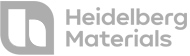
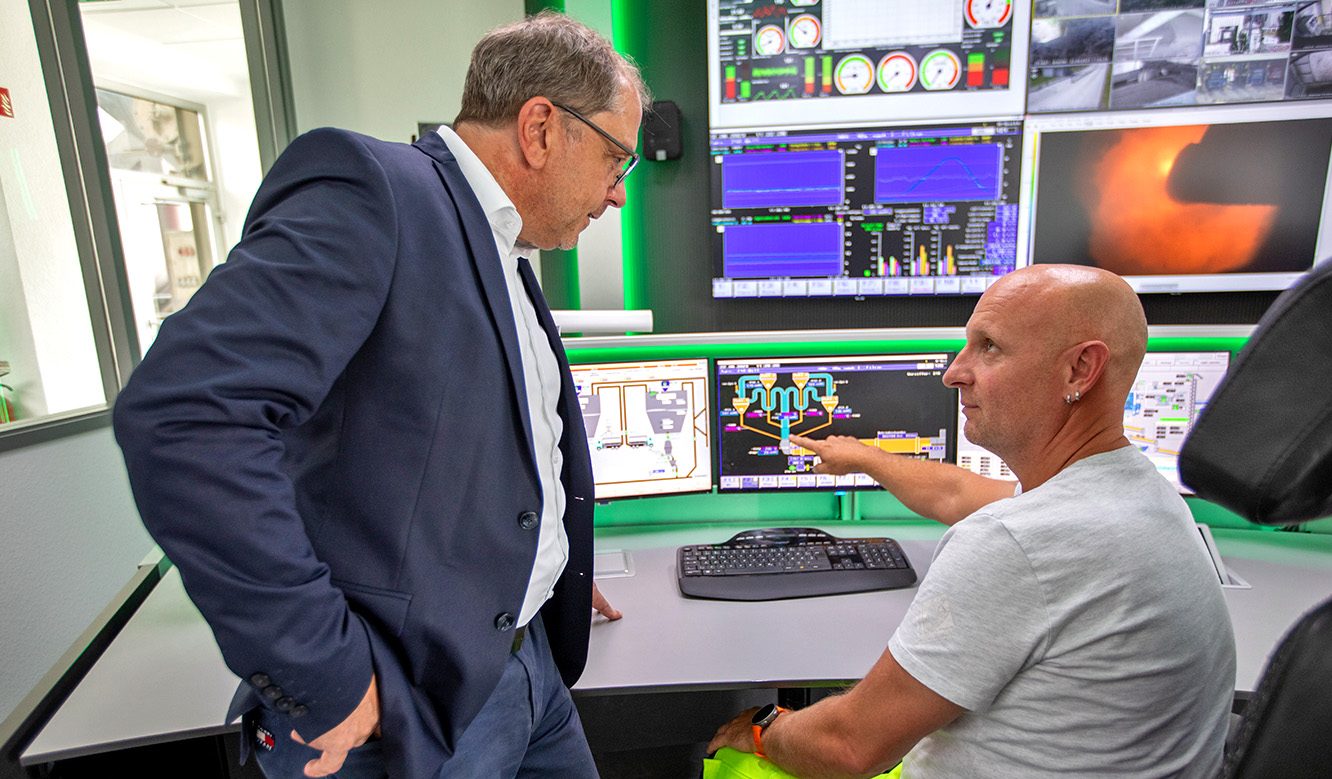
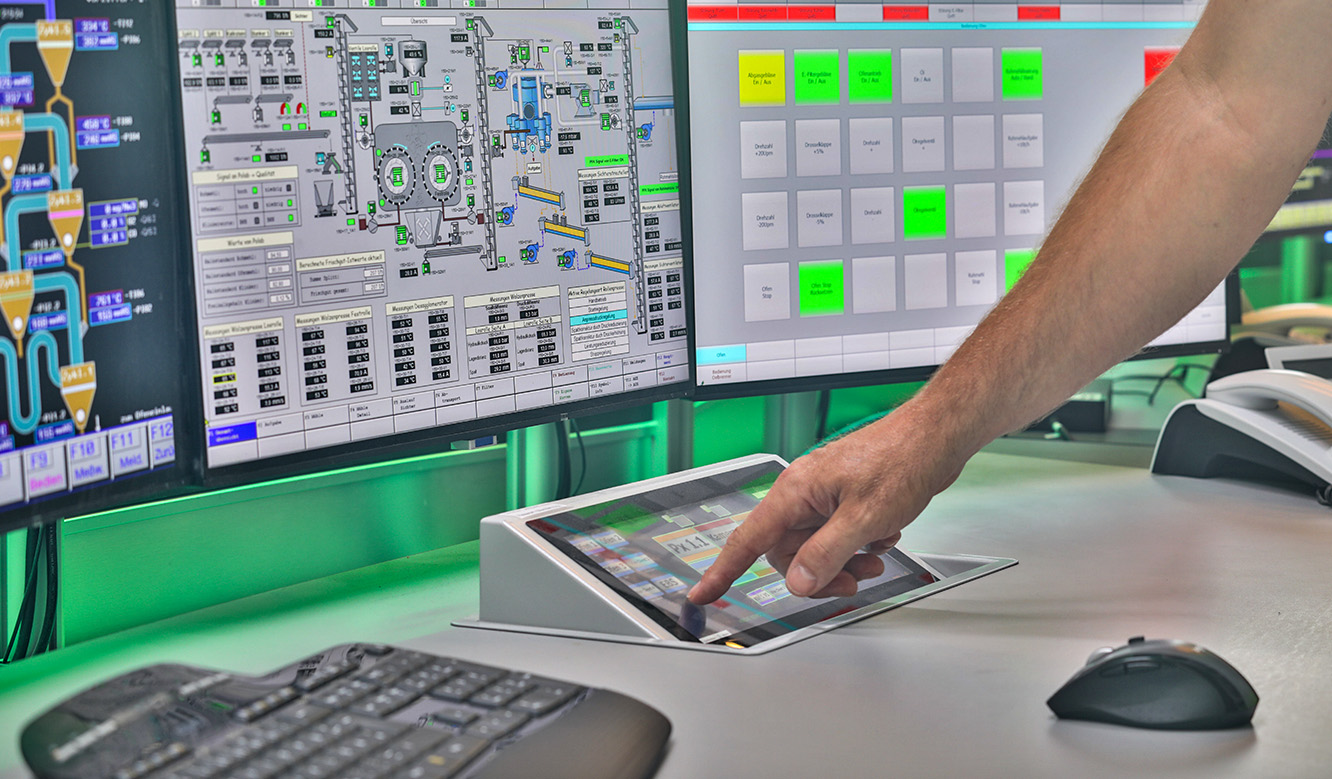
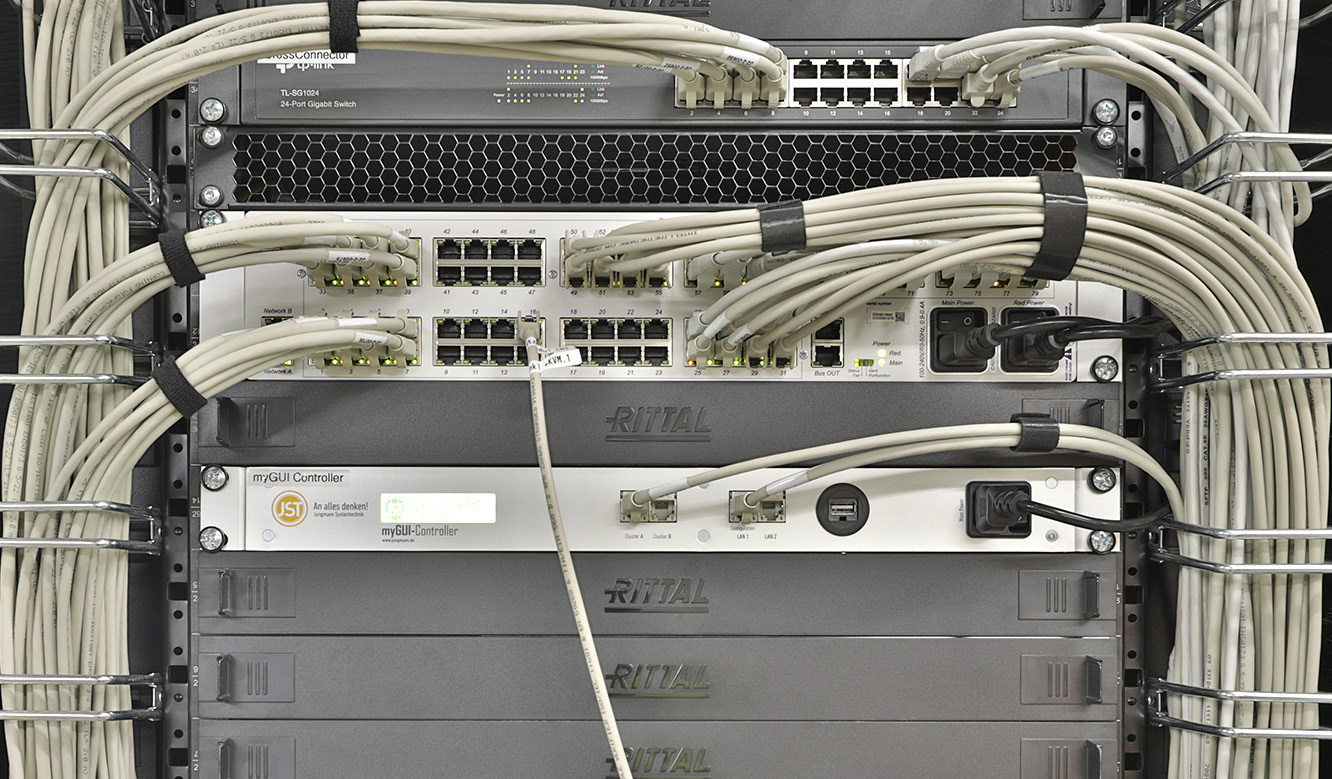
Photo 1 | The new control center at Heidelberg Materials' Geseke site is ideally equipped for the decarbonization course that has been initiated: Ergonomic furniture, flexible visualization options, and the control room management with MultiConsoling® technology create the necessary conditions for monitoring the processes of additional equipment on the premises of the cement plant as well.
Photo 2 | Before the upgrade: typical picture for grown structures in many control stations. Entire columns of monitors crowd the work desks. Each monitor displays a single application. The operators have to keep rolling from place to place with their office chairs. Image: © Heidelberg Materials
Photo 3 | After the upgrade: an end to the constant to and fro in front of the screens. Perfect overview thanks to large-screen technology combined with flexible MultiConsoling® control. The technology makes it possible to display any desired source to any screen virtually at the touch of a button.
Photo 4 | The cement plant in Geseke, North Rhine-Westphalia: From 2029, a complete CCS value chain (CCS = Carbon Capture and Storage) will start from here, with which around 700,000 tons of CO₂ will be captured annually. Image: © Heidelberg Materials
Photo 5 | The rotary kiln is virtually the heart of the plant. Here, during burning at a temperature of around 1,450 degrees Celsius, a new product is created from the raw meal through so-called sintering, a chemical conversion process: the cement clinker. Image: © Heidelberg Materials
Photo 6 | Whether in the rotary kiln or during subsequent storage in the cement silo. In all processes, the control center must ensure that the specified values are maintained. Stefan Naber: "Anything that deviates from the norm is significant for us: A pressure is not as it should be, a temperature suddenly rises - then the control center operators become active."
Photo 7 | JST control room consoles: The control station consoles offer numerous ergonomic advantages. In addition to generous legroom and a particularly deep tabletop with a lowered monitor area, these include in particular the electric motor-driven height adjustment, which, for example, makes it possible to switch between sitting and standing. Every operator can thus adapt "his" Stratos X11® control room console to individual needs.
Photo 8 | JST control station desks: The Stratos X11® operator console not only meets the highest ergonomic and visual demands, ...
Photo 9 | JST control room consoles: ...concealed behind the inspection flaps are generously sized, illuminated supply rooms that provide sufficient space for technical equipment.
Photo 10 | JST PowerPort Data Box: The operator consoles have been equipped with power port data boxes. This gives control station operators immediate access to the desired supply connections conveniently directly at the workstation.
Photo 11 | JST furniture: "Keep everything in mind!" - this JST guiding principle is also reflected in the well thought-out planning: Behind the sight protection...
Photo 12 | JST Furniture: … a cabinet solution with integrated galley kitchen is hidden - individually manufactured for the control station in Geseke.
Photo 13 | JST control center solutions: Acoustics, lighting, atmosphere - the OPAL X11® ceiling sail creates a new level for the operator workplace. In addition to optimizing the acoustic values, the integrated HCL light source (Human Centric Lighting) is one of the decisive advantages. HCL lighting takes into account the visual, emotional and biological effects of light. Its color values also have a positive effect on concentration and performance.
Photo 14 | JST DisplayWall: The control center operators have a perfect view of the video wall from their workstations. Design strips with a high-quality brushed aluminum surface and the AlarmLight give the videowall its unmistakable JST look. Behind the fronts of the DisplaySuit are the components for a climate control concept with large-volume air outlets. Advantage: The cooled air exits at low velocity, meets the back of the operator consoles and then swirls successively without causing any adverse effects due to drafts.
Photo 15 | JST control station concept: Red light immediately signals "Attention!" - there are possible deviations from the target values. The control center team becomes active immediately.
Photo 16 | Control station operator Rene Ventur in conversation with JST consultant Volker Weimer (left) - for the planning of the new control center, it was determined exactly which components could be used to support the work of the operators.
Photo 17 | JST CommandPad®: It is one of the tools that make processes in the control station not only faster but also more secure: One tap on the JST CommandPad® (here as an integrated solution) is enough to switch a selected source to any desired screen.
Photo 18 | JST Technology: Outsourcing the technical components has the positive effect of keeping heat and noise away from the control station. Access-secured premises also create additional security; from above: CrossConnector, MultiCenter and myGUI® controller.
Control center in cement plant put in position for the decarbonization
Here things are moving in big steps toward a climate-neutral future! The Heidelberg Materials company is providing the evidence: Even in cement production – known for high carbon dioxide emissions – CO2 neutrality is not a utopia. The necessary conditions for this are to be created at the Geseke site by 2029. The control center, which will later take over the management of the additional processes, was already positioned for the decarbonization offensive at an early stage – with solutions from JST – Jungmann Systemtechnik®.
A long row of work tables, 20 monitors on them, each displaying a different process flow. In front of them: two control station operators who have a daily “race” on their office chairs along the phalanx of screens.
Outdated control center with far too many monitors
“We had a completely outdated control center with far too many monitors, rooms that were not air-conditioned – almost like an office workstation multiplied 20 times,” reports the man who supervised the control center project at the Geseke cement plant. For Stefan Naber (Operations Manager Production)), one thing was certain: The visualization options in the control room were already insufficient for the current process control. And: “We couldn’t even set up as many screens here as we’ll need in the future to visualize the new systems.”
Heidelberg Materials Geseke – Control Center before and after renovation
Perfect prototype already in operation for colleagues
For the project manager, it was quickly clear what the ideal control center should look like and what it should be able to do. Just two years earlier, the Heidelberg Materials colleagues at the Ennigerloh site had put the perfect prototype into operation – equipped and installed by Jungmann Systemtechnik. “We spoke to our colleagues on site and received very positive feedback throughout,” recalls Stefan Naber. So the decision was easy to select the right components for the future tasks.
Mammoth task: Decarbonization
Indeed, a mammoth task awaits the Geseke cement plant with complete decarbonization. The GeZero project, which Heidelberg Materials is launching in Geseke, will be the first to realize a complete CCS (carbon capture and storage) value chain for the capture, transport, and permanent storage of all CO₂ emissions at a German domestic site.
From rock, via crushed stone and raw meal to clinker
Whether energy supply, pressures, bearing or shell temperature, whether the processing of rock into crushed stone in the so-called crusher or the burning of raw meal into clinker in the rotary kiln – the new control station now uses innovative technology to monitor all this. A modern large screen wall, which can be controlled conveniently and efficiently thanks to the flexible KVM system MultiConsoling®, in combination with selected sources on the workstation monitors, replaces the formerly seemingly endless column of screens.
Faster and more secure thanks to optimized overview
Stefan Naber: “The overview has improved enormously. We receive automated messages. In the event of a warning, the corresponding application is switched on immediately.” The JST CommandPads® also contribute to this optimized overview; touch displays with which all sources of the control station can be conveniently called up or, for example, alarms can be quickly confirmed.
Ergonomic control room consoles whose height can be varied at the touch of a button are also among the equipment features, such as the OPAL X11®. The ceiling sail scores points not only in terms of lighting but especially with regard to room acoustics.
"The elders were a little skeptical at first"
Project manager Naber is positive about the acceptance of the new installation among the shift workers from the control center: “The older ones, who had already been working with a grown structure for 20 or 30 years, were a little skeptical at first. But their doubts quickly subsided. And the younger employees were already convinced during the planning phase.”
The plant manager also remembers the cooperation with the JST team very well: “The work together with JST – that went very well! The schedule was kept, requests were answered quickly, and the implementation was flawless.
Our references today (selection)
A
B
C
E
H
I
M
N
P
R
S
- s.Oliver, Rottendorf
- SachsenEnergie, Dresden
- SAG, Berlin
- SAG, Nürnberg / Nürnberg Messe
- Salzgitter Flachstahl
- Senvion SE, Osterrönfeld
- SGL Carbon Group, Bonn
- SIEMENS
- SIEMENS, Wegberg
- Spenner, Erwitte
- Städtische Werke Magdeburg
- Stadtwerke Gießen
- Stadtwerke Ratingen
- Stadtwerke Schwerin, Kraftwerk Süd
- Stadtwerke Steinburg GmbH, Itzehoe
- Stadtwerke Wolfenbüttel
- Starlim Sterner, Marchtrenk
- STORAG ETZEL, Friedeburg
- Straßenverkehrsamt Frankfurt am Main
V
Unsere Referenzen (Archive)