Advanced control center for the automotive industry ensures smart, efficient processes
The control center for the automotive industry serves as a central hub. All information from production, logistics, quality management and IT converges there. Processes are monitored and coordinated in real time. With innovative control and surveillance tools from JST, efficient operations are ensured. Deviations are detected early in the control center and decisions are made quickly – before disruptions affect production reliability. Existing and new systems in the vehicle technology sector can be seamlessly integrated thanks to customised interfaces.
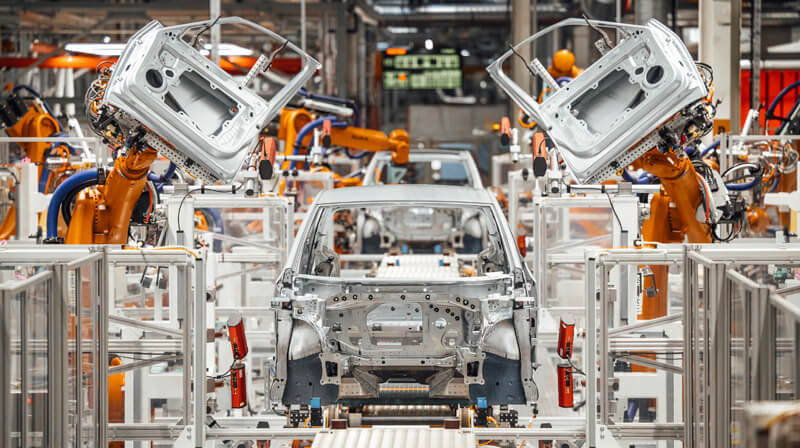
Central control system is becoming the main actor
Wear and tear, delayed delivery, interrupted production or even plant downtime – the control center in the automotive industry ensures that such scenarios are effectively prevented. Modern monitoring systems ensure that there are neither quality deviations nor capacity bottlenecks. But are all the conditions correct? Are all the requirements met within the control center? The experts at JST not only include hardware and software components for secure system integration in their planning. Visualisation, ergonomics and system availability also play a crucial role in vehicle manufacturing.
From parts delivery to body production and final assembly: a control center is the fundamental component in the automotive industry for controlling material flow and production processes efficiently and smoothly. In hundreds of control rooms, operators work with JST control room solutions that have been specially configured for the individual tasks on site.
Increased productivity, fewer failures, lower costs – key requirements that are met in the automotive control center. Intuitive system operation with KVM technology serves as the basis for this, simplifying the handling of all applications and their visualisation on the video wall. The operator team is able to react proactively and immediately to impending faults. The result: smooth processes, higher performance and increased competitiveness.
Technology and ergonomics were key factors in planning the FIS control center at Volkswagen in Wolfsburg. There, everything revolves around the vehicle information and control system. Operators monitor and manage the entire automotive manufacturing process. With the help of JST´s 3D visualisations, the project team was able to get an idea of the future control room in advance.
Production control in the automotive industry – hold all the aces
Real-time monitoring – through MES & SCADA system integration
Process automation – reducing manual intervention speeds up the processes
Secure handling – smart KVM technology simplifies operator tasks
Efficient coordination – thanks to direct access to all control center sources
Predictive maintenance – stay ahead with real-time data and analyses
Optimisation of logistical processes, manufacturing control and production monitoring in the automotive industry requires clearly defined performance specifications within the control center. Advanced KVM technologies are the basis for seamless task and process coordination. Increased productivity, higher quality and maximum operational reliability can only be achieved through optimal resource utilisation and early detection of failure points. Whether live status displays, predictive maintenance, AI-supported control of relevant production key figures or the integration of systems such as MES and SCADA – the KVM solutions JST MultiStreaming® and MultiConsoling® provide a future-proof foundation for smooth, centralised control in automobile manufacturing.
Image: © AUDI AG
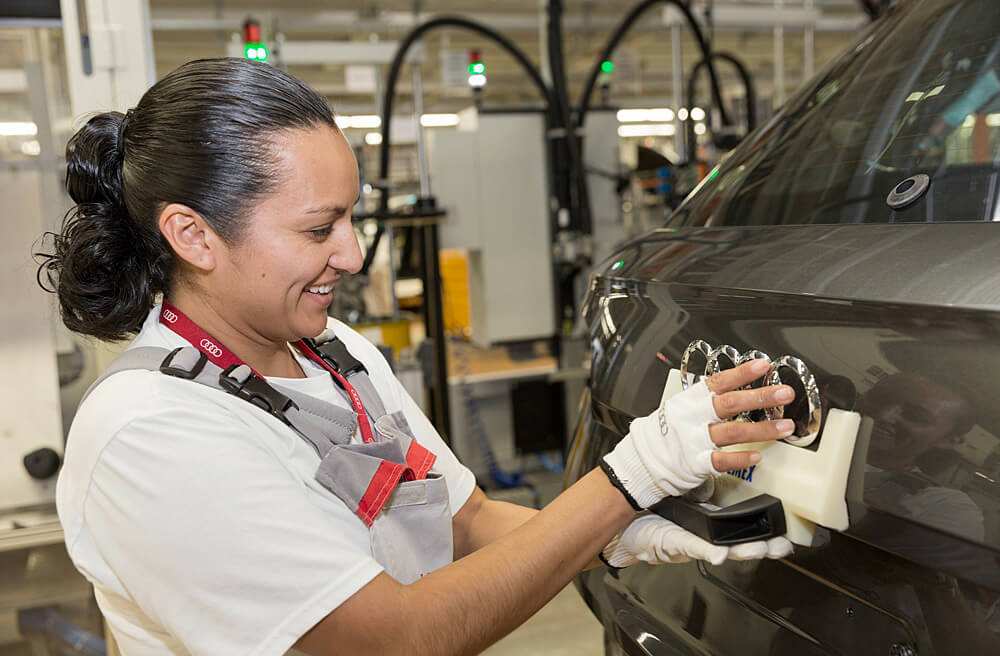
Line status, machine conditions, production progress, material flow – these are just a few of the data sources whose continuous analysis is indispensable in the automotive industry. Monitoring such critical parameters demands efficient decision-making processes and rapid responses. Prerequisite: A uniform user interface reduces the complexity of data evaluation through an easy-to-understand visualisation.
The JST developers have designed the user platform myGUI® specifically for this challenge. User feedback from hundreds of control centers has been incorporated into the interface, which is individually adapted to the workplace. The myGUI® combines all applications in a single view – system-independent, intuitive and convenient!
with the myGUI®
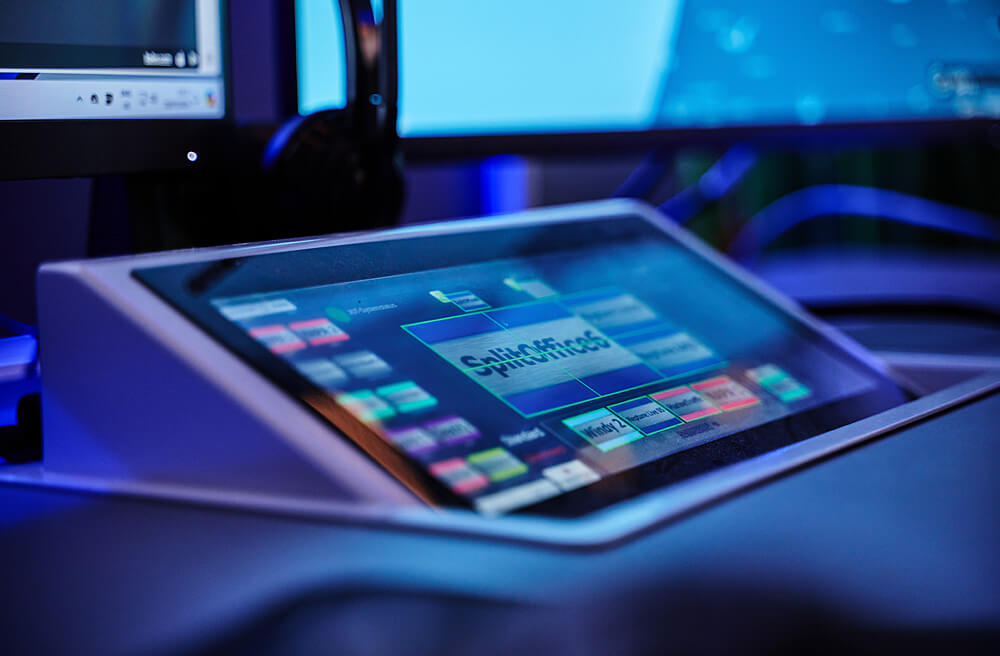
with the myGUI®
A clear overview of production data, process statuses and key figures can prove to be a real game changer for control centers in the automotive industry. Video wall technology offers all operators an identical level of information about current conditions within a location. Decision-making processes and coordination become more efficient and the risk of communication errors is reduced.
Both LCD monitor walls and large-format LED walls are suitable for real-time monitoring of production processes and live status displays of machines and robots. With innovative visualisation technologies of the JST control center experts, predictive, automated alarm messages can also be implemented in the digital control of manufacturing processes.
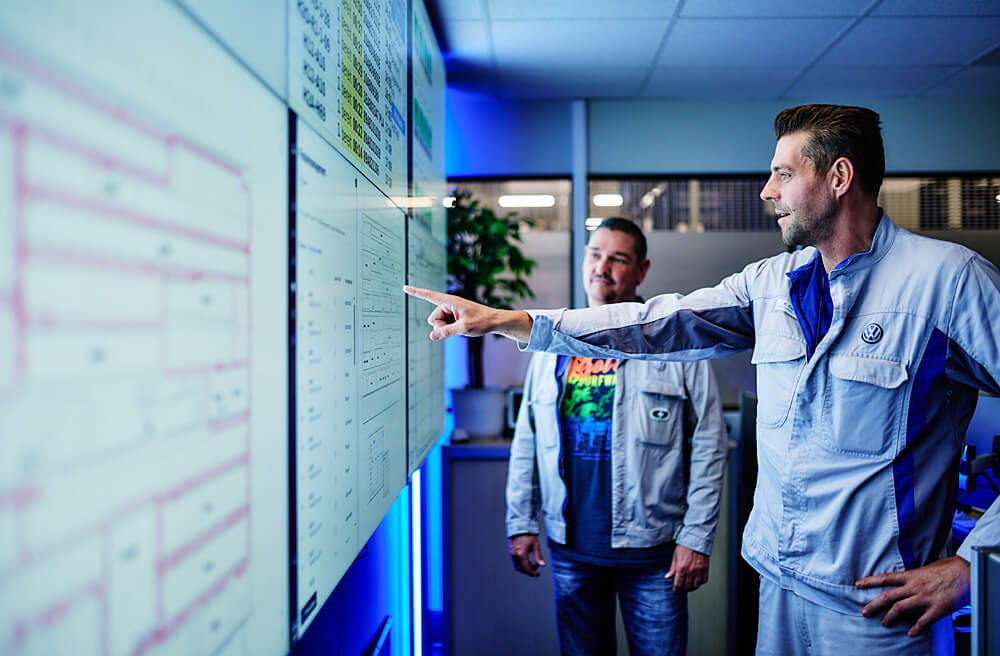
A look at our projects: When it comes to the big picture, JST technology makes the difference
Almost three decades of control room expertise – that’s what we stand for! With hundreds of outstanding projects. JST installations – these are control centers in all areas of the automotive industry. Control rooms that cover such diverse sectors as production processes and logistics, IT and energy supply. And all this in an sector that has to face the challenges of the global market like no other – from electric mobility, rising energy costs and growing competitive pressure to digitalisation, sustainability requirements and increased quality and efficiency standards.
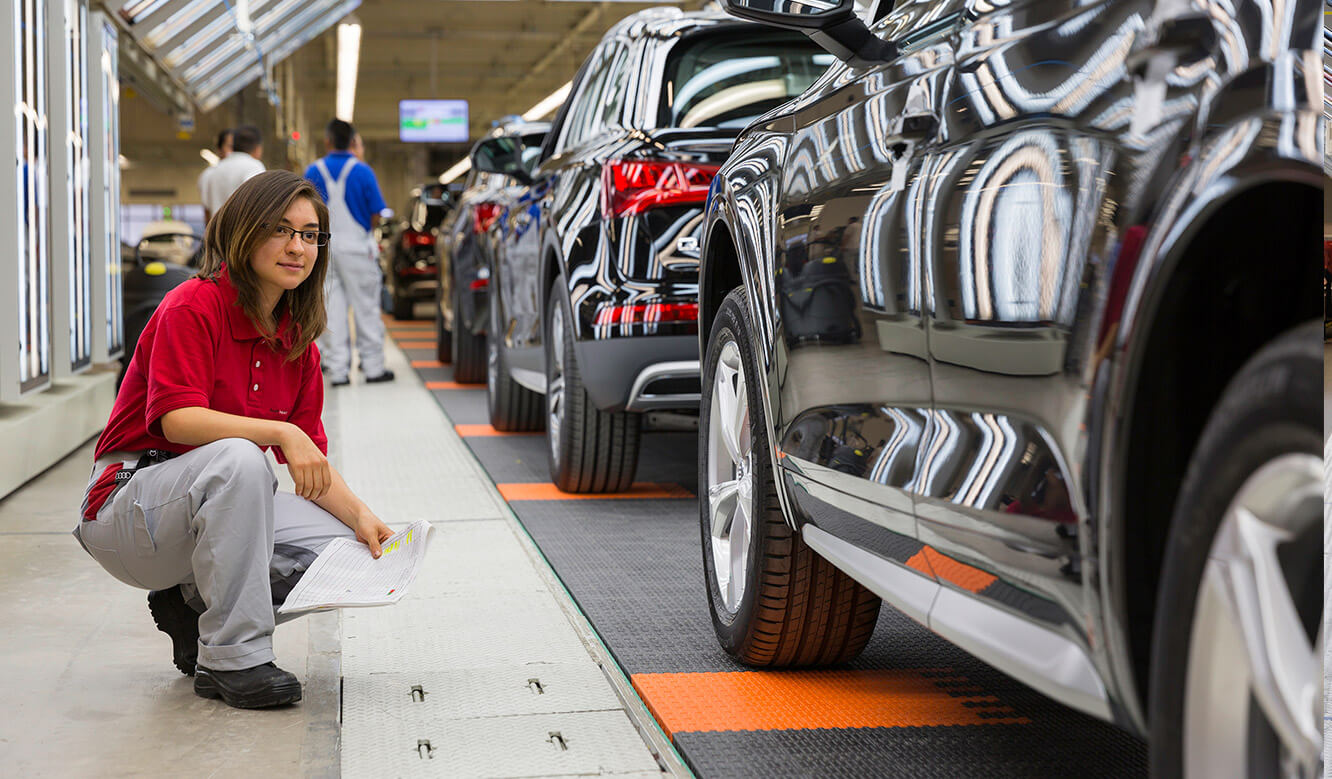
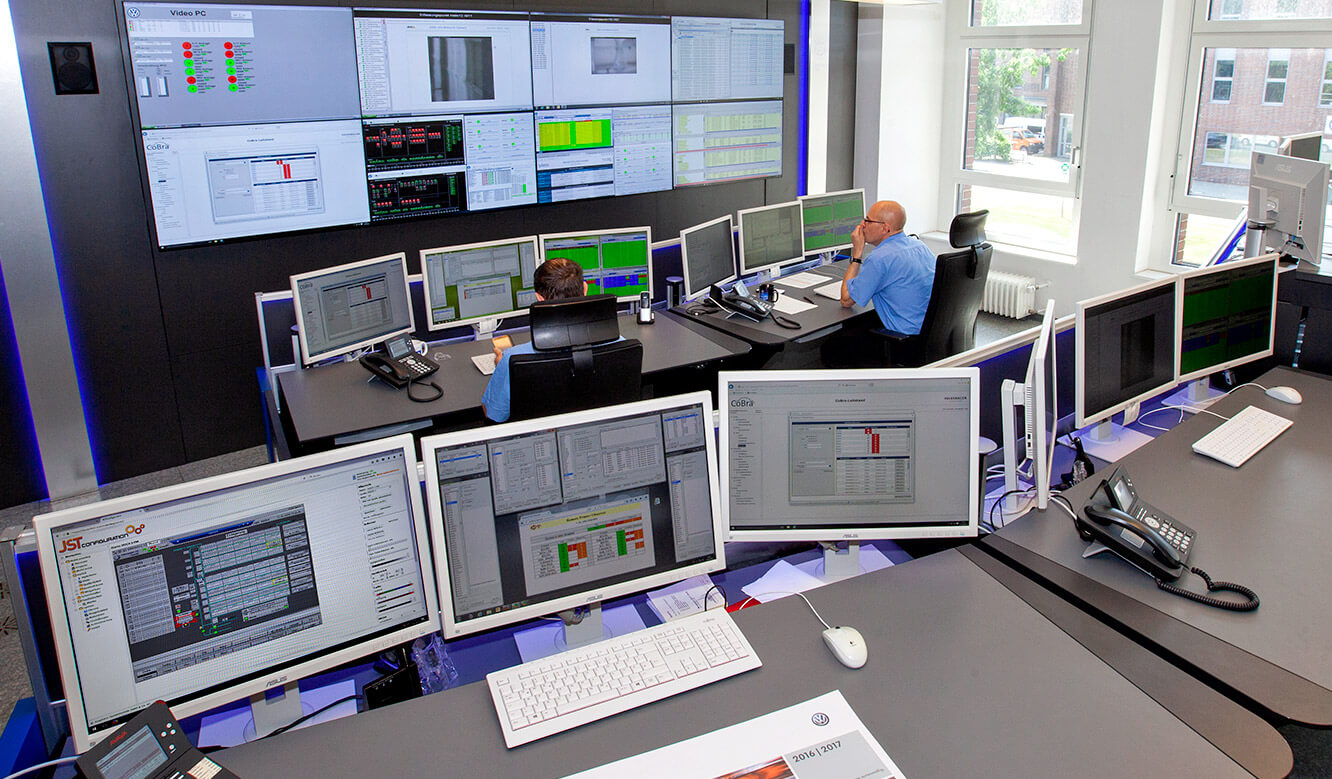
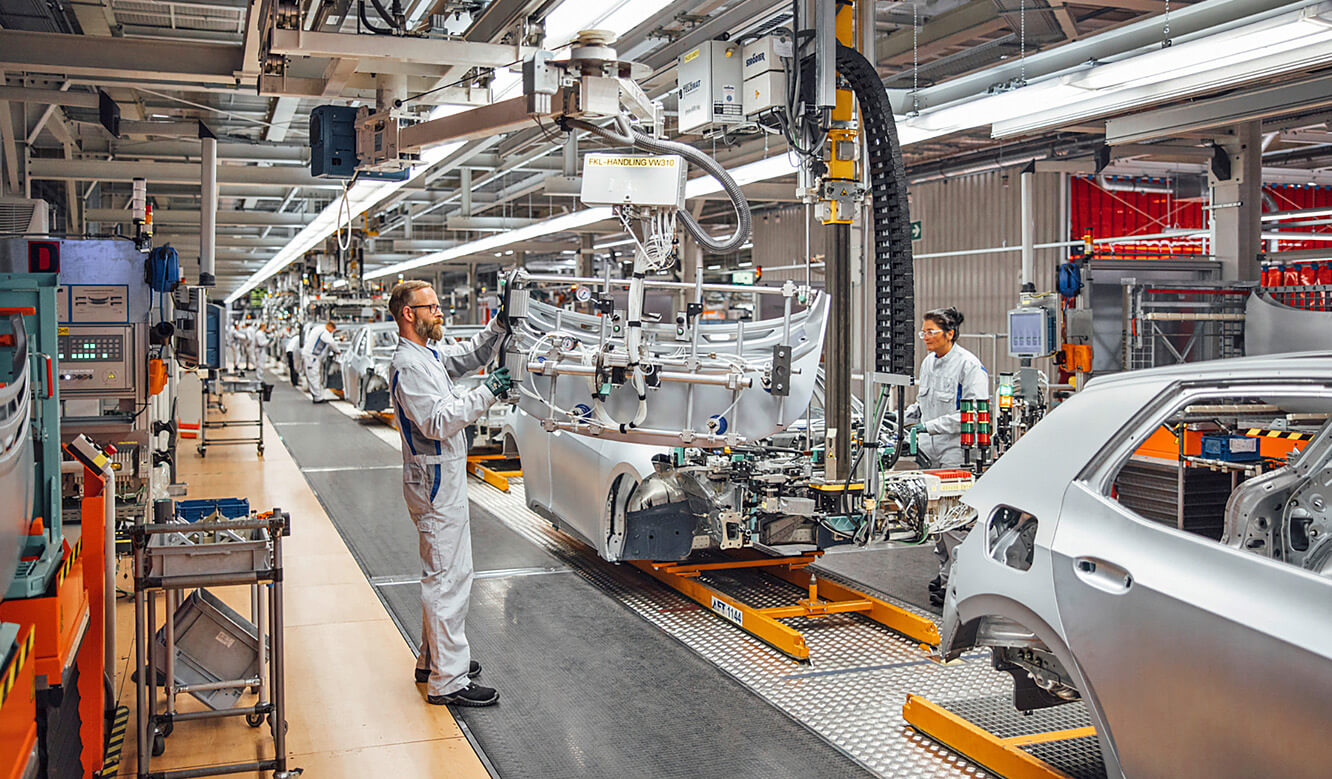
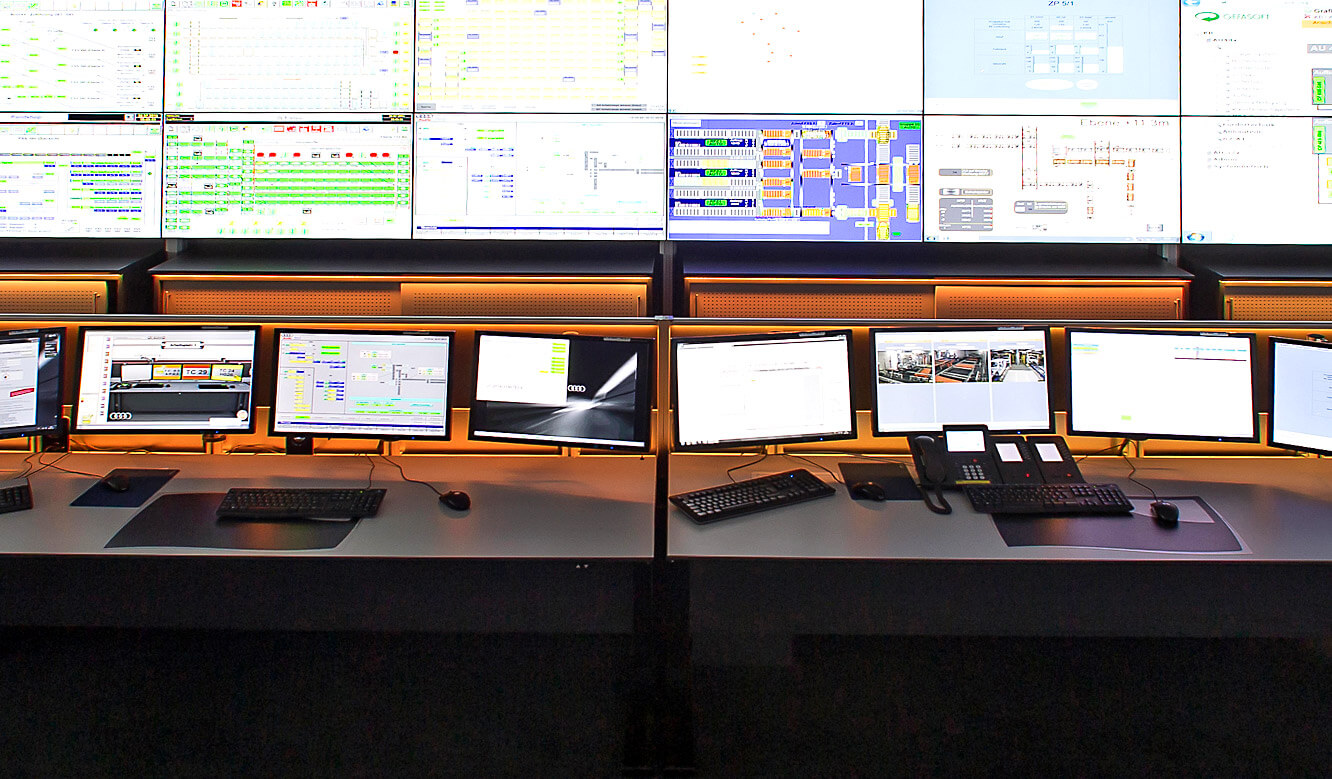
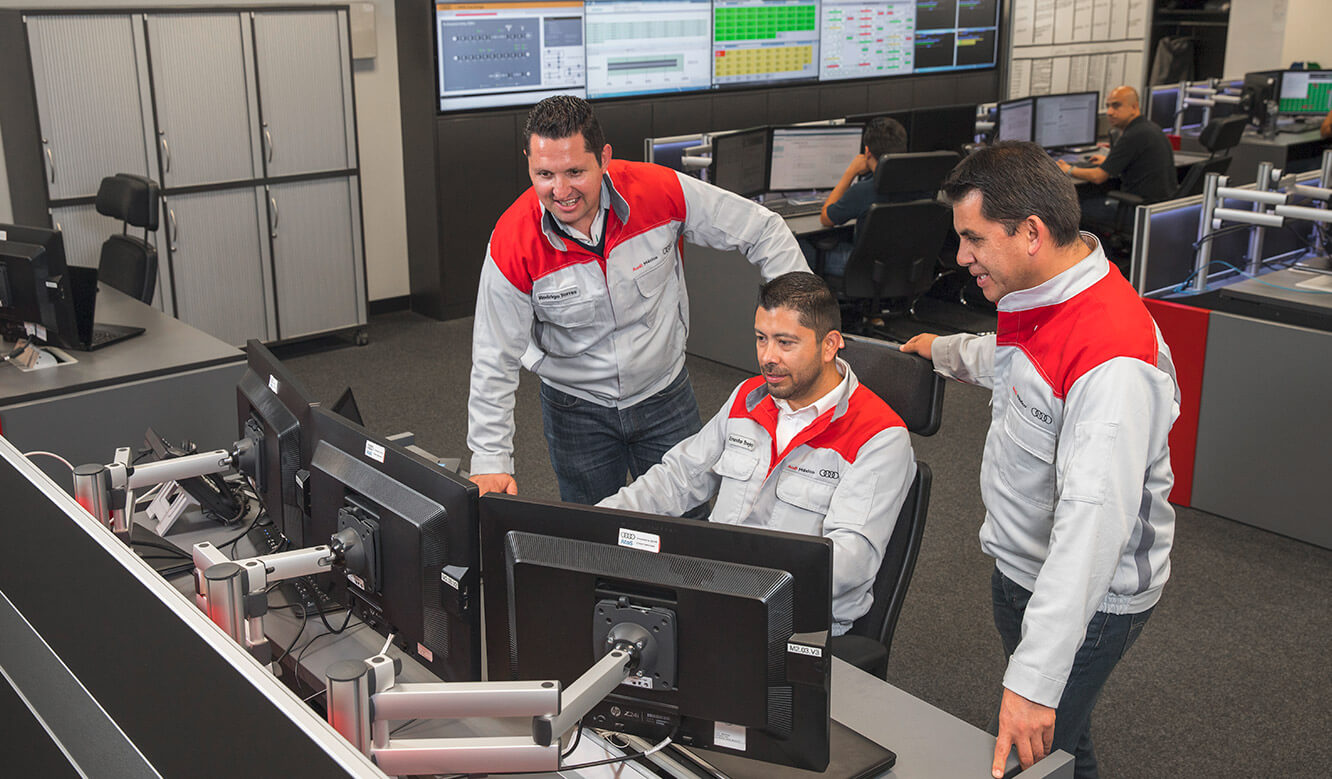
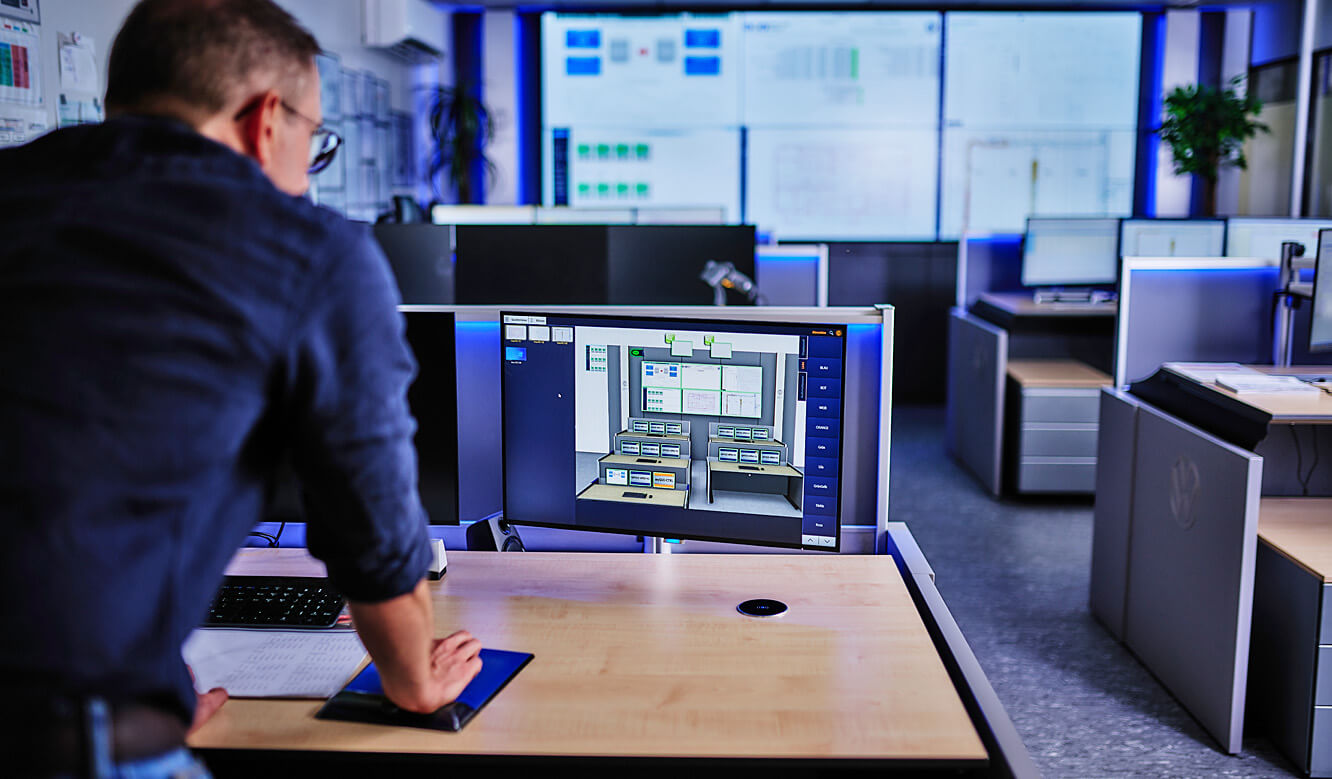
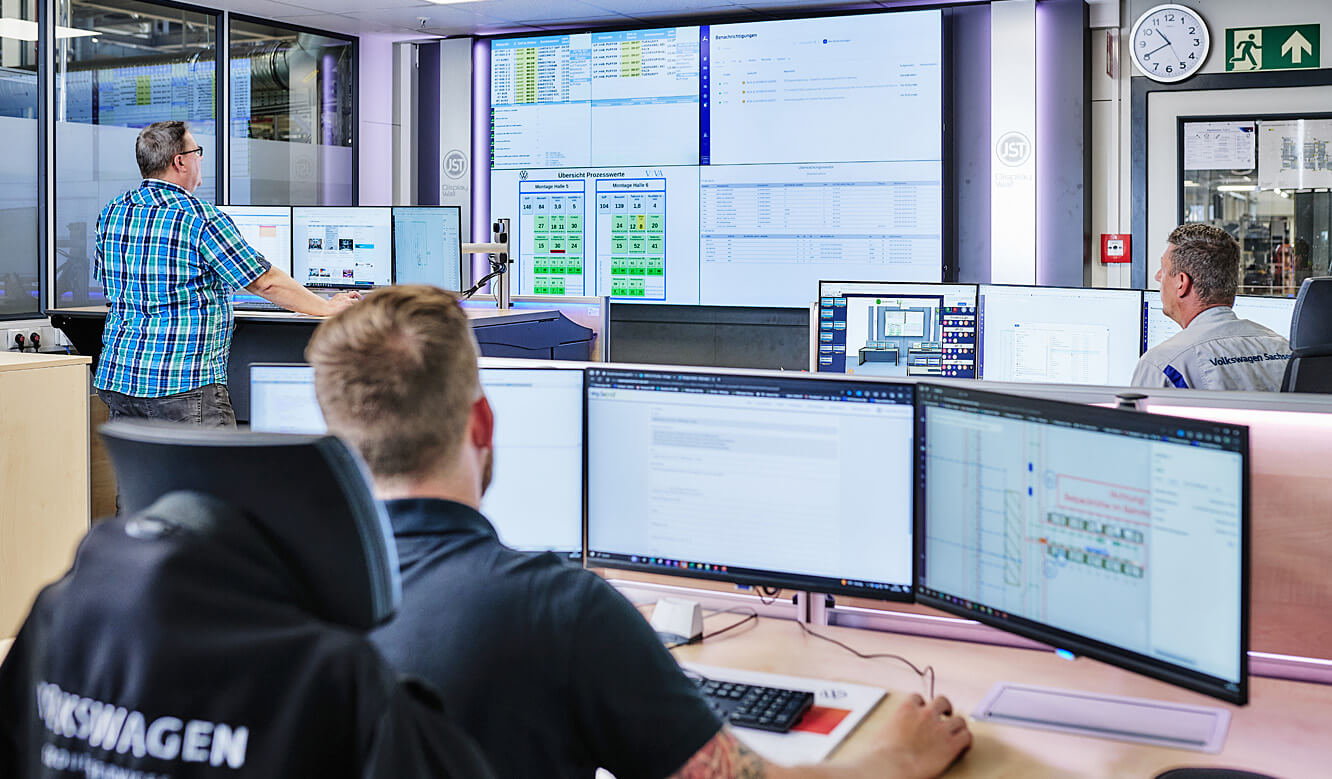
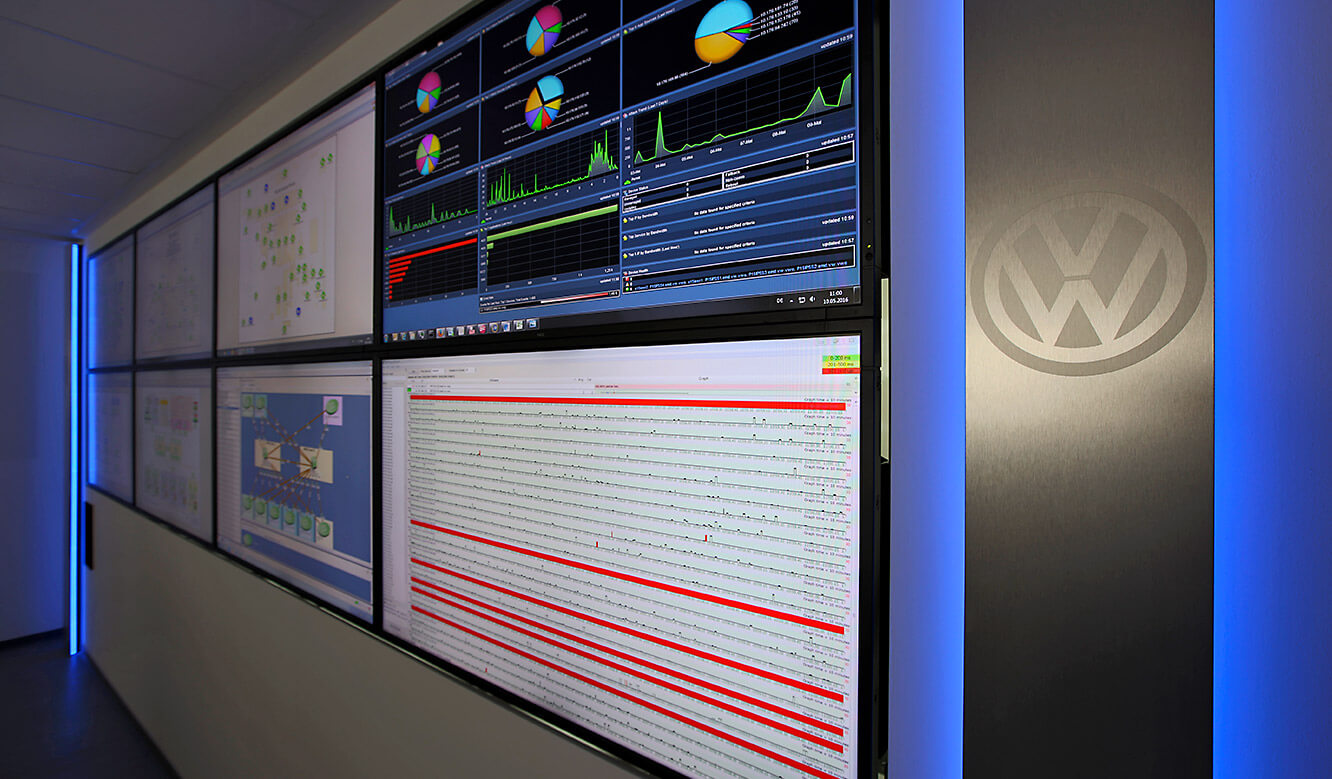
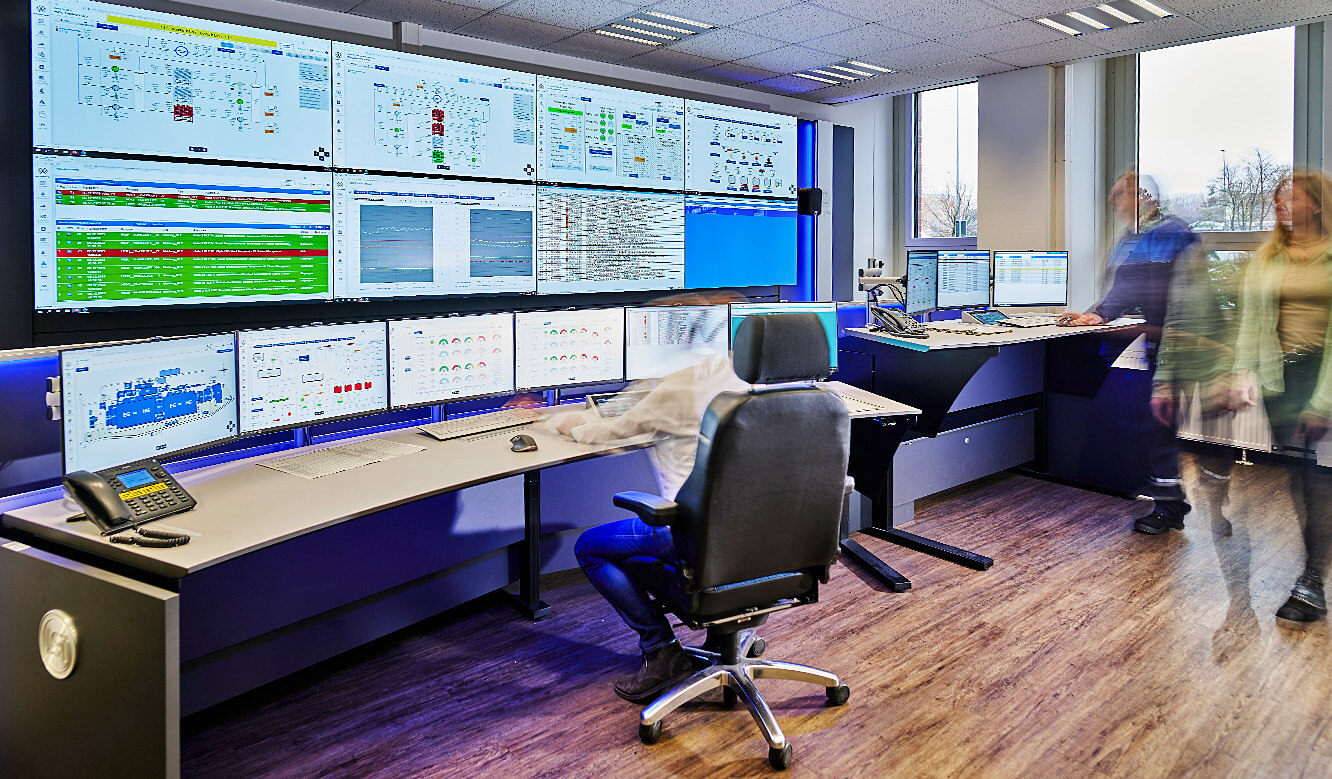
Image 1 | ©AUDI AG | Final inspection at the AUDI plant in Mexico: after the production control center has monitored the digital control of the entire vehicle manufactoring process, the brand-new SUVs roll off the assembly line.
Image 2 | At the Volkswagen plant in Wolfsburg, the FIS control center is known as ‘the brain of the factory’. The entire production process is monitored and controlled from here, from the receipt of orders for the plant to the arrival of the vehicles at the assembly line.
Image 3 | ©Volkswagen AG | One of the few production steps at Volkswagen Sachsen that still involves the physical labour of employees: the assembly of tailgates. The majority of the production lines are automated and controlled by means of modern control technology. The advantages of this are faster processes, more efficient use of resources and early detection of faults and bottlenecks.
Image 4 | Central vehicle control at AUDI in Ingolstadt: real-time monitoring in the manufacturing process and digital control on the production lines. On two large video walls, employees can follow the complete development of the vehicles – from the first sheet metal processing in the body shop to controlling in the individual paint lines and on to final assembly with the last quality check.
Image 5 | ©AUDI AG | To ensure compliance with the premium quality standards, Audi is networking the plant in Mexico globally with other locations in the Audi production network. For the first time, five control centers, which are often located separately at other Audi sites, are combined in the central control room in Mexico. By combining individual interfaces, the various control centers can communicate with each other efficiently and directly. This allows even the smallest deviations to be detected at an early stage, so that appropriate action can be taken in time.
Image 6 | Secure access to control of all processes: the myGUI® user interface provides employees in the control center of the body construction division at VW Zwickau with a clear 3D visualisation of the entire infrastructure and thus access to all sources in a matter of seconds.
Image 7 | Efficient processes are also a central topic in the assembly control center at Volkswagen Saxony. Project manager Michael Beier talks about the advantages of the new video wall technology: “The control center and its functionality help us to visualise the various sub-processes within the system. We don’t have to guess where the fault might be, the large display wall shows us directly.”
Image 8 | LCD technology in the Emden plant of Volkswagen AG: the large-screen video wall technology serves as a central visualisation element for all operators in the control center. Project manager Andreas Stange: “We now work directly from our workstations with the displays on the large screen wall, we can also easily see the details and develop solutions as a team.”
Image 9 | By merging two control rooms into a central control center, more structured workflows, more efficient energy management, and high availability could be established at the Volkswagen Commercial Vehicles site in Hanover. The MultiConsoling® KVM technology from JST created the conditions for the desired consolidation. In addition, employees benefit from ergonomic control room furniture and proactive video wall technology.
Global competition is putting pressure on the automotive industry: costs, quality, innovation and agility are of enormous importance in the international market. Remote monitoring ensures transparency in production as well as consistent quality and standards. Resources can be used more efficiently and quick decisions can be centralised. In addition, travel and maintenance costs are reduced for the automotive branch.
JST’s high-performance and scalable KVM systems provide the appropriate solution for real-time remote monitoring and control. Operators have live access from the overarching production control center to remote locations on all continents. User access is managed centrally, which also minimises the risk of cyber attacks.
Scalability and cost control are essential in the automotive sector. Transformation processes make it necessary to integrate monitoring and control systems such as MES (Manufacturing Execution System) or SCADA (Supervisory Control and Data Acquisition) into the plant management system and to supplement them with a growing number of smart applications. KVM technology from JST provides the basis for this modernisation. Both the network architecture of JST MultiStreaming® and the hardware configuration of MultiConsoling® adapt to the needs of the control center independently of operating systems. Both solutions have been designed by the JST development team to allow flexible extensions to be made effortlessly and cost-effectively.
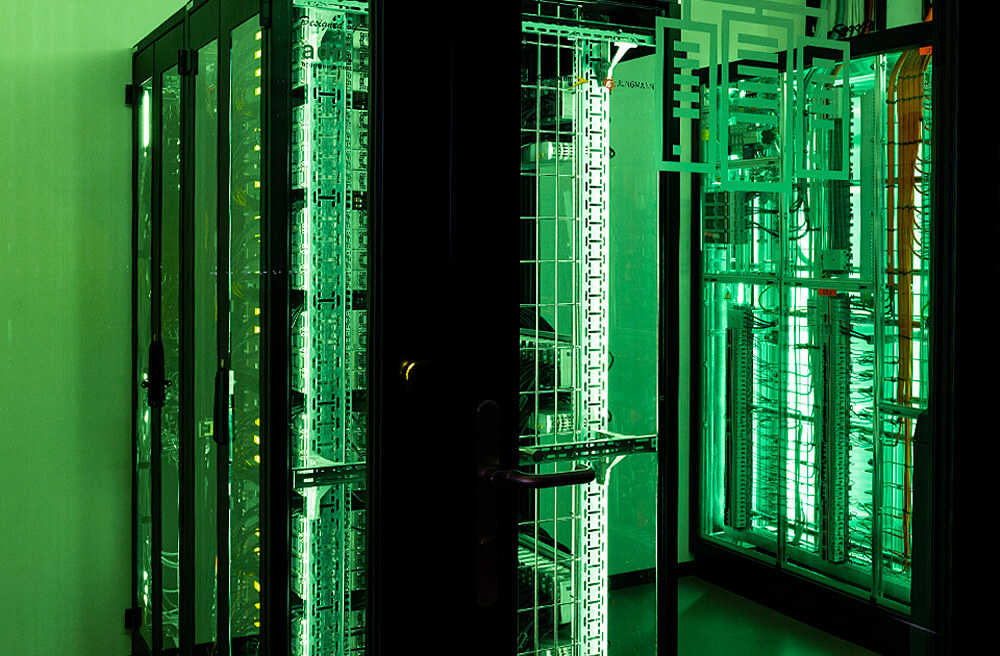
Automated manufacturing processes and quality control are indispensable in the automotive industry. However, maximum product quality requires error-free, reliable monitoring. The operator in the control center must continuously evaluate incoming data with a high level of concentration and react quickly to any deviations. Alternatively, JST’s PixelDetection® software takes over the monitoring of relevant processes in real time.
The application scans patterns in the background and sends visual or acoustic signals in the event of anomalies. Thanks to intelligent filter and analysis functions, only significant alerts are generated. Depending on the alarm prioritisation, notification chains or automated measures can also be triggered.
During a workshop in JST’s unique control room simulator, the control center solutions can be thoroughly tested. The project, targets and budget are defined in a virtual meeting or live on site. The planning phase then begins: experienced control room professionals are at your side with technical planning support in on-site discussions and web meetings! Photorealistic 3D visualisations and film trailers based on the existing floor plans help in the decision-making process. Operating and visualisation concepts are developed. Ergonomics, climate, acoustics, light – all aspects are taken into account. And even after implementation of the automotive control center, JST remains at your side with an individually customized service package.
We offer our customers unique products and solutions for control rooms. An exclusive benefit that only JST can provide.
We have been working in the business for more than 30 years. We would be happy to bring our many years of know-how to your project.
This means that you benefit from our extensive experience and smooth project realisation processes. Because JST keeps everything in mind!
Our experts are among the best. They have been designing control rooms for years. Our team enjoys working together – for you!
Experience more at a planning workshop in the control room simulator
Having visions of the future is good. Experiencing is better! Visit the control room simulator, unique in Europe, where state-of-the-art technology and the latest ergonomic know-how are combined. The control room of the future. The special feature: Here you can touch everything and try it out for yourself.
Whether virtual or live on site – the workshop in the control room simulator is free of charge.
We kindly ask for prior registration.
What clients from the automotive industry say about their experiences with JST – Jungmann Systemtechnik®
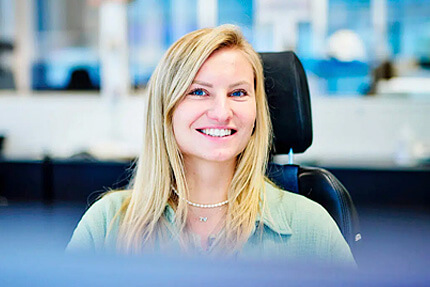
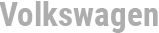
„The work processes have not only become clearer for employees, but also much more convenient. The data that is really important is in the foreground and no longer disappears in the flood of messages.“
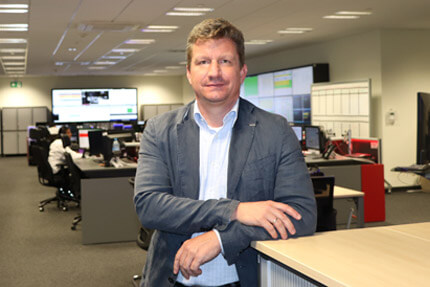
„By merging individual interfaces, the various control centers can communicate efficiently and directly with each other. This enables us to detect the smallest deviations at an early stage and to react in time.“
Photo: © AUDI AG
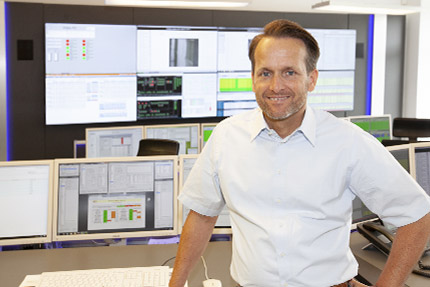
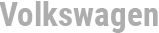
„We simply wanted to be able to use the optimal software solutions that allow us to act quickly“
Symbiosis of innovative control room technology and ergonomic furniture sets high standards automotive industry control centers
On the one hand, an improved overview and convenient handling – on the other hand an ergonomic bestseller that is already celebrating success in hundreds of control centers. The JST CommandPad® and the Stratos X11® control room console are becoming a successful duo in the automotive control center. As a user panel for the JST 3D interface myGUI®, the Command Pad can be integrated directly into the surface of the Stratos desk. In the video below, JST expert Dirk Lüders focuses on four central features that are of importance in industrial control rooms.
Perfect integration into the Stratos X11® operator console
Together, JST developers and furniture designers have created the perfect interplay of technology and usability: In the built-in version, the JST CommandPad® is integrated directly into the Stratos X11® console. The operator in the automotive control center has sufficient room to move the mouse and keyboard.
Intuitive: “direct line” to the myGUI® user interface
Control room operation has never been so clear and convenient! No complicated command inputs, no delays. The JST CommandPad® provides a constant overview of all vehicle production systems directly at the workplace. Desired functions are executed at the touch of a finger using previously defined settings.
Poor air quality? Traffic light system warns operator
Increased concentration, improved attention! To counteract signs of fatigue among control center employees, an air quality sensor integrated into the Stratos X11® can be read via the JST CommandPad®. A traffic light system warns the operator at an early stage if the air quality is declining.
Effortless integration of the rights and roles system
Security is one of the priorities in control centers for the automotive industry! The protection of sensitive data is implemented via the myGUI® controller using strategic rights and role management. The administrator decides who in the operator team has access to the available data and to what extent.
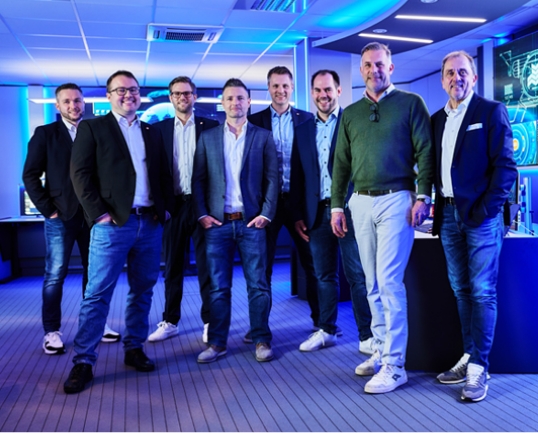
Fixed contact person for all phases of the project
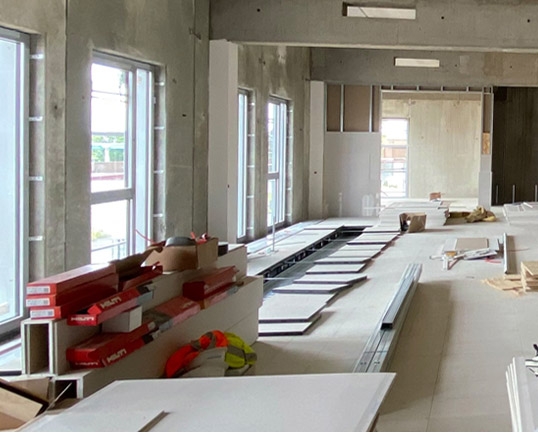
Workflow and task coordination with the specialist departments
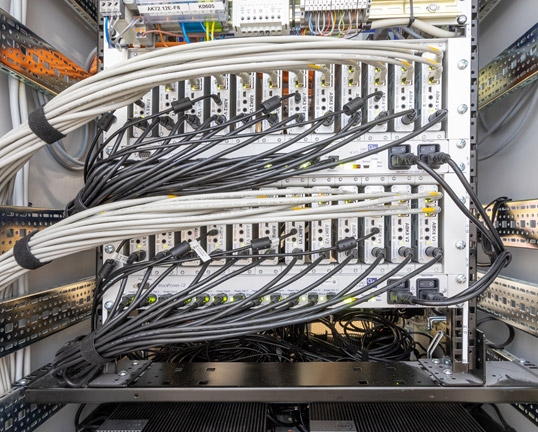
Professional implementation of all components
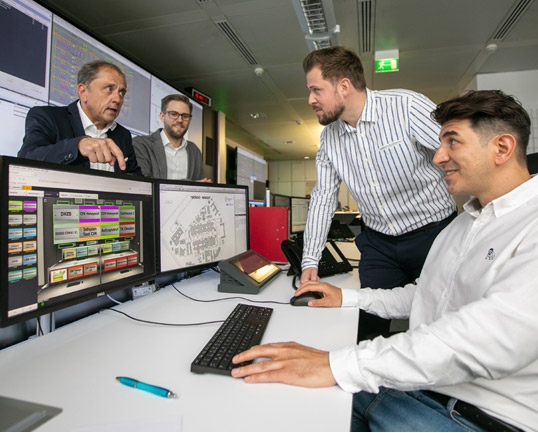
Employee training and initialization of the new Control Center
Turnkey Solutions:
Integrated overall solution creates a real competitive advantage
You want a control center where all information comes together? A control room as a secure basis for the requirements of the digital future, precisely tailored to your processes and needs?
With our experience from more than 600 projects, we are the right partner for turnkey solutions that transform your control room into a profit center.