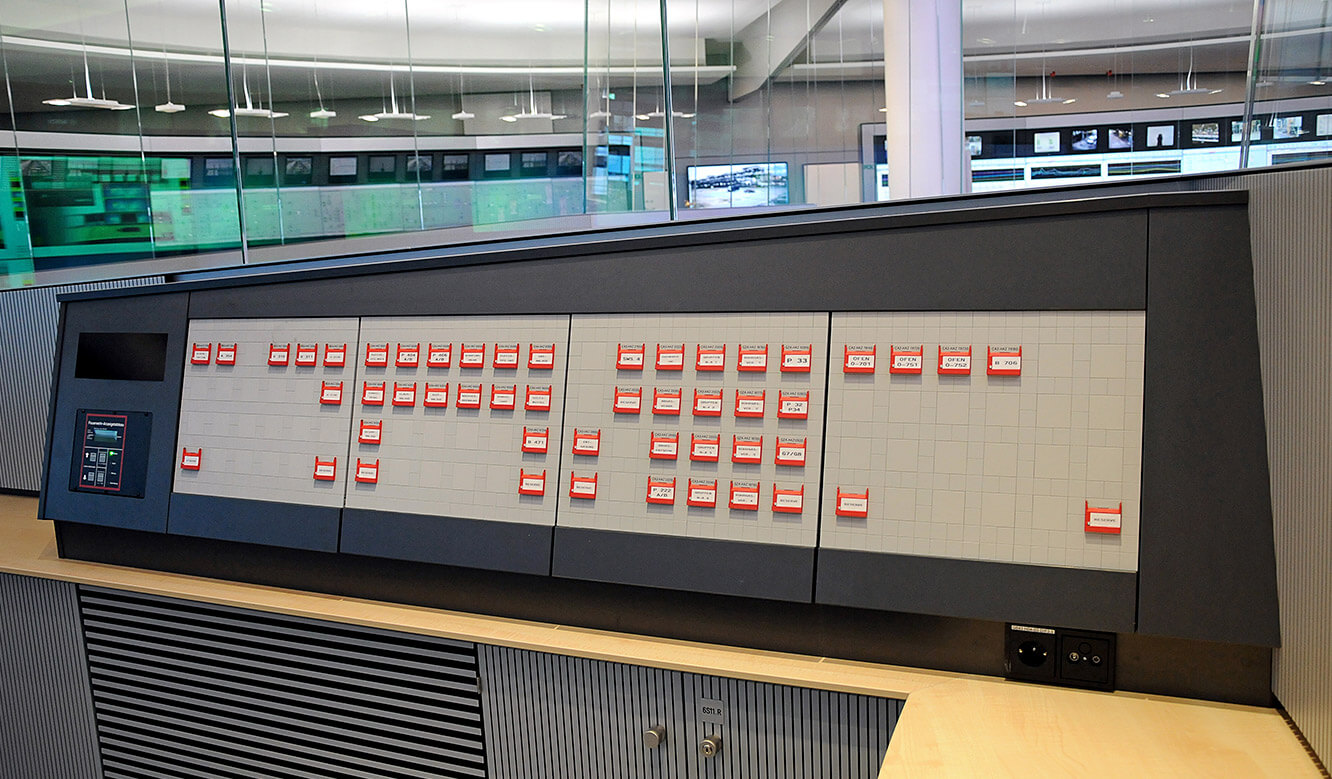
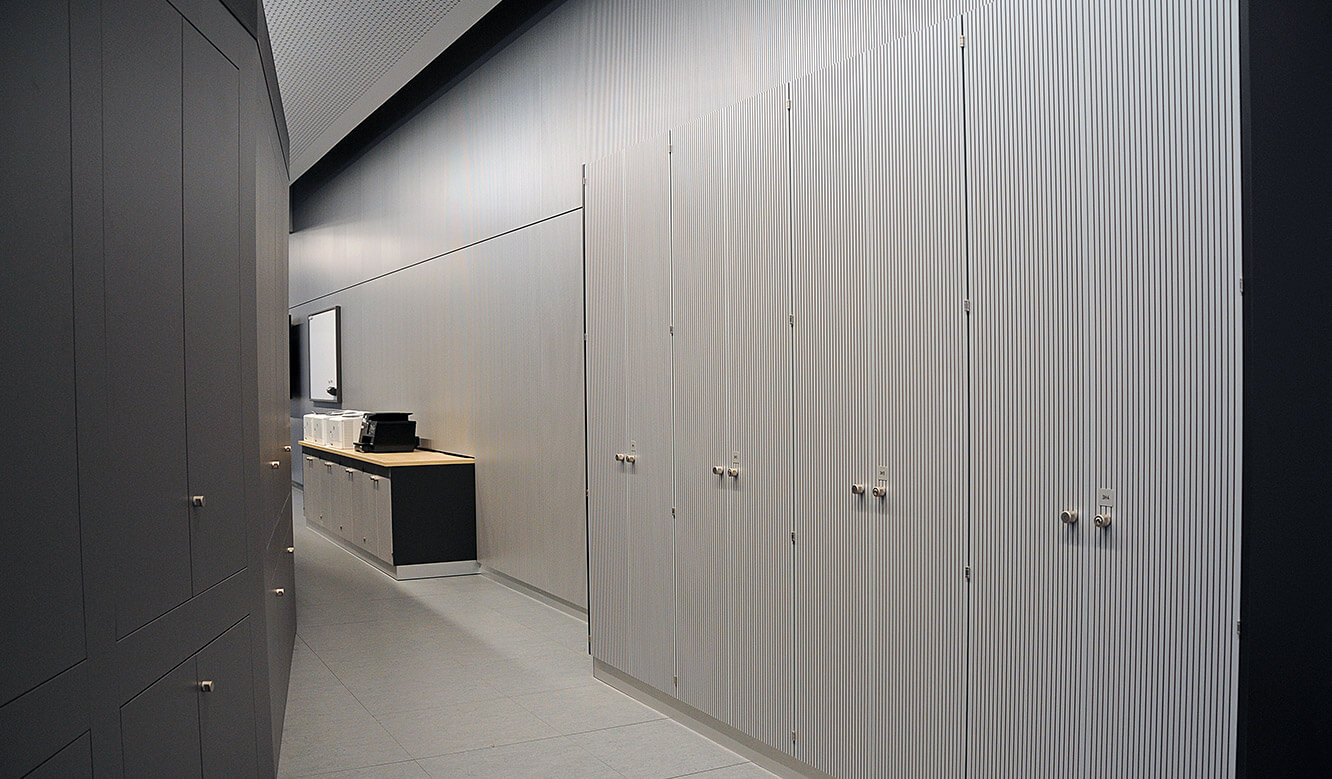
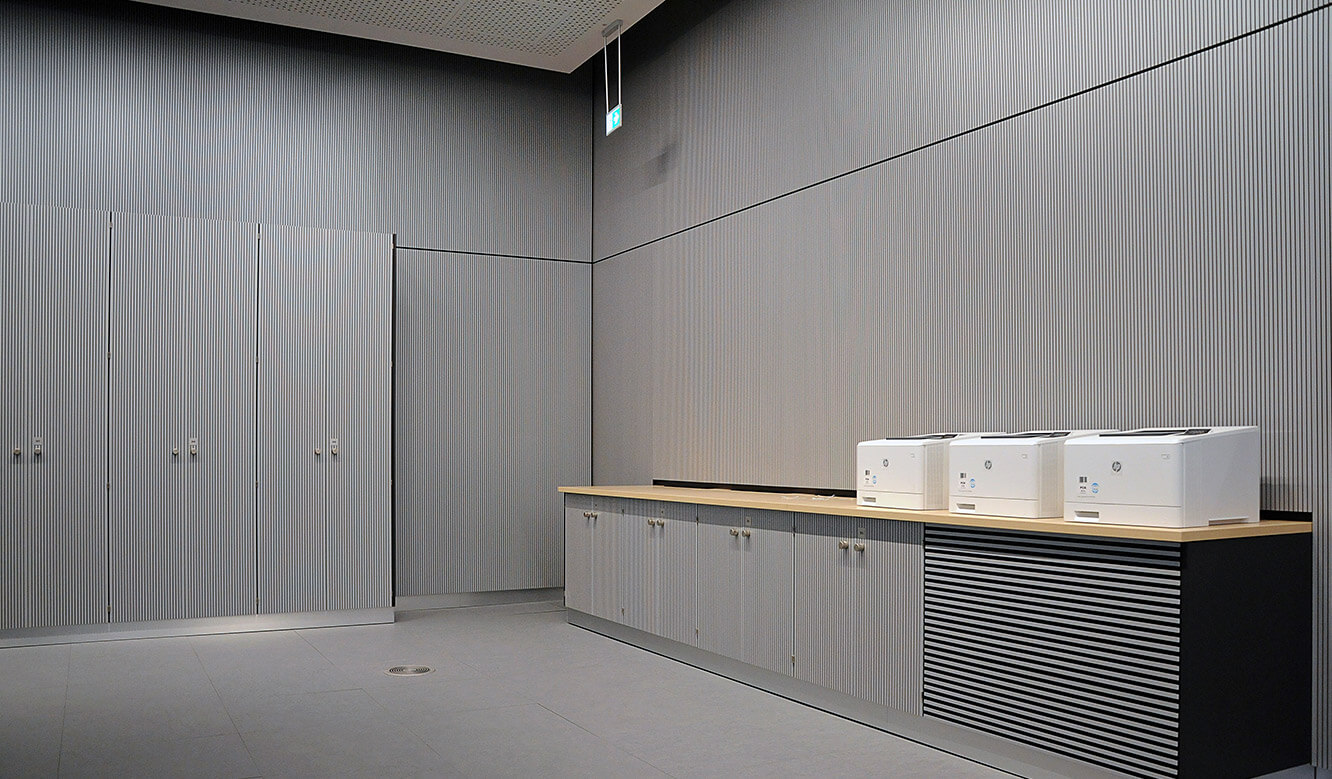
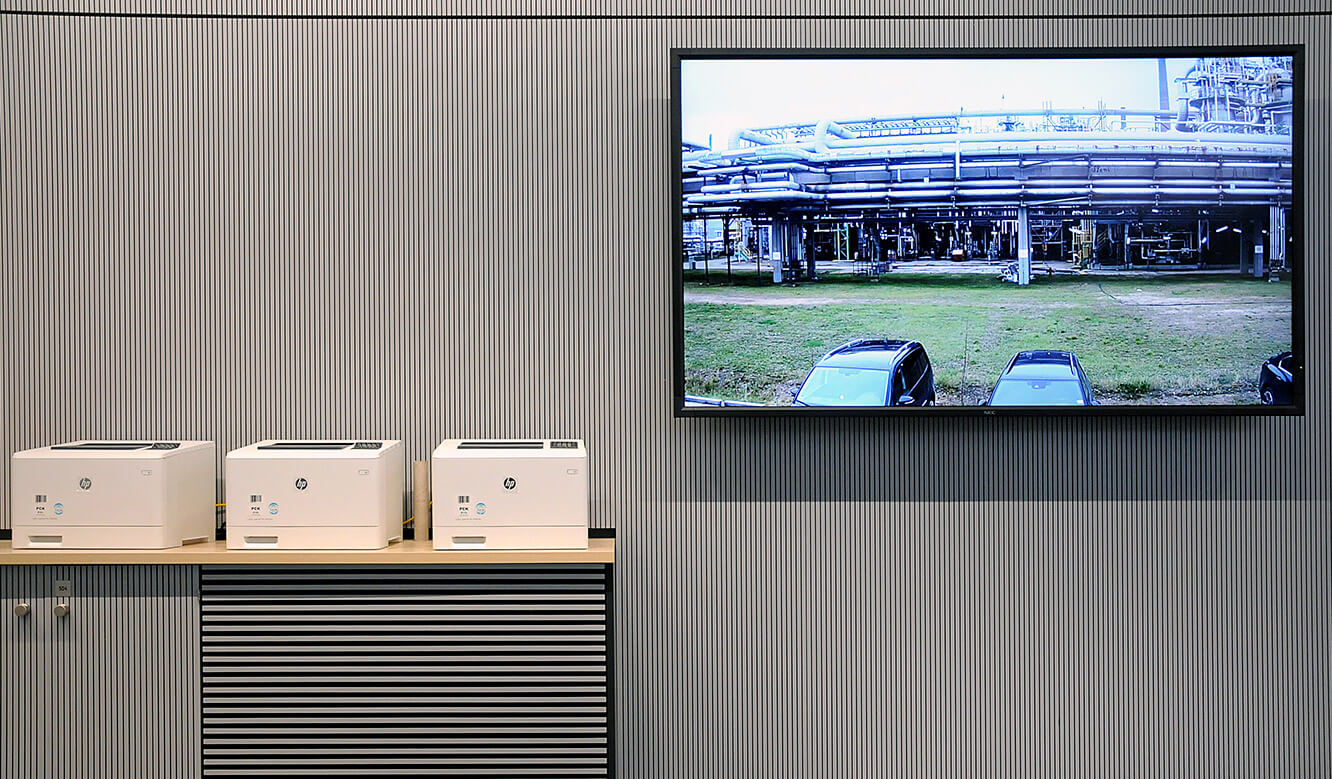
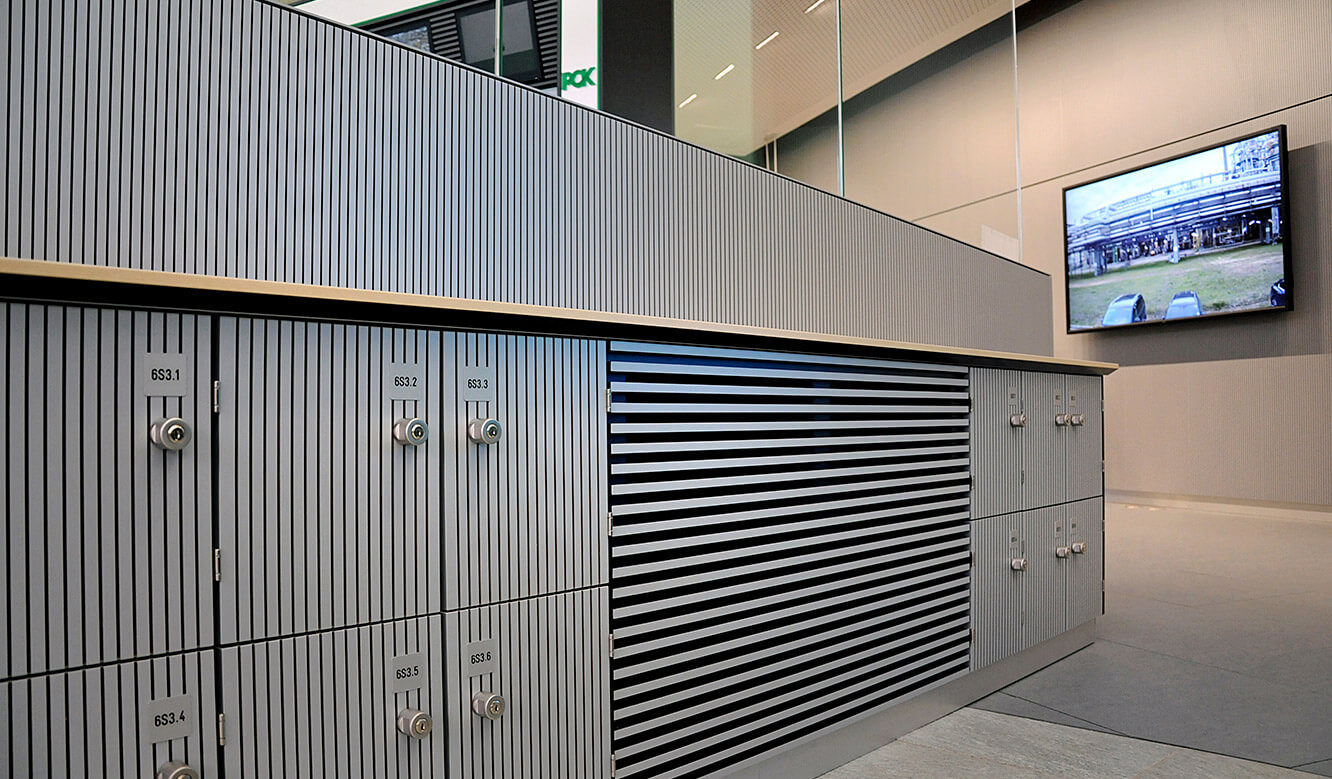
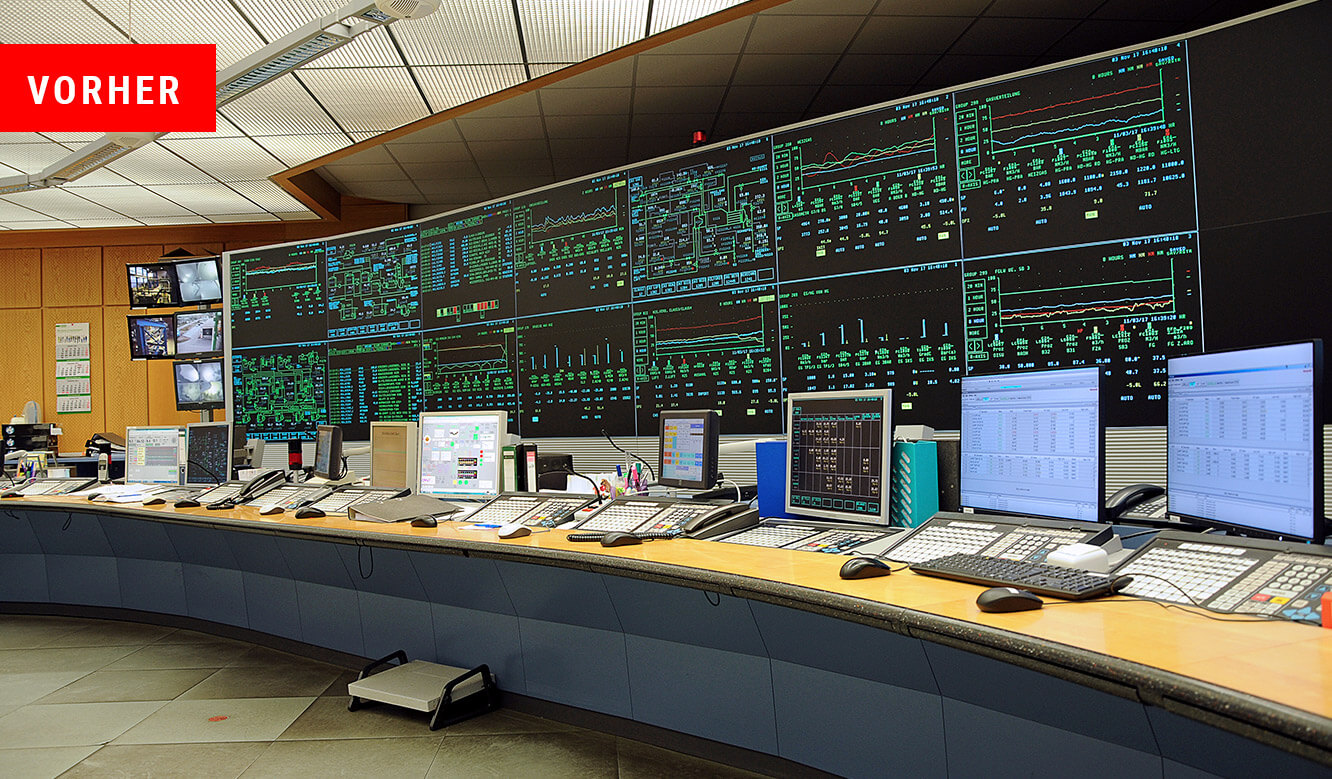
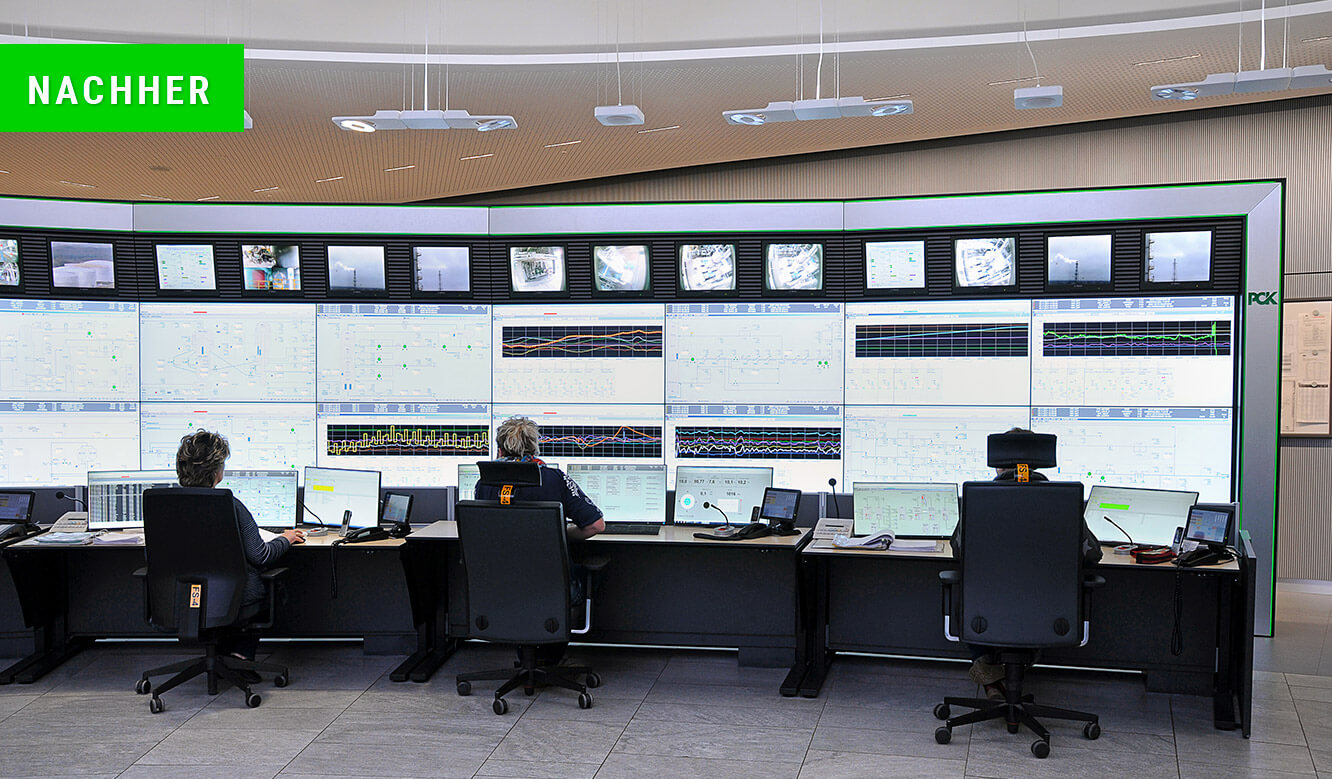
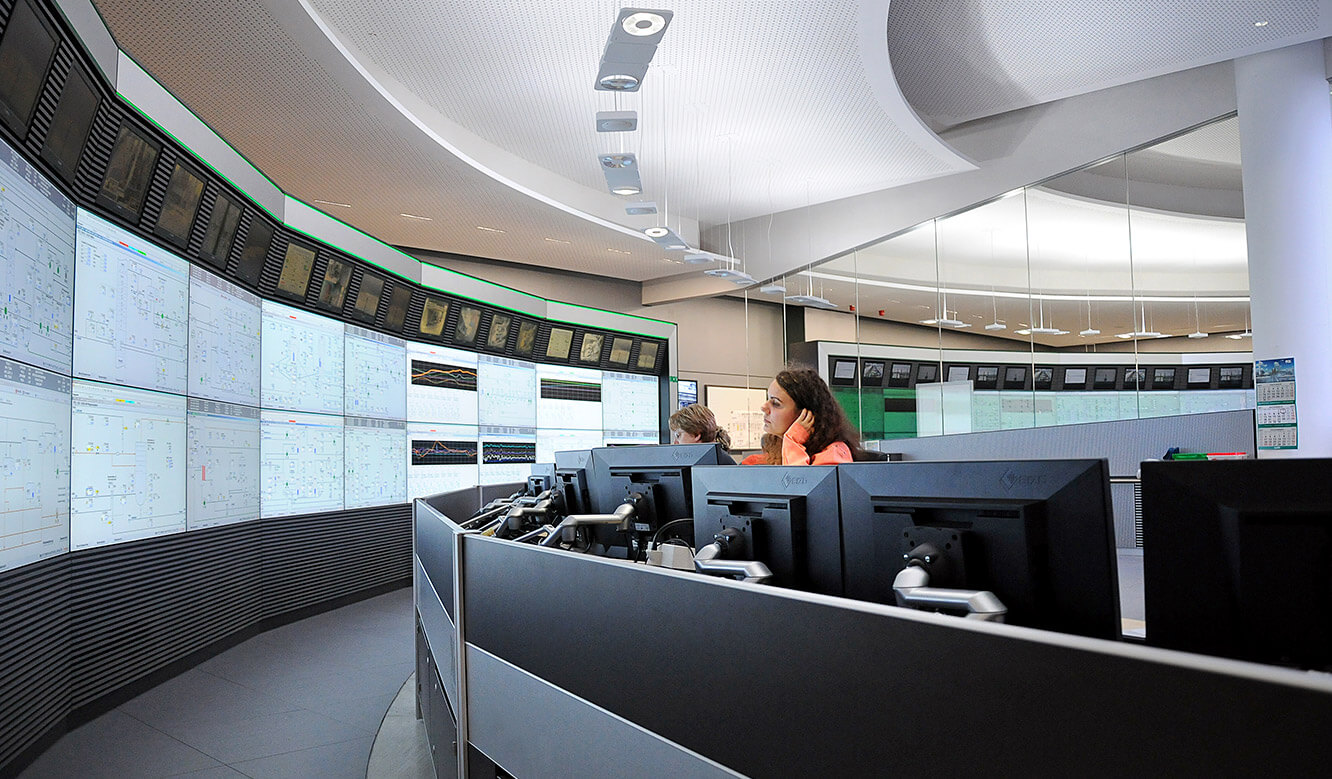
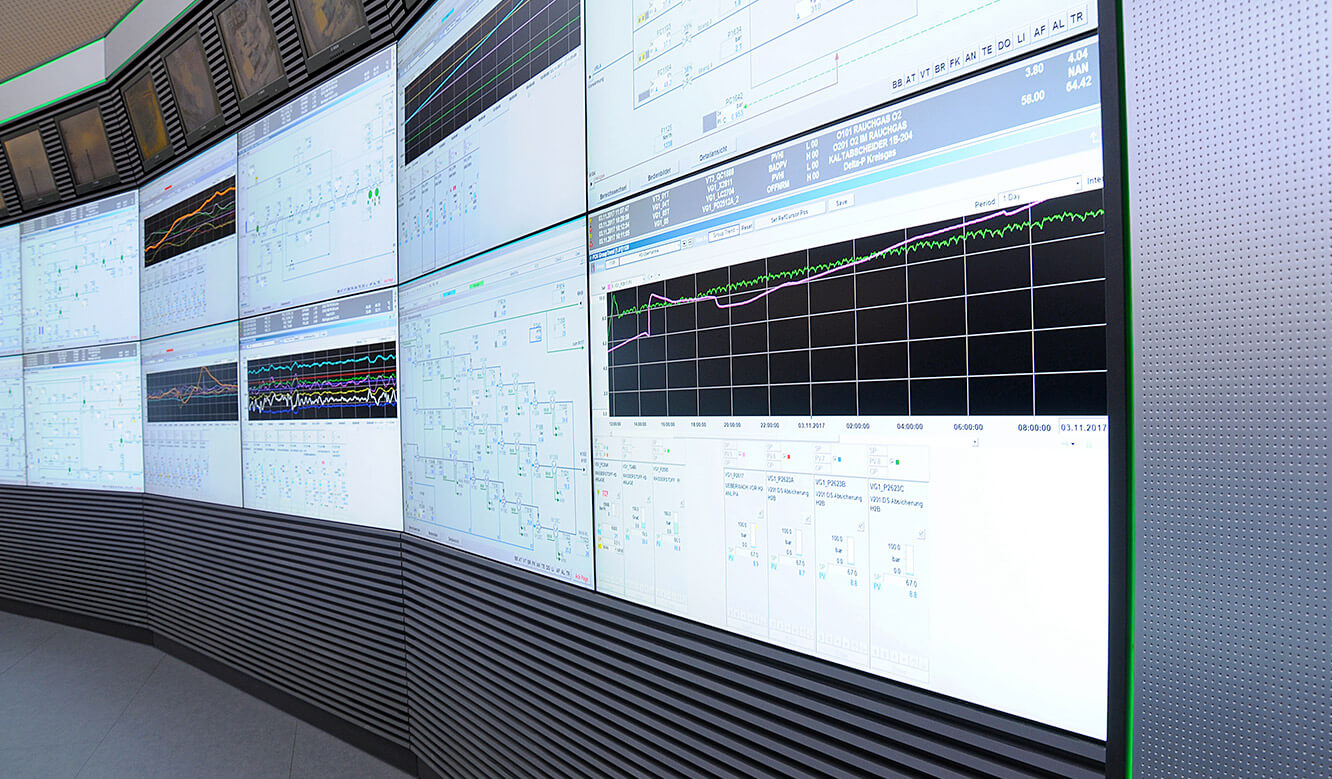
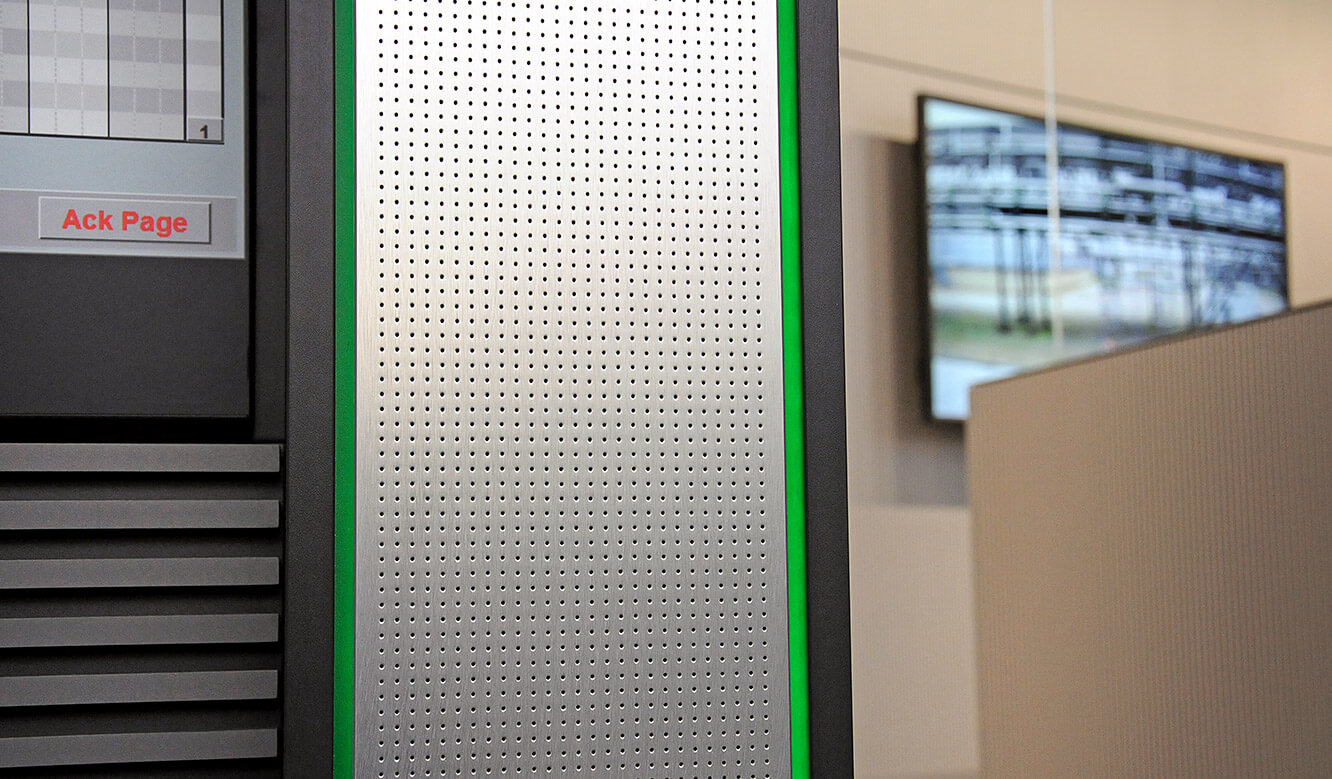
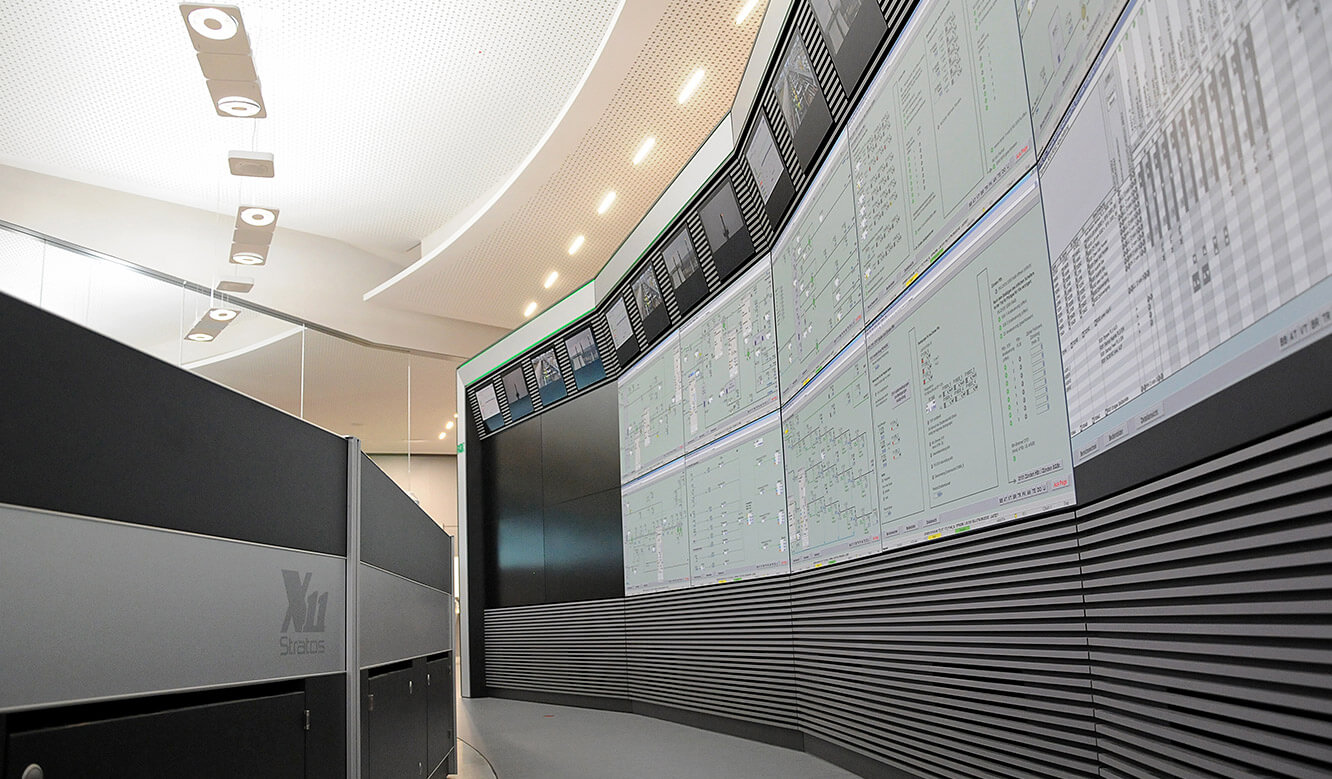
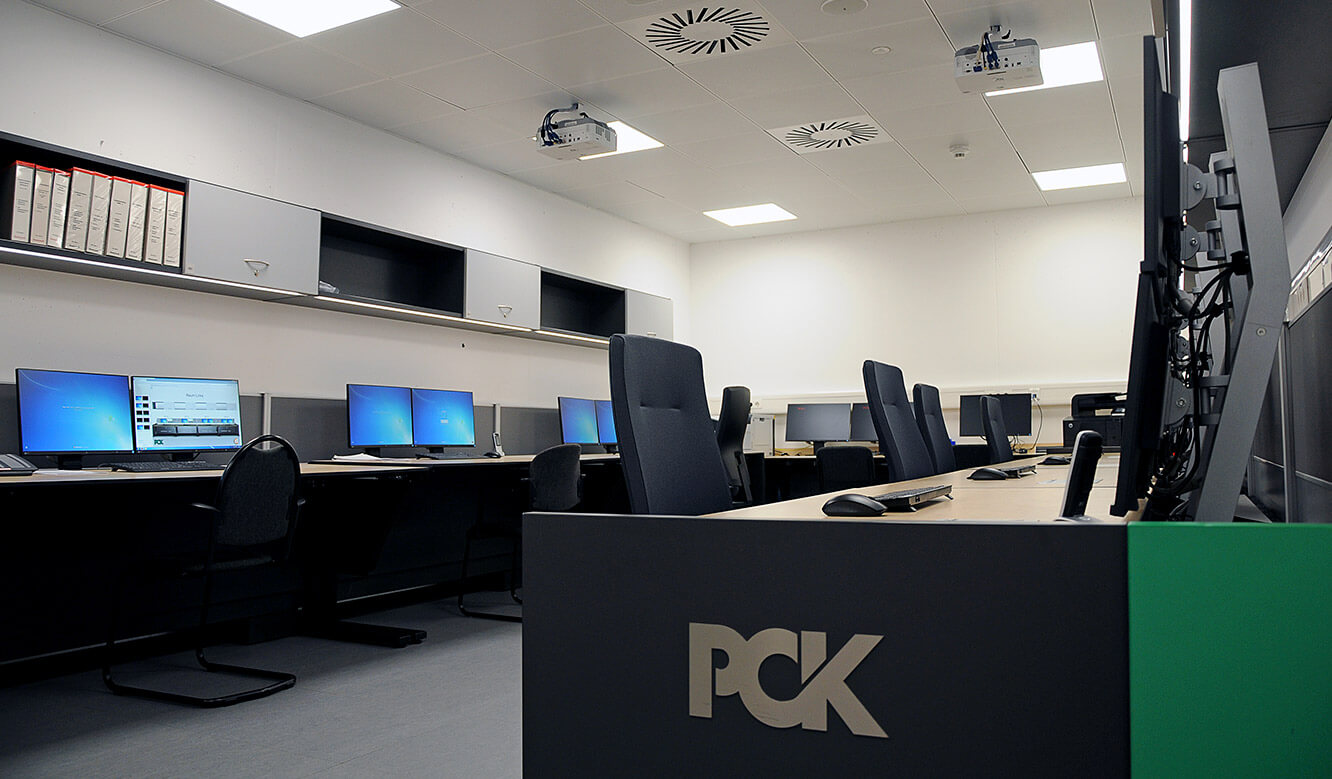
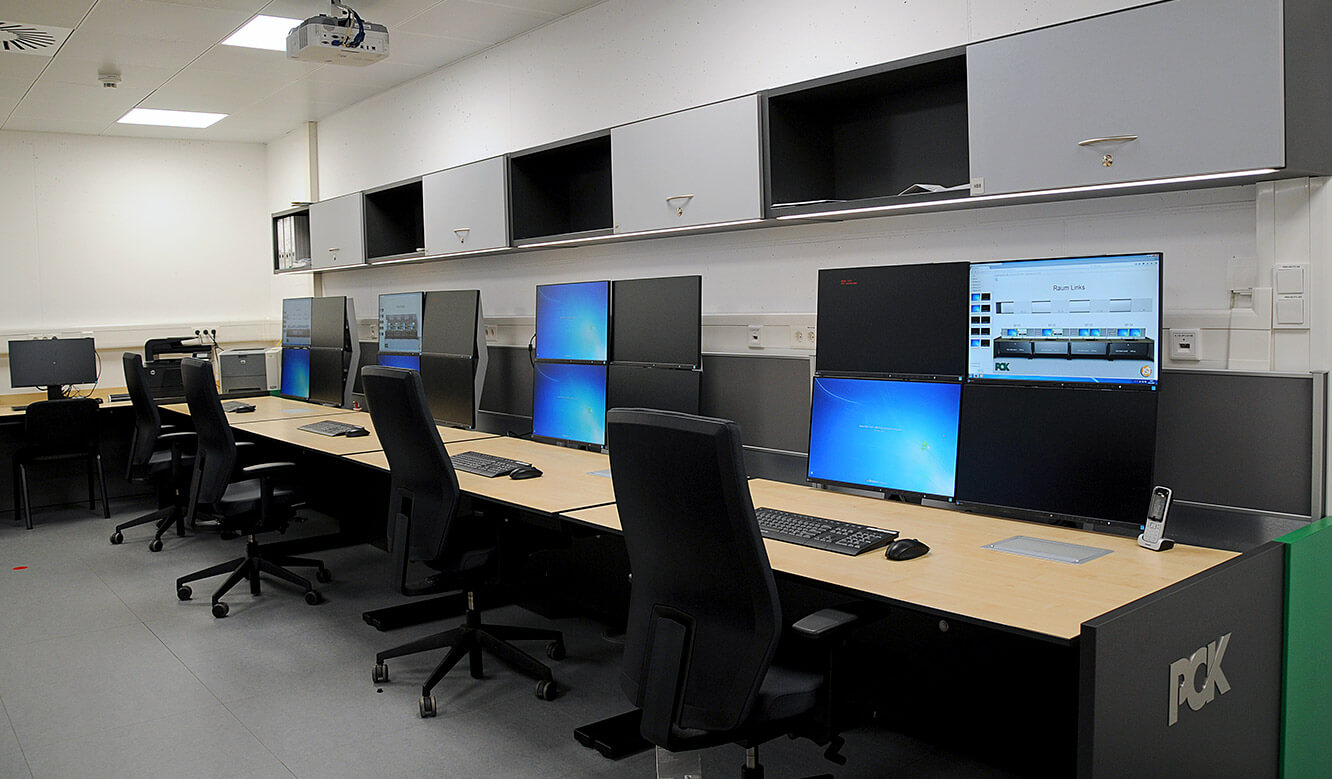
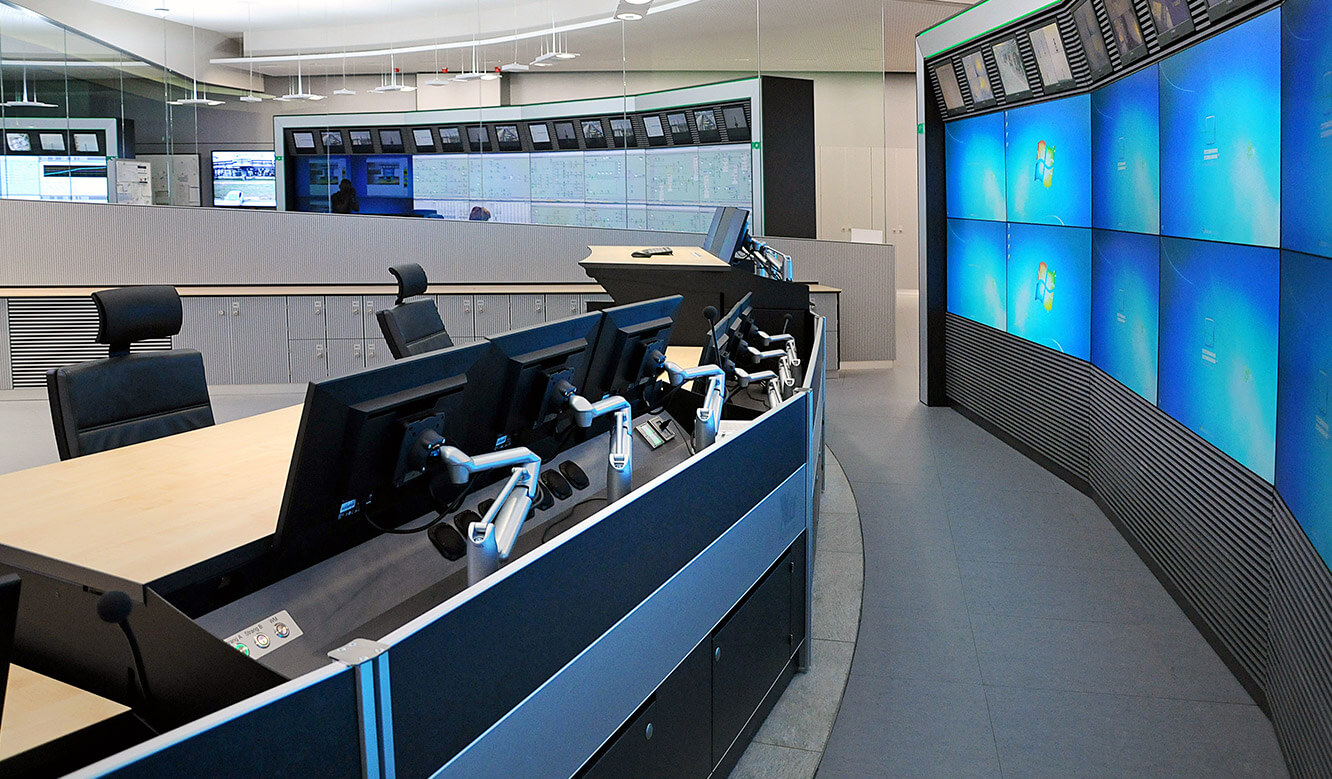
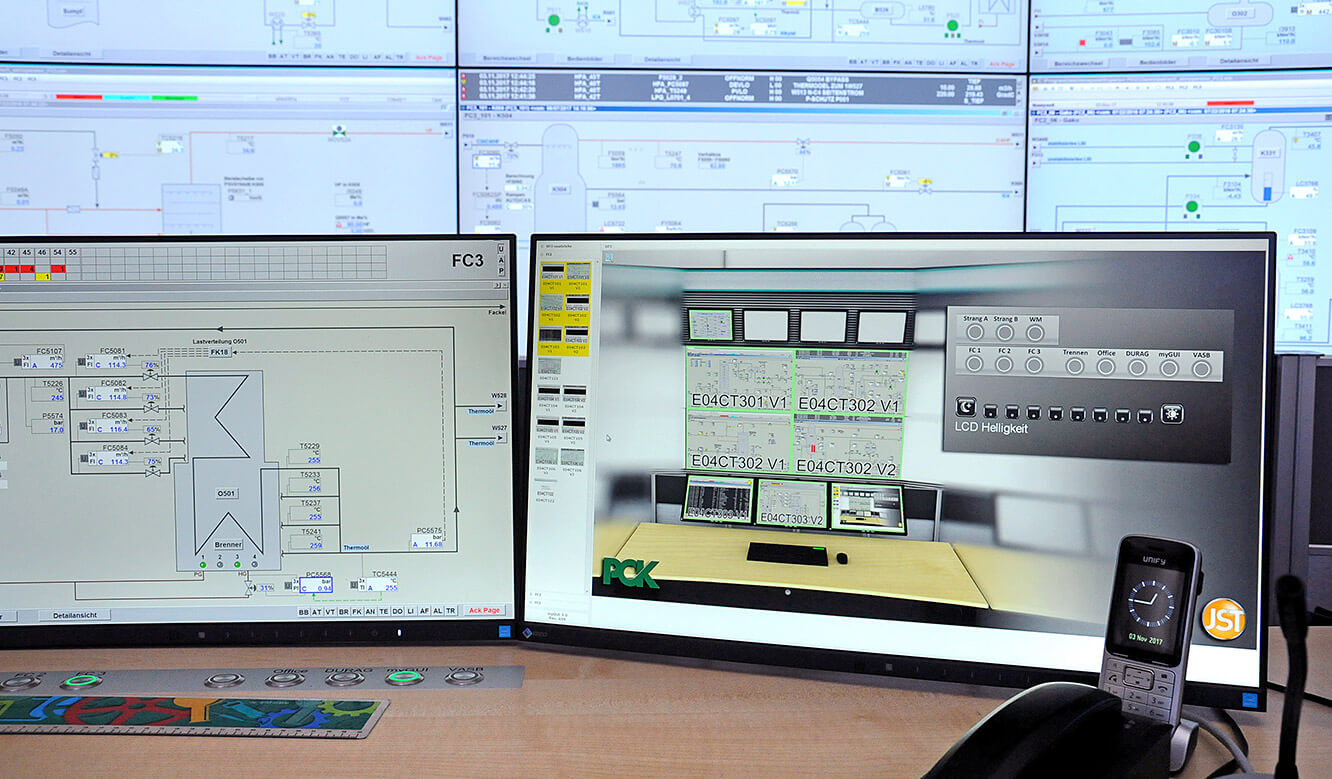
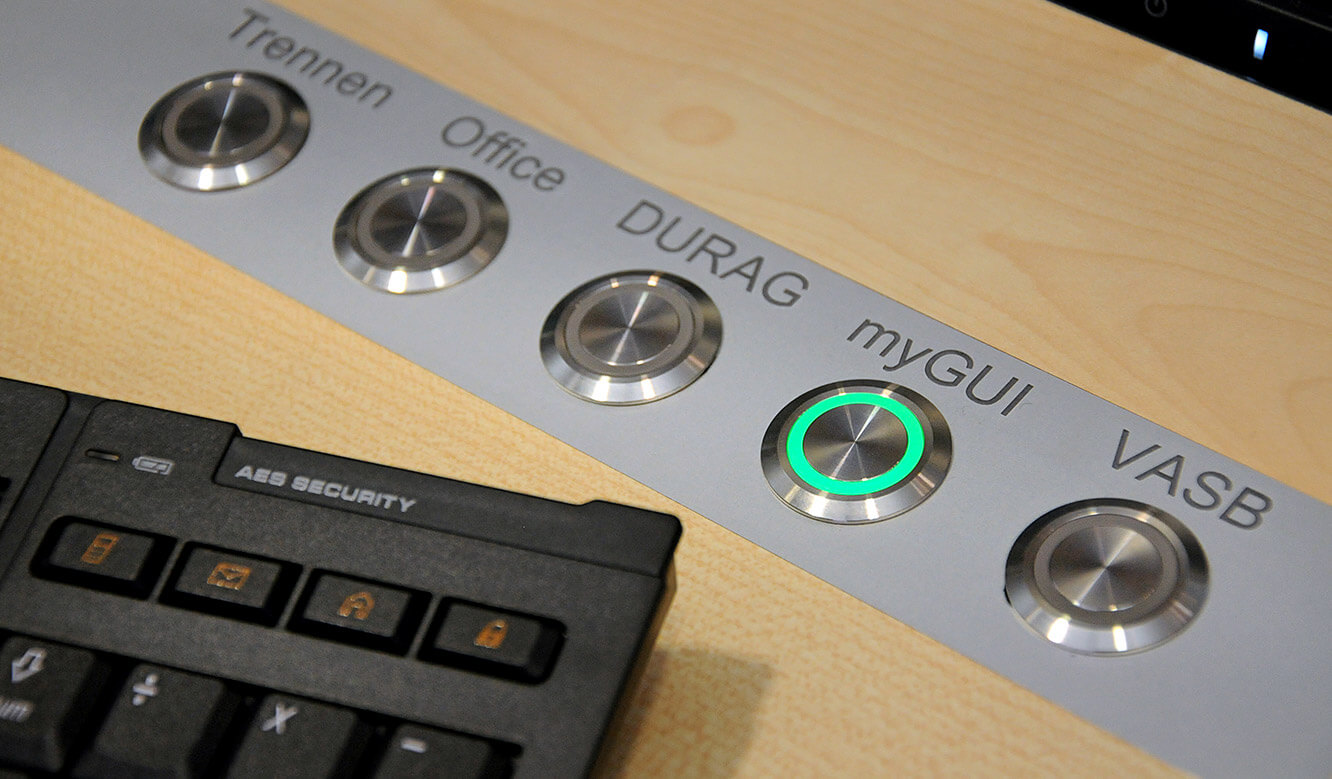
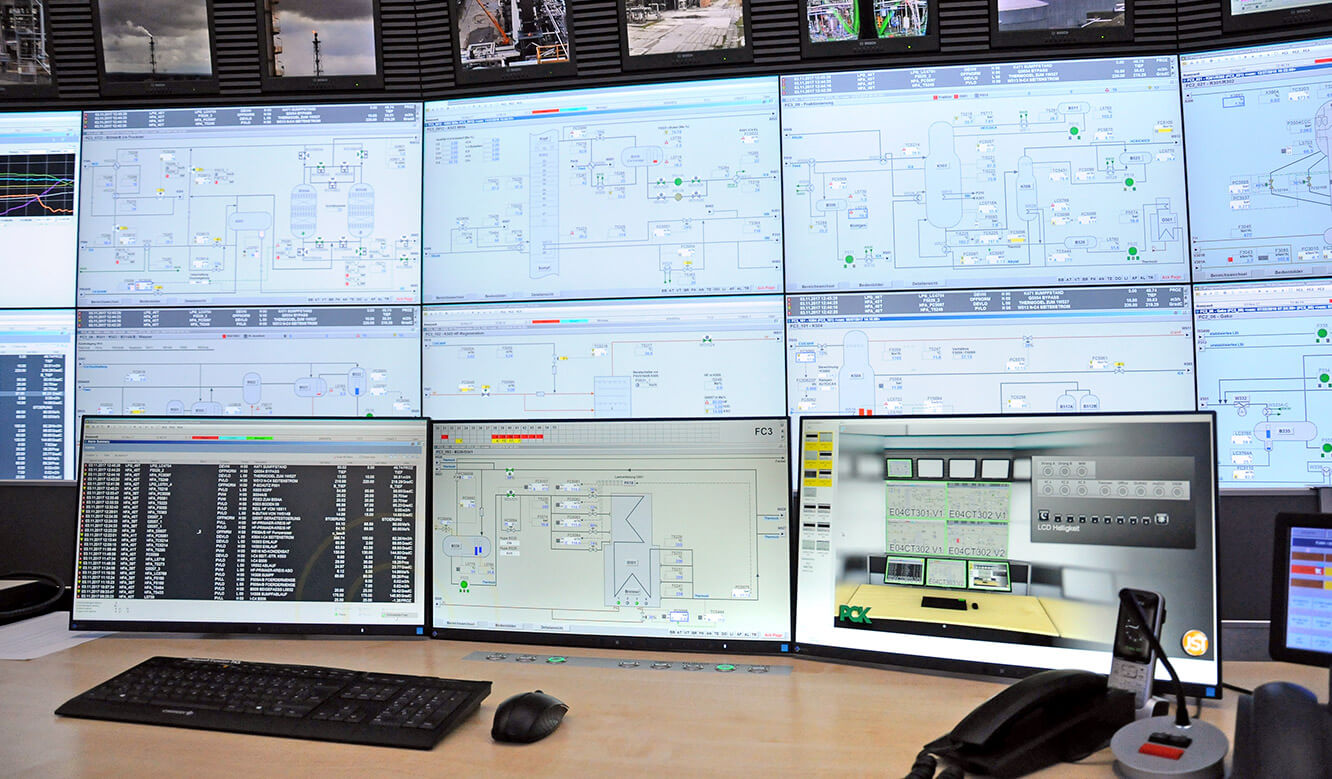
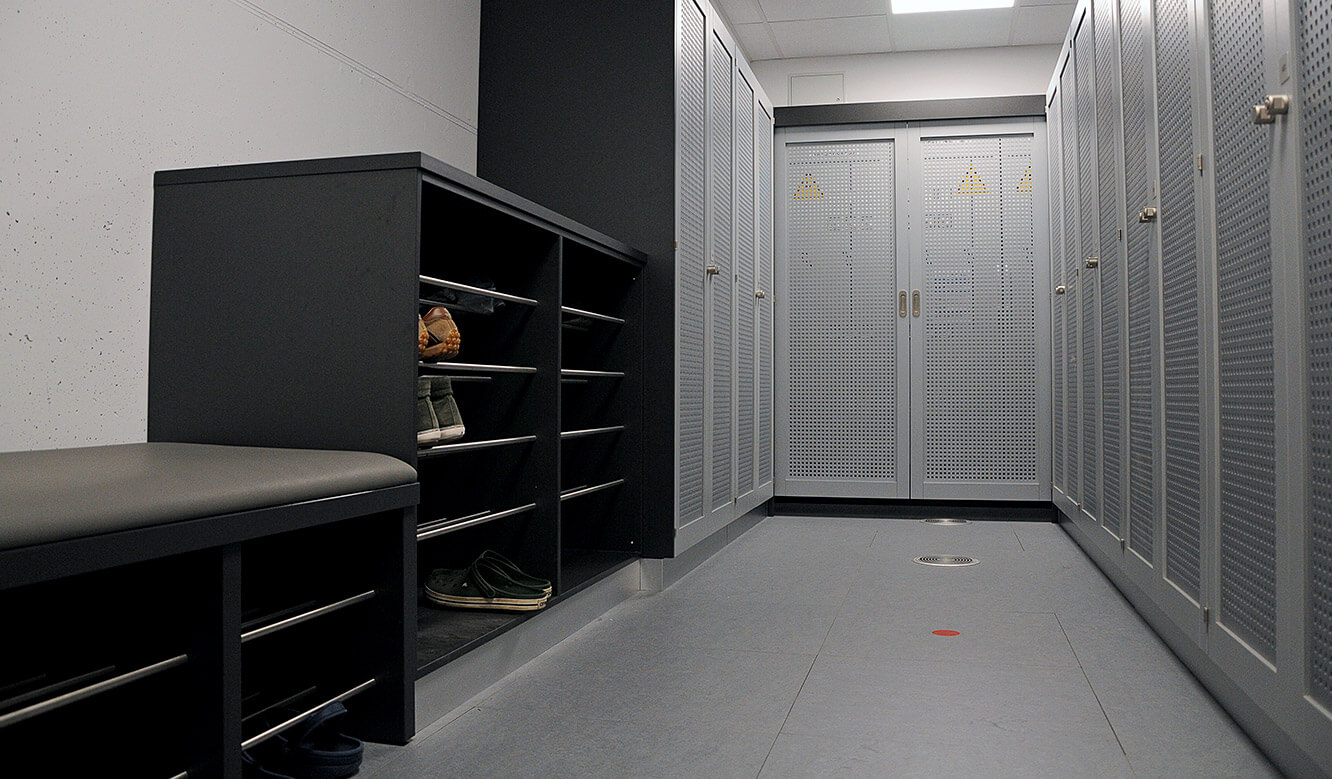
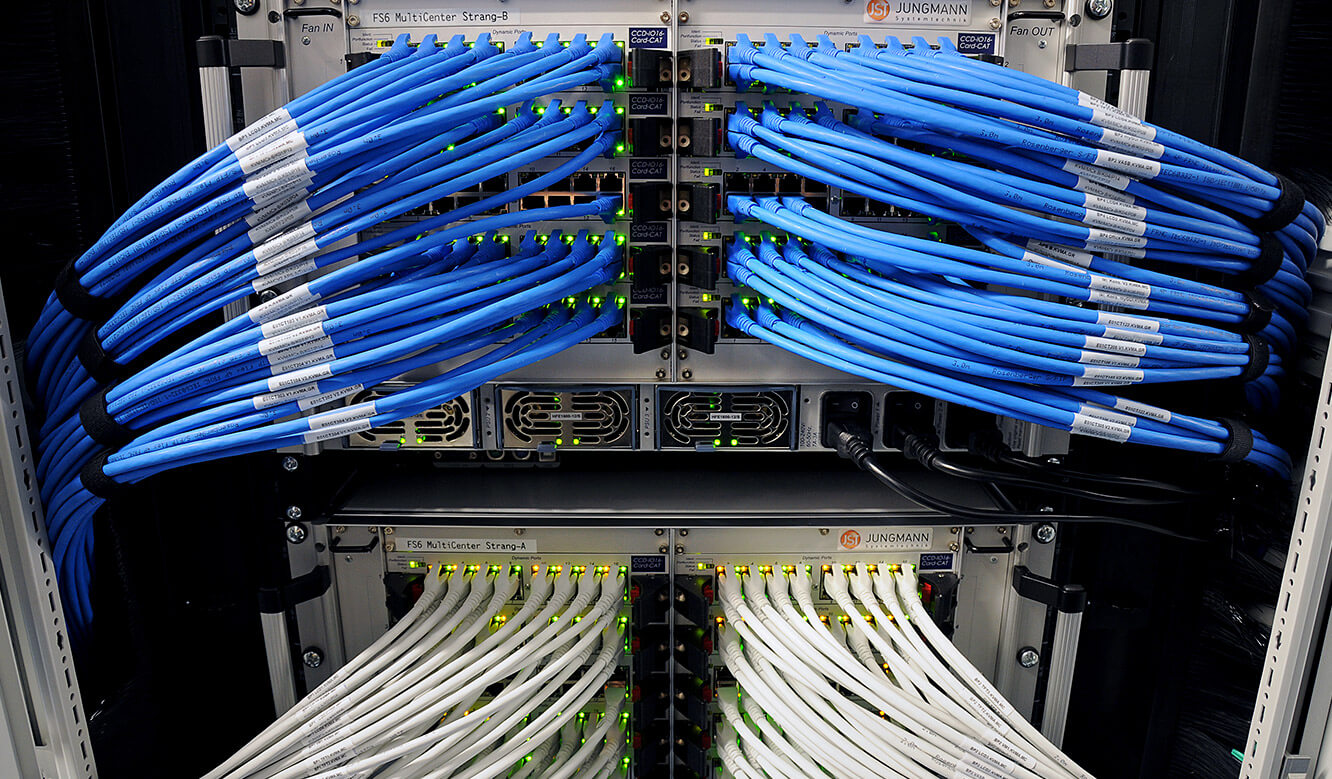
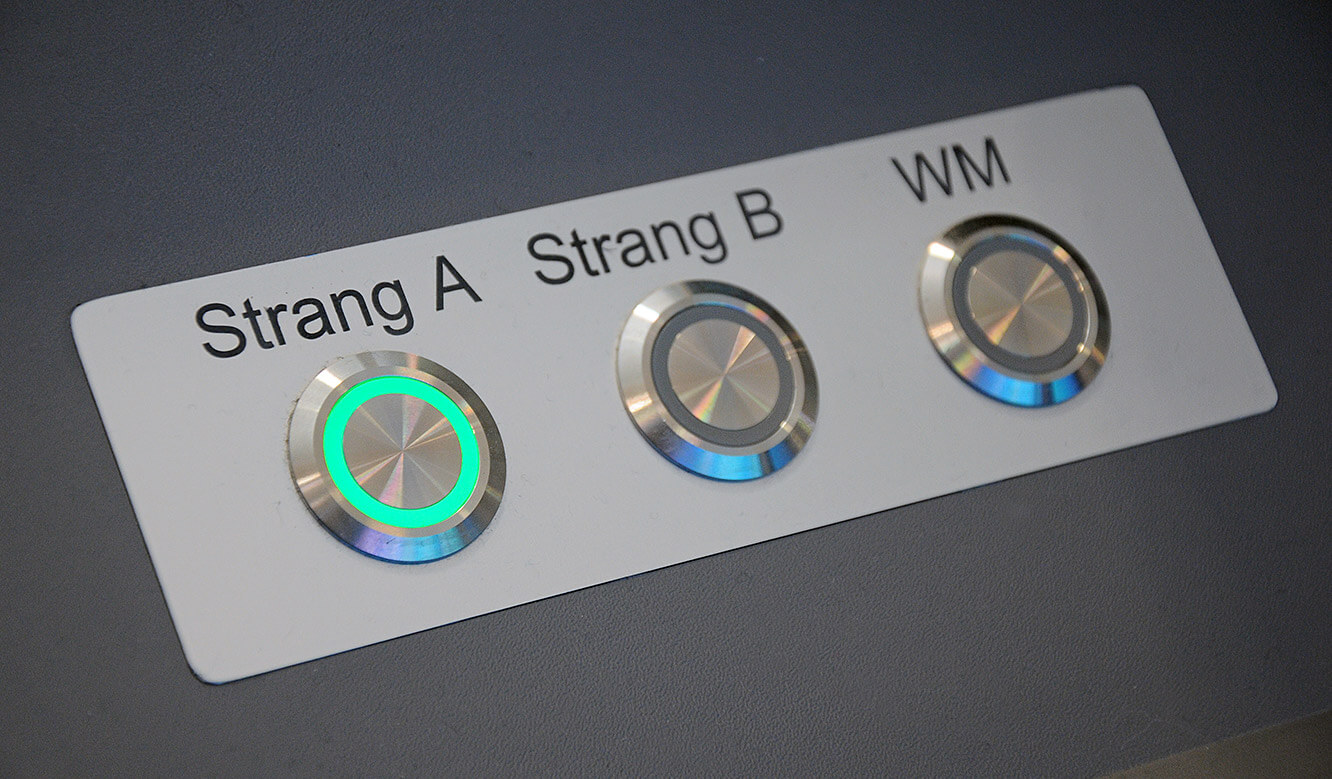
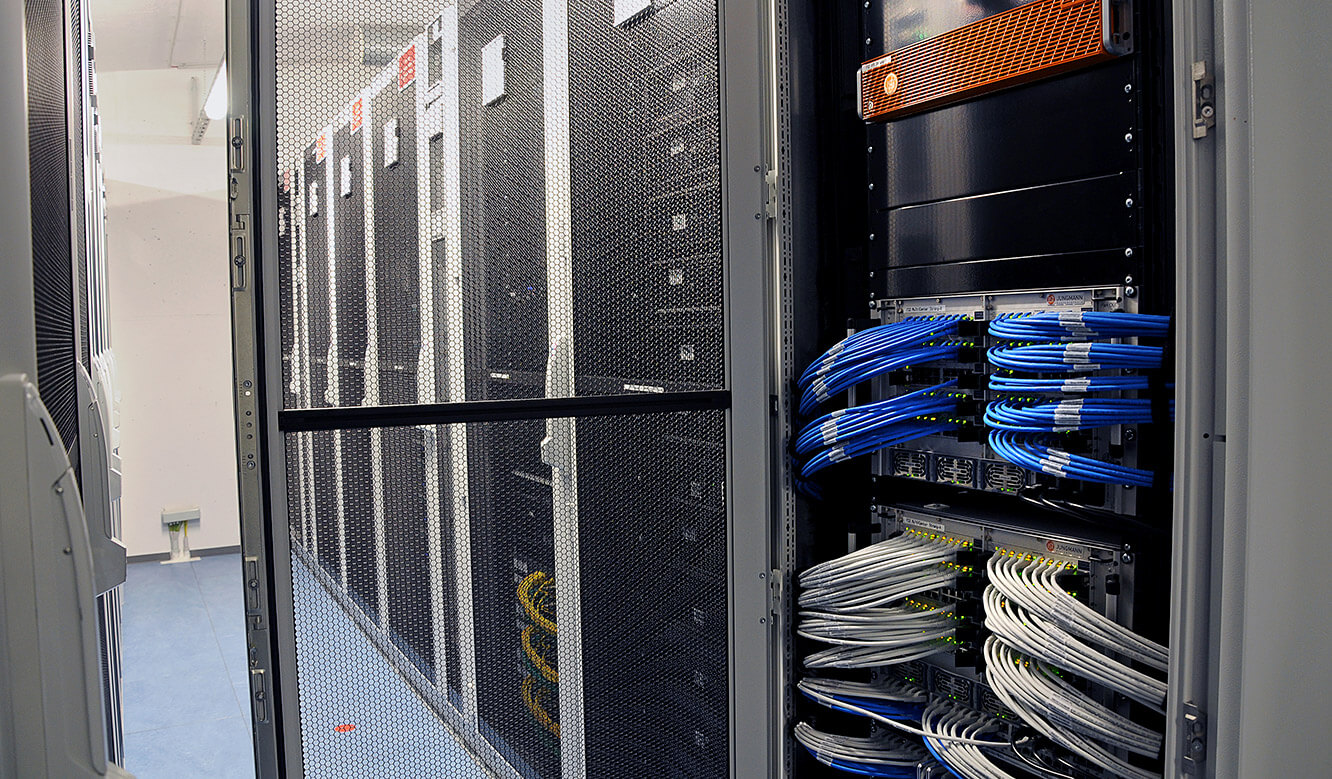
Photo 1 | JST control stand: View through an anti-reflective glass pane into a control stand. A total of six of these control stands with a total of 25 operator stations were set up by the JST specialists.
Photo 2 | JST Ergonomics: The lower edge of the monitor wall is only 70 centimeters. Background: The objective during planning and conception was to achieve an optimized line of sight from the workplace monitors to the large screen system.
Photo 3 | JST Control Room Planning: Efficient and safe plant control is the focus of the realization of one of the most modern control rooms worldwide. On an area of about 1,000 square meters, the state-of-the-art control room of the Schwedt company PCK was realized with the support of the JST control room specialists. Special eye-catcher of the project: the Virtual Sky, which simulates a natural lighting situation. With the help of an upstream graphics processor, a bright summer sky can be generated from a gloomy November day.
Photo 4 | JST 3D planning: JST's holistic solution for the PCK project includes floor plan design, furniture, large screen systems, multi-console hardware and software, and a backup concept for maximum availability.
Photo 5 | Large construction site: pictures from the time of the extensive construction measures during the installation...
Photo 6 | ...remarkable: The complete commissioning of the entire control room was realized by JST within four weeks.
Photo 7 | JST Furniture: On customer request, the control room furniture was designed in the corporate design of PCK Raffinerie GmbH.
Photo 8 | JST workplace ergonomics: We also thought about the comfort for the PCK employees. To relieve the strain on the back, the operator can use the infinitely variable electromotive height adjustment of the control room consoles. The installation area of the operator desks was also equipped with underfloor heating.
Photo 9 | JST control center desk: In the rear area of the Stratos Command Desks, in addition to the TFT articulated arms for the screens, loudspeakers, USB sockets and controls for the room lighting are integrated.
Photo 10 | JST Technology: Revision-friendly technology installation - all MultiConsoling hardware is located in the supply room of the Stratos CommandDesk
Photo 11 | JST control room: Welcome to the spaceship - beam me up! The heart of the control room is a (currently still free) communication area, which will later be equipped with JST special technology and a digital interaction table.
Photo 12 | Animated LED daylight ceiling: The new PCK measuring station is located in an explosion-proof bunker building - without windows. However, a trick is used to create the impression of natural daylight: outdoor cameras film the current weather situation and project the data in real time onto the LED daylight ceiling.
Photo 13 | JST Control room: All control rooms are separated from each other by specially curved and anti-reflective glass panels. This enables visual communication without being impaired by disturbing noises.
Photo 14 | JST Control room: Entering the control room creates a real spaceship atmosphere. The actual dimensions of the project are best visualized in a 360° photo visual, which can be found here.
Photo 15 | JST Control room: No optical illusion - the anti-reflective glass panels were intentionally planned at an angle to avoid sound reflections in the individual control rooms.
Photo 16 | JST Operator's stand: A break and meeting area for the employees is also part of the equipment of the operator's stands. In the photo to the left: On a sideboard the legally required emergency stop switches were placed, which are no longer assigned to the individual workstations.
Photo 17 | JST Technology: A special installation to keep the danger under control, especially in dangerous situations: With the emergency stop panel, individual parts of the system can be switched off with a single push of a button in the event of a fault.
Photo 18 | JST Furniture: A look behind a control stand is also worthwhile: All wall surfaces were covered with an acoustically effective material and ...
Photo 19 | …Functional areas such as wall cabinets were integrated unobtrusively. Advantage: a completely quiet atmosphere in the entire control room.
Photo 20 | JST Furniture: The special furniture of the PCK control room has an additional function: Ventilation and air-conditioning installations have been integrated into the base areas of the individual pieces of furniture.
Photo 21 | JST Furniture: Again, barely perceptible to the eyes and ears of the observer: air conditioning and ventilation "hide" in the skirting boards of the sideboards. Right picture - the window to the outside: The display shows (like a window) the outside view to the outside. Traditional windows are not available in the bunker building.
Photo 22 | Until April 2016, all production facilities were monitored and controlled via a central control room from 1993, which had become too confusing over time. A proactive operation of the systems was only possible with a large number of personnel.
Photo 23 | JST Control Room: In the new control room, JST MultiConsoling has not only reduced the number of monitors but also the number of mouse-keyboard units at the workstation.
Photo 24 | JST Planning: Rear view of the workstations. The special ceiling structure is also clearly visible. According to the principle "form follows function" all elementary functions are integrated: lighting and acoustic concept, emergency lighting, air conditioning, loudspeakers and, of course, the optics.
Photo 25 | JST Large screen wall: Detail of the proactive monitor wall: The system is not used for display but as an active desktop extension for the process control system. A crucial advantage is the proactive alarm system, which automatically warns the plant operator in the event of a fault. Video monitors are integrated in the upper area, which transmit live images of the refinery plant.
Photo 26 | JST Large screen wall: Concealed air-conditioning function, acoustic materials and the AlarmLight, which switches from green to red in case of malfunctions - the JST DisplayWalls offer the highest quality "made in Germany".
Photo 27 | JST monitor wall: Clever solution! In the lower area of the large screen, the ventilation and air conditioning of the entire control room is housed inconspicuously and completely noise-free - neither air nor flow noises are perceptible.
Photo 28 | JST control room: A special training and education room was also set up. Software upgrades, for example, are installed and tested here before they are used in refinery operations.
Photo 29 | JST control room: The PCK training room attached to the control room has another special function: Here - similar to a flight simulator - all system malfunctions can be simulated.
Photo 30 | JST Technology: The technical installations were implemented in an identical manner in all control stands. The only differences are in the different process plants that are operated.
Photo 31 | JST MultiConsoling: Each control station is controlled with the myGUI user interface from JST. This allows comfortable operation, usually with a single click, and absolutely safe and confident operation in stressful situations.
Photo 32 | JST ControlRoom-Automation: The most important systems can be switched on at the touch of a button via the JST CommandPad®.
Photo 33 | JST MultiConsoling: The MultiConsoling concept creates clarity. Today, only three monitors (previously: seven monitors) and a mouse/keyboard unit (previously: four units) are required per workstation.
Photo 34 | JST Furniture: The PCK project also followed the JST motto "Think of everything!” In addition to setting up the actual control room, the control room professionals also supplied the surrounding and communal room furniture.
Photo 35 | JST MultiConsoling: The entire technical concept of the PCK control room is based on the MultiConsoling System from JST. This was implemented in multiple redundant design and guarantees a system availability of almost 100 percent with maximum operating comfort for the system operators.
Photo 36 | JST redundant MultiConsoling system: The switching from the master to the slave system is fully automatic. With the optional string changeover, manual changeover to the redundancy system can be forced during operation. This also allows a manual swivel from the productive MultiConsoling system to the backup system at any time.
Photo 37 | JST MultiConsoling: The JST MultiConsoling architecture comprises several 19-inch technology cabinets and is accessible from the front and rear for easy maintenance.
Europe's most modern refinery control room successfully goes into operation
Each year, PCK Raffinerie GmbH processes about 12 million tons of crude oil into petroleum and petrochemical products. All production facilities were monitored and controlled via a central control room from 1993, which had become too small and confusing over time. The responsible persons therefore decided to replace it with a state-of-the-art control room of about 1,000 m². With the interior design and technical equipment Jungmann Systemtechnik GmbH & Co. KG (JST) was awarded the contract for the interior design and technical equipment. The control room experts installed six control stations with a total of 25 operator stations and 78 monitors, as well as large screens with 100 displays, which are used proactively to control the systems. A special MultiConsoling concept reduces monitors and reaction times, creates an overview and enables particularly efficient work.
“PCK has been trying to centralize the control rooms since the 1990s. At that time we combined eleven satellite control rooms in the ‘old’ central control room. Now we are taking the next step forward by replacing this control room with a new, more modern one,” explains Thomas Taube, maintenance service engineer and project coordinator at PCK. In the new 1,000 m² main control room, the heart of the refinery, the entire process chain is monitored and controlled – from the receipt of crude oil by pipeline from Russia, through the steps in the production plants, to the finished product to be delivered, be it diesel, petrol or kerosene for aircraft.
Enables efficient and pleasant working
The control room consists of six control stands; acoustically separated from each other by anti-reflective glass walls. After completion, 125 plant operators – including reserve personnel – will be working there. Thomas Taube about the concept: “The system operation should be controlled via the large screen in combination with smaller monitors.” The company also intended to reduce the number of operating devices per workstation. Work in the control room should not only be made very efficient, but also as pleasant as possible for the employees. In addition, the entire system had to have extremely high availability and the probability of failure had to be reduced to an absolute minimum.
Test control center led to holistic JST solution
Detailed research and market analysis led to JST. “PCK contacted Jungmann Systemtechnik for the first time in 2014 during the ko:mon – Congress for Control Room Technology and Monitoring Systems. After a subsequent visit to JST’s control room simulator, the refinery first extensively tested a test workstation created by us consisting of a control room console, large screen segment and associated MultiConsoling hardware and software. After the successful acceptance of the test workstation, PCK then decided on an integrated solution from JST,” explains Carsten Jungmann, Managing Director of JST. These include among others layout concept, control room furniture, large screen systems and MultiConsoling Hardware and software.
Increased availability with increased flexibility
An essential prerequisite for the new building: “We wanted to increase the availability of the process technology and achieve high flexibility in the use of the control system,” says Taube. “The aim was also to be able to access every place in the facilities from as many places as possible.” Besides the process control technology, this is mainly due to hardware and software developed by JST for the control of workstations and large screen systems: „MultiConsoling correlates monitors, which means that the system operator always gets the display on one of his own screens that he needs at the moment,” explains Carsten Jungmann. “In this way, up to 1,000 different process images can be displayed on a single workstation with a reduced number of monitors”. The operation is done with only one keyboard-mouse unit at a time.
Potential sources of error have been eliminated
“We used to have four keyboards per workstation and always slid back and forth between them,” says Taube. This was inefficient and inconvenient on the one hand, and on the other hand the control room operator did not immediately have an overview of which monitor the respective device belonged to – a potential source of error that is now eliminated. MouseHopping, another operating function of the MultiConsoling, also plays a part in this: “It enables the operator to move the cursor with the mouse, for example, over all the screens at his workstation and up on the monitor wall,” explains JST Managing Director Jungmann.
Large screen walls integrated into new operating concept
The new large screens also support this concept “from fault-oriented to knowledge-based operation,” explains ThomasTaube. When an alarm is received, the control room operator is supported by special proactive lighting of the control room workstations and large screen walls, which complements the acoustic warning: This is the AlarmLight from JST, which can be controlled by the monitoring system and can flash or change color when an error message is received.
Reliable system control even in critical cases
The complete solution at the Schwedt refinery is designed to ensure safe plant control even in critical cases: “At PCK, our MultiConsoling system is used in a highly available expansion stage, i.e. with full redundancy,” explains Jungmann. “The MultiConsoling systems are designed for each operator’s platform in a way that if one system module fails, a second cluster takes over its functions within a few seconds”. But the safety concept has even more to offer. Thomas Taube: ” We also designed the higher level, meaning the complete system, with a complete redundancy system. According to our calculations, the control center thus offers maximum safety for our systems.
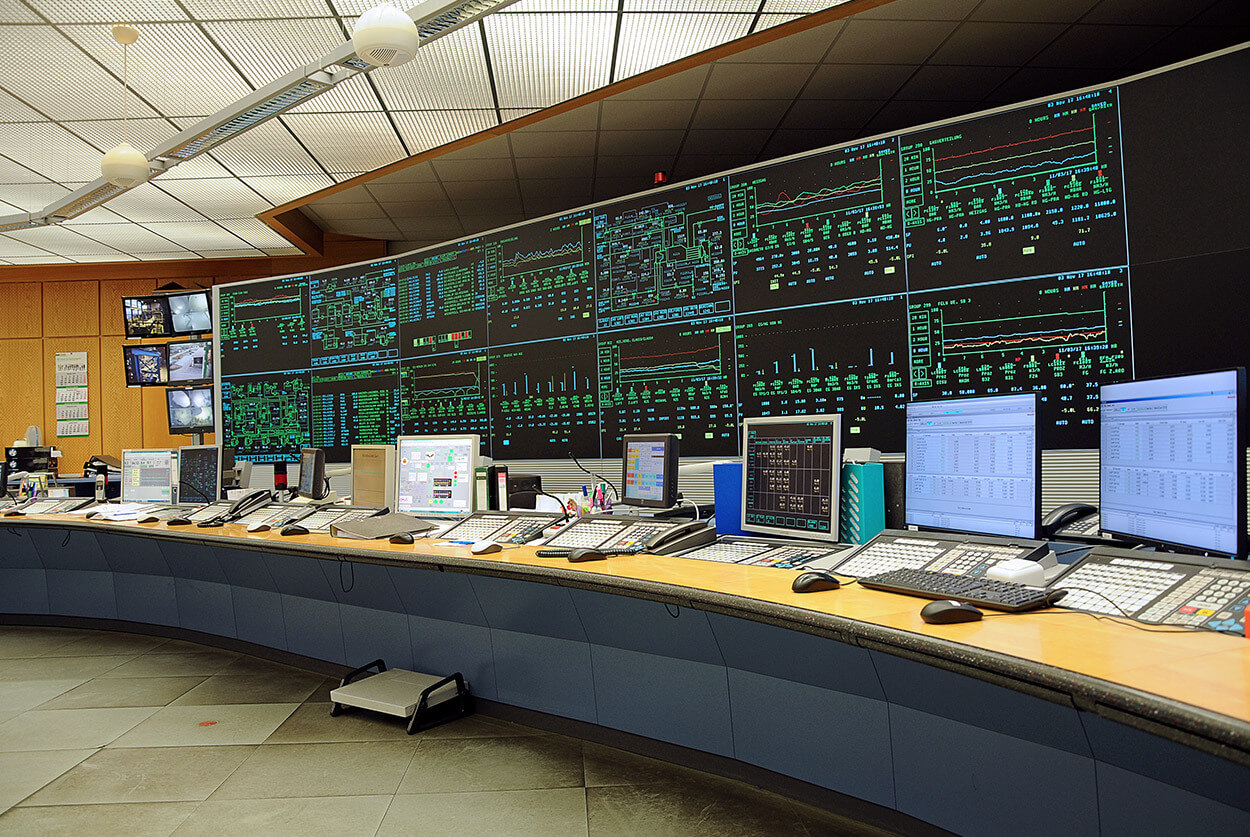
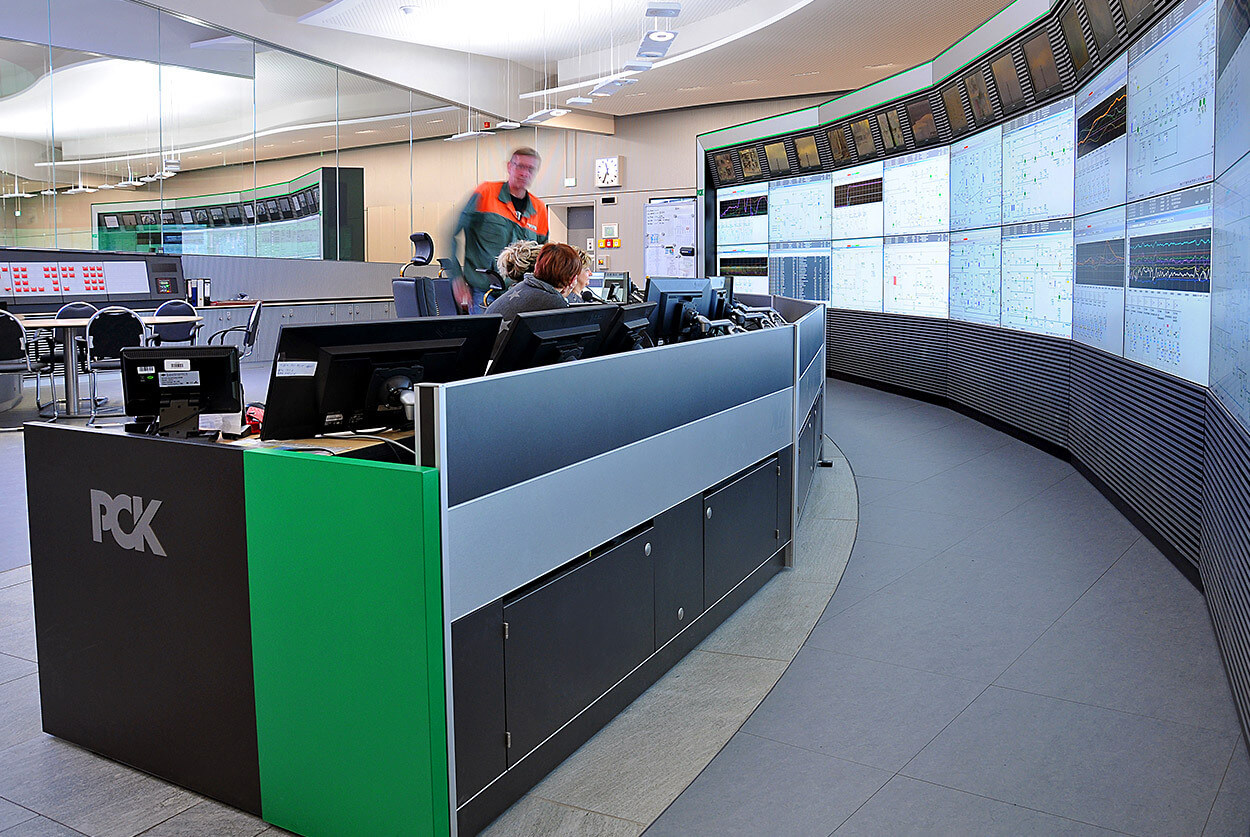
PCK control room before and after modernization.
Improvement in all respects
Both those responsible for the project at PCK and the plant operators rate the new control room very positively: “Compared to the satellite control rooms and also to the old central control room, we have achieved improvements in all aspects, be it acoustics, lighting, air conditioning, ergonomics or user-friendliness,” says Taube. “We are very pleased with the performance of our project partners.”
Interactive touch screen technology becomes a unique center for communication and data exchange
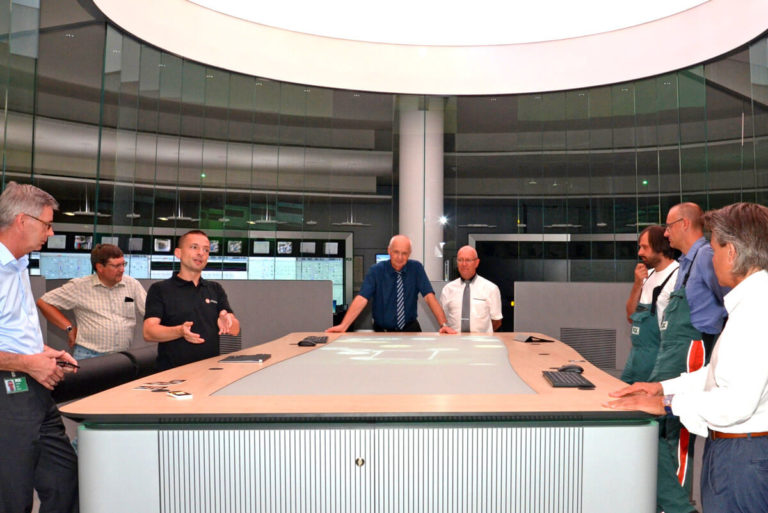
The motto “The future is now” applies! The state-of-the-art equipment of the PCK refinery control room is crowned with an extraordinary technical innovation: the interaction table. Christian Beck (technical director of JST, 3rd from left) gives an insight into the unbelievable variety of possibilities that could be realized with this unprecedented project. During months of development work, the Jungmann specialists created a multifunctional medium that enables interactive data exchange on an impressive touchscreen projection screen.
PCK refinery
PCK Raffinerie GmbH in Schwedt/Oder is one of the leading companies in the German state of Brandenburg. It processes around twelve million metric tons of crude oil annually into petroleum and petrochemical products, making it one of the largest crude oil processing sites in Germany. Its main products are diesel, gasoline, kerosene, liquefied petroleum gas, heating oils and bitumen. PCK was one of the first refineries in Germany to use biofuels and is itself a major producer of high-quality biofuel components. To PCK belongs the entire plant site including facilities and buildings, a crude oil tank farm and a pier in the Rostock oil port, the 78 km Schwedt – Seefeld pipeline, the 203 km Rostock – Schwedt pipeline and a hazardous waste disposal plant.
You are currently viewing a placeholder content from YouTube. To access the actual content, click the button below. Please note that doing so will share data with third-party providers.
More InformationYou are currently viewing a placeholder content from YouTube. To access the actual content, click the button below. Please note that doing so will share data with third-party providers.
More InformationPress review
Unsere Referenzen heute (Auswahl)
A
B
C
E
H
I
M
N
P
R
S
- s.Oliver, Rottendorf
- SachsenEnergie, Dresden
- SAG, Berlin
- SAG, Nürnberg / Nürnberg Messe
- Salzgitter Flachstahl
- Senvion SE, Osterrönfeld
- SGL Carbon Group, Bonn
- SIEMENS
- SIEMENS, Wegberg
- Spenner, Erwitte
- Städtische Werke Magdeburg
- Stadtwerke Gießen
- Stadtwerke Ratingen
- Stadtwerke Schwerin, Kraftwerk Süd
- Stadtwerke Steinburg GmbH, Itzehoe
- Stadtwerke Wolfenbüttel
- Starlim Sterner, Marchtrenk
- STORAG ETZEL, Friedeburg
- Straßenverkehrsamt Frankfurt am Main
V
Unsere Referenzen (Archive)