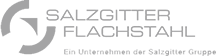
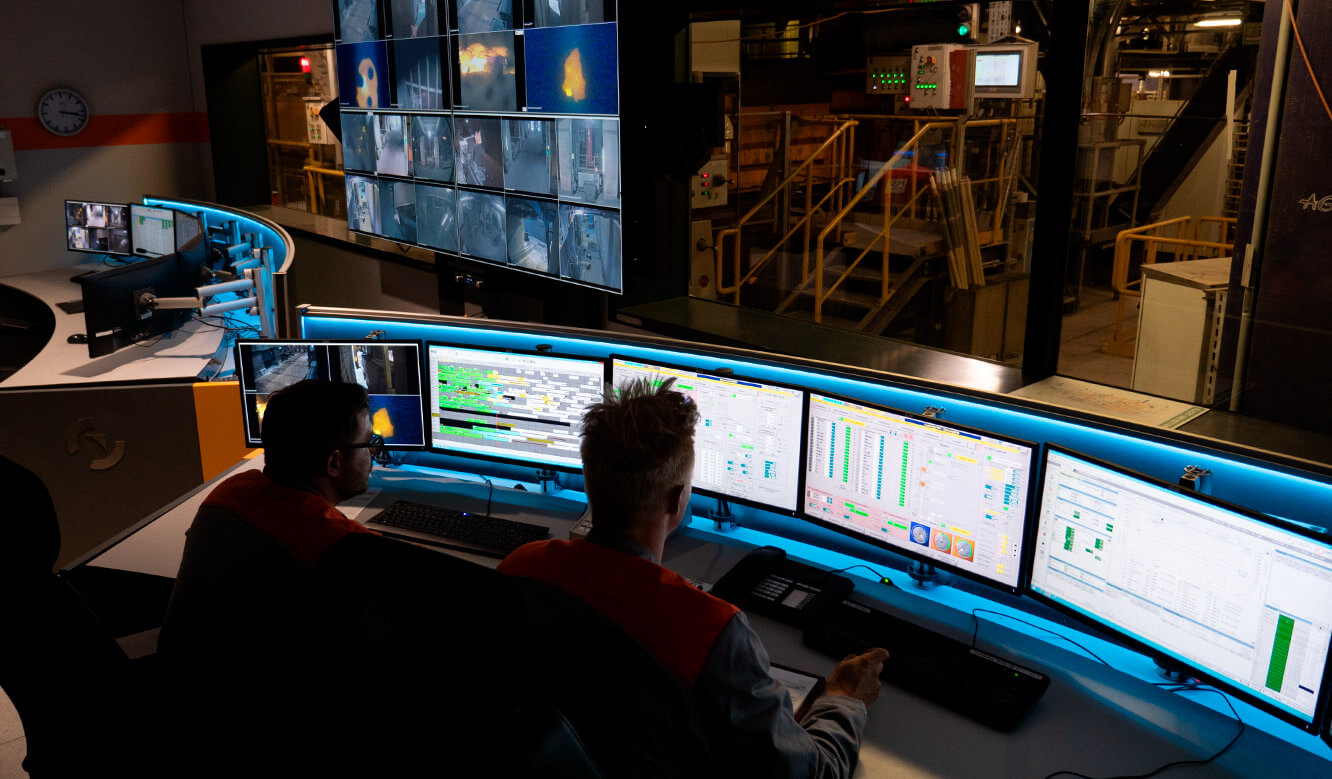
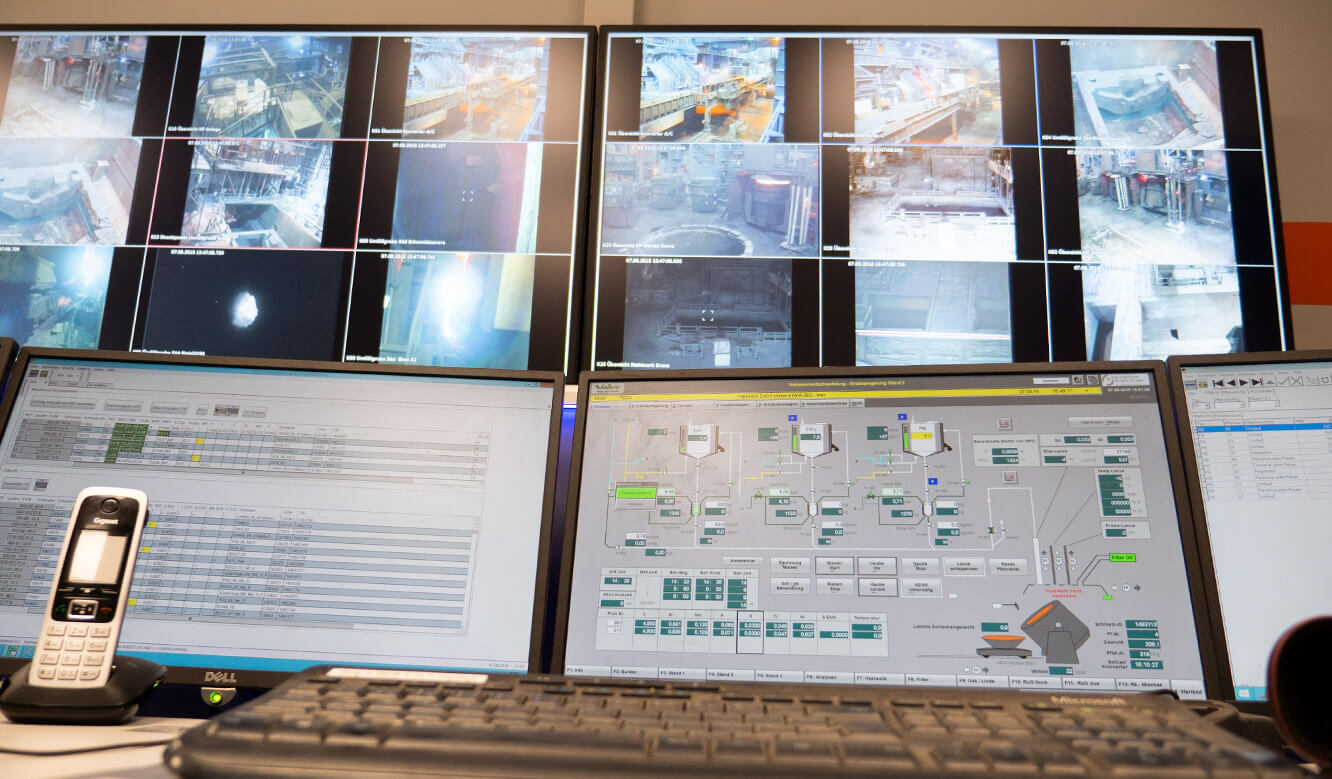

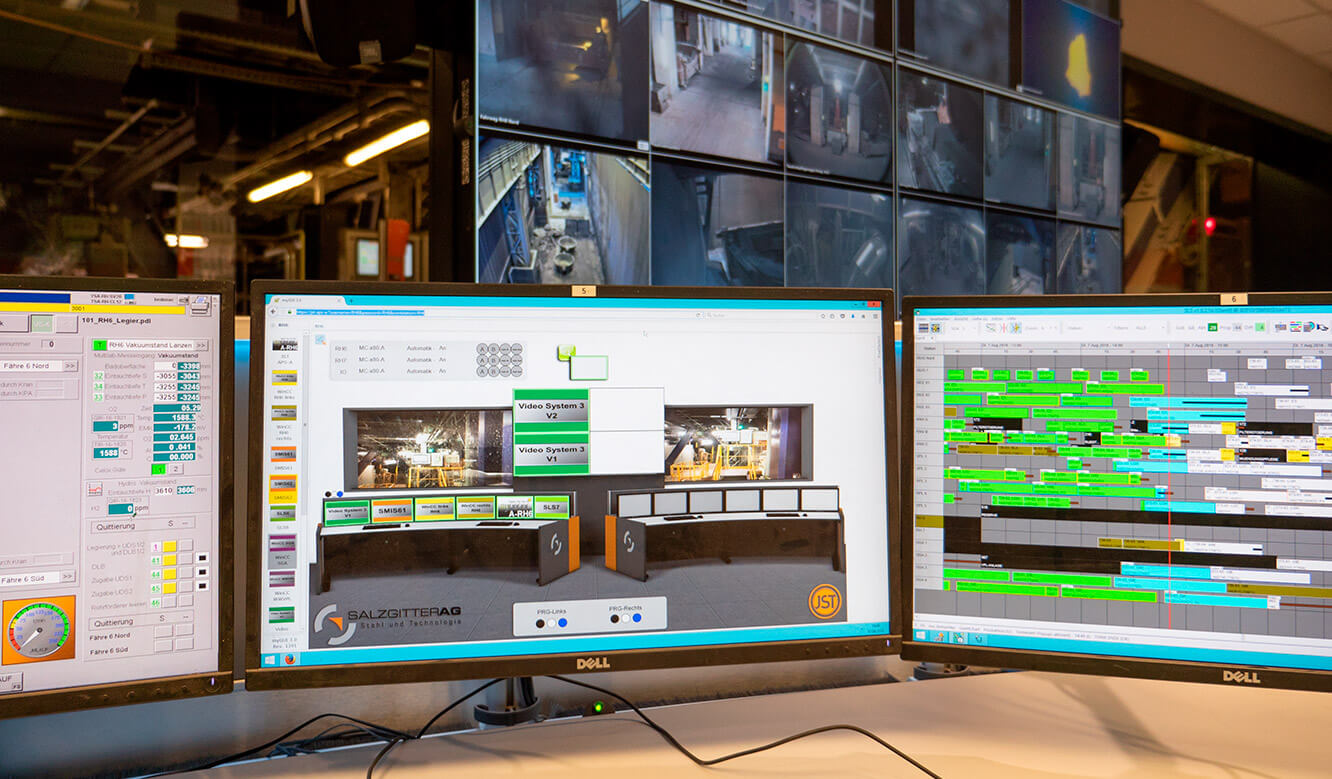
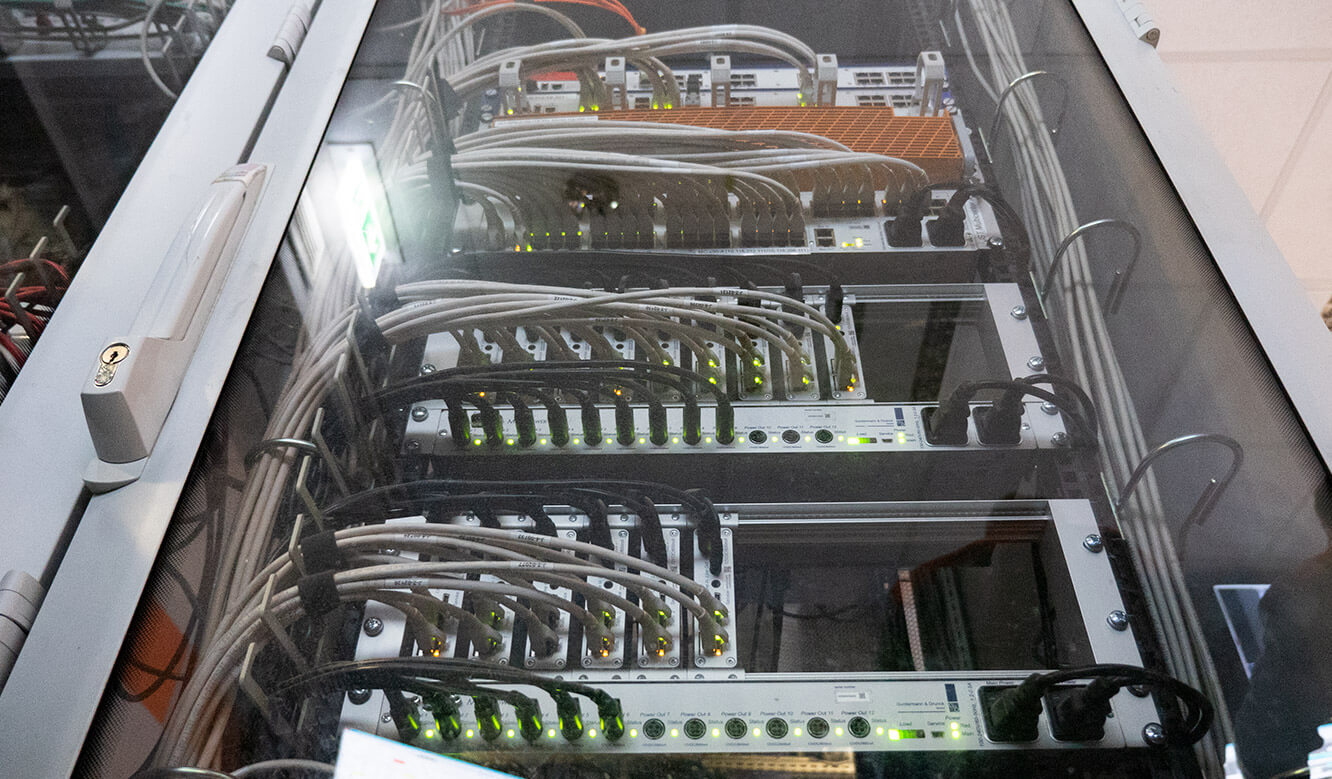
Photo 1 | JST control room: Increasing the quality and capacity of high-grade grades are declared goals of Salzgitter Flachstahl GmbH. With the installation of the new process control rooms, the best technical and ergonomically conditions were established in the area of plant control and monitoring.
Photo 2 | Impressive pictures from steel production: In the converter the pig iron is converted into crude steel. In this process stage, the carbon is separated from the pig iron. By adding oxygen, CO gas is formed and the carbon can be split off from the melt.
Photo 3 | Already before this converter phase, the molten iron was treated in the hot metal desulphurization plant, which is monitored and controlled from the control room of the same name.
Photo 4 | Only after conversion in the converter is the pig iron designated as raw steel. This steel is then also "refined" in the new RH plant by the employees in the process control room, so that its quality ultimately meets the customer's requirements.
Photo 5 | JST Control room desks: With the Stratos OperatorDesks, here in the curved variant "Curve", the focus is on ergonomics in the control room. In addition to numerous standard-compliant plus points such as legroom and a lowered monitor placement surface, the consoles also offer, for example,...
Photo 6 | ... the possibility of electromotive height adjustment to relieve the back and prevent health problems.
Photo 7 | JST control room desk: The Stratos Control room console always cuts a "good figure". Generously laid out and illuminated supply rooms offer sufficient space for technology and large quantities of cables. The control room workstations give a tidy impression throughout.
Photo 8 | JST control room console: When selecting colors and surfaces of the Stratos OperatorDesks there are many options to choose from. However, all surfaces have one thing in common: they are extremely resistant and can withstand even high loads during 24/7 use in control rooms.
Photo 9 | JST control room furniture: Individualizations are also no problem for JST – Jungmann Systemtechnik®. Here for example the logos on the Stratos CommandDesk in the corporate design of Salzgitter Flachstahl GmbH
Photo 10 | JST Ergonomics: Parabolically arranged screens - realized by 3D monitor articulated arms - allow the operator an ergonomic viewing angle of the displays at the workplace.
Photo 11 | JST control room furniture: In the foreground are lockable Personality cabinet solutions. Individual furnishing variants, which fit into the control room, JST Furniture manufacturer meets customer requirements with special equipment.
Photo 12 | JST Furniture: Back wall of the Stratos OperatorDesks. The control room desks are equipped with the JST AlarmLight, whose colors can be freely and intuitively selected. This makes it possible to change the working atmosphere at the touch of a button.
Photo 13 | JST Control room equipment: Individual solutions are always part of JST's control room philosophy. Here, for example, special cutouts in the user interfaces of the OperatorDesks, which were used by the client to insert joysticks for system operation.
Photo 14 | JST PowerPort Data Box: The operator consoles were equipped with PowerPort-Data Boxes. In this way, users have all the desired supply connections conveniently available directly at their workplace.
Photo 15 | JST Large screen technology: Camera views, logistics models, illustrations for technical operation and data for metallurgical calculations - the areas of application for large screen displays in Salzgitter Flachstahl control rooms are manifold.
Photo 16 | JST Video wall: The displays on thelarge screen wall also show, for example, images of steel transport in ferries or by crane. Such images in particular are closely followed by control room staff, as they are highly relevant in terms of security.
Photo 17 | JST QuickOut mounting system: The large screen displays are mounted directly on the wall to save space. By applying light pressure to the outer edges of the display, each individual display slides forward (QuickOut) to ensure access to rear connections and technical components in case of inspection.
Photo 18 | JST Large screen technology: In the control room of the hot metal desulphurization plant at Salzgitter Flachstahl, the large screen displays are not used in combination, but as individual large displays for camera and monitoring recordings.
Photo 19 | JST ControlRoom Automation: Behind these buttons in the surface of the operator panels is a special solution from JST. Employees can individually arrange their desired configurations from data, functions and camera images, then save them and call them up again at the start of the shift at the push of a button. It is also possible to activate additional, predefined scenarios via the JST CommandPad®.
Photo 20 | JST Control room technology: With the MultiConsoling® concept, a keyboard and a mouse are all that is needed to operate all workstation displays and the large screen wall.
Photo 21 | JST MultiConsoling®: Both the process control systems and the camera systems are flexibly displayed with the JST MultiConsoling® an operating concept that allows all desired displays to be switched on quickly and intuitively on the large screen displays or on the monitors at the workplace. "We have to react at short notice, and this is no problem with MultiConsoling® ," says plant engineer Soeke Helmers.
Photo 22 | JST MultiConsoling®: Makes operation of the JST JST MultiConsoling® fast and safe - the myGUI®user interface (here on the middle screen) displays a 3D image of the control room.
Photo 23 | JST Technology: Clean and protected from dust in special cabinets: The heart of the control room technology with MultiCenter (device on top) and the so-called "grabbers" to which the individual computers are connected.
Steel industry: New process control rooms are the "salt in the soup”
A handful of manganese, some silicon and a pinch of niobium. What sounds like a recipe at first glance comes from the “kitchen” of the steel industry. But making steel is not quite as simple as preparing a tasty meal. Salzgitter Flachstahl GmbH (SZFG) offers its customers around 450 different steel grades. This requires complex processes that take place in ultra-modern facilities. Two of these plants on the company premises in Salzgitter have now been equipped with new process control rooms – by JST – Jungmann Systemtechnik®.
“This plant meets the requirements for ultra-low desulfurized, ultra-low decarburized and hydrogen degassed steels as well as for steels with the highest degrees of purity,” explains steel mill manager Thomas Müller, describing the advantages of the new RH plant (Ruhrstahl-Heraeus), a vacuum treatment plant used in secondary metallurgy to increase the quality and capacity of high-grade grades.
Only as efficient as the person who operates them
But even the most modern instruments and equipment are only as efficient as the people who operate them. For this reason, SZFG decided to use a control station from Jungmann Systemtechnik to operate and control the new RH system. And not only that: At the same time, a new control room was also installed for the upstream process of hot metal desulphurization and the plant required for this.
High-tech plant with a high-tech control station
For plant engineer Soeke Helmers, the cooperation with the JST specialists is an important step: “A new high-tech plant includes a high-tech control station that offers an optimal combination of technology and design”.
Most exact monitoring and control required
But what actually happens in the new RH plant? And what are the tasks of the 24/7 manned control center? The Ruhrstahl-Heraeus process is a complex process in which the liquid steel is decarburized by means of vacuum treatment. At the same time, unwanted gases are extracted from the melt. Soeke Helmers comments: “There is a large number of process models here, which are precisely monitored and controlled to calculate the desired result. Naturally, we want the operator to have an optimal overview of everything.
Safe and intuitive with MultiConsoling®
Large screens walls provide an overview of the processes. Whether camera view, logistics model or data for metallurgical calculations – with the JST control concept MultiConsoling®, the employees at the control stations are able to safely and intuitively access any desired display on the displays of the large screen wall or the individual workstations via the myGUI® graphical user interface. “This allows the employees to evaluate the process perfectly,” judges Soeke Helmers, who emphasizes: “This is not just a monitoring activity. Rather, modern technology in combination with human expertise and years of experience are required. “Our employees know exactly how to handle the melt. Important decisions are made which have a major impact on the final product.”
New standards in work ergonomics
In order to provide the best basis for judgment and overview for these essential tests and diagnoses within the framework of a high degree of automation, the process control stations of Jungmann Systemtechnik were implemented. “We also wanted to set new standards here in terms of work ergonomics,” says the plant engineer, who mentions several aspects that are particularly appreciated by his colleagues from the control room team. These include the Stratos X11® CommandDesks, which, thanks to height adjustment, special supply rooms for cables and technology as well as indirect lighting, can be easily set up to meet the individual requirements of the individual.
"Desired configuration easily available”
It is precisely these customization options that the steel expert appreciates in another JST component that has found its way into the new process control rooms: With the ControlRoom-Automation solution, every employee can optimally compile views of all data, functions and camera images, then save them and call them up again at the start of the shift at the push of a button on the operator console. “So you can have the configuration you want quickly and easily available.”
Praise for process transparency thanks to JST concept
The conclusion of Soeke Helmers: “The control station concept of Jungmann Systemtechnik offers excellent process transparency and also advantages for work safety. Furthermore, the satisfaction of the employees speaks for itself, for whom this great working environment is very important.“
Our references today (selection)
A
B
C
E
H
I
M
N
P
R
S
- s.Oliver, Rottendorf
- SachsenEnergie, Dresden
- SAG, Berlin
- SAG, Nürnberg / Nürnberg Messe
- Salzgitter Flachstahl
- Senvion SE, Osterrönfeld
- SGL Carbon Group, Bonn
- SIEMENS
- SIEMENS, Wegberg
- Spenner, Erwitte
- Städtische Werke Magdeburg
- Stadtwerke Gießen
- Stadtwerke Ratingen
- Stadtwerke Schwerin, Kraftwerk Süd
- Stadtwerke Steinburg GmbH, Itzehoe
- Stadtwerke Wolfenbüttel
- Starlim Sterner, Marchtrenk
- STORAG ETZEL, Friedeburg
- Straßenverkehrsamt Frankfurt am Main
V
Unsere Referenzen (Archive)