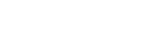
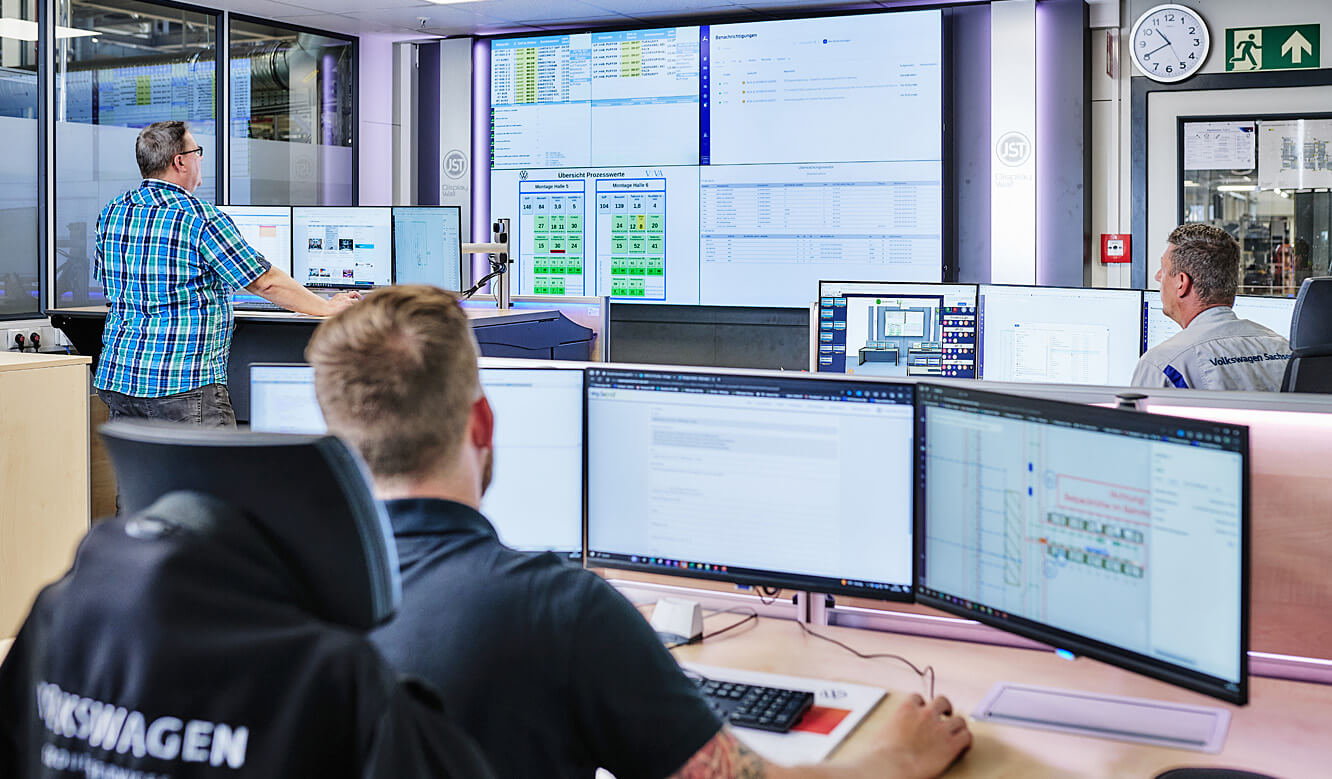
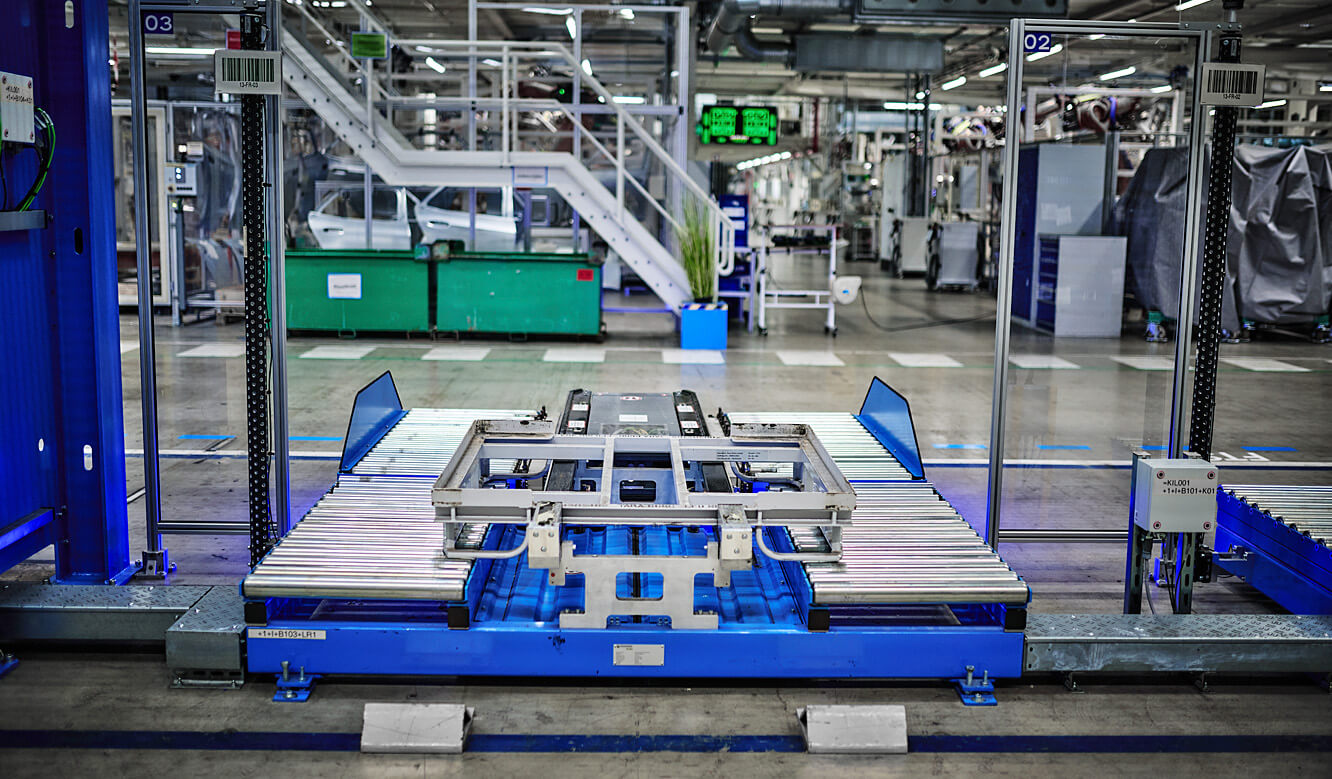
Photo 1 | JST control center: The smart factory is no longer a distant goal for the future at Volkswagen in Zwickau. The development into an Industry 4.0 site is making great strides; here, for example, in the control center for monitoring the automated guided vehicle systems (AGVs), which link assembly and intralogistics into an efficient process.
Photo 2 | Automation in the high-tech factory at the Volkswagen site in Zwickau enables shorter process times, among other things. Around 1,700 of the latest generation of production robots and more than 500 automated guided vehicles (AGVs) pave the way for human-robot cooperation.
Photo 3 | JST control room furniture: The Stratos X11® operator console is not only visually appealing, but also has impressive "inner values". Behind the flap mechanism in the lower area, for example, there is an easily accessible and additionally illuminated supply compartment that offers sufficient space even for technical components.
Photo 4 | JST ergonomics concept: The electromotive height adjustment of the Stratos X11® control room console offers a comfortable alternative to the sitting position and is also recommended by occupational physicians for ergonomic workplace design.
Photo 5 | JST control room equipment: Appearance also plays a role in modern control rooms. Here, for example, the Stratos console was configured with a company logo and individual color scheme at Volkswagen's request.
Photo 6 | JST control room planning: According to medical expert committees, the optimum design in terms of work ergonomics: The Federal Institute for Occupational Safety and Health also recommends a parabolic arrangement of the screens at the operator desk.
Photo 7 | JST control room ergonomics: TFT columns with 3D monitor articulated arms enable convenient adjustment of the screen orientation at the workstation of the control room operators.
Photo 8 | JST control room ergonomics: Small effort, big effect: The so-called PowerPort Data Boxes are easily accessible embedded in the surface of the operator desk and allow…
Photo 9 | …convenient access to all required supply connections. Personal keyboards for control room employees can be replaced in a flash during shift handovers.
Photo 10 | JST large screen technology: High resolution and brightness, durability and an excellent contrast ratio: The 55 inch displays of the video wall with a screen diagonal of 139 centimeters and software interface for control room management with the JST MultiConsoling® quickly become a real "team player" in the control center. Here, IT expert Rico Trautmann (left) and production supervisor Uwe Menge use the DisplayWall to verify a current fault.
Photo 11 | JST Videowall: A particular advantage of the ultra-narrow bezels selected by Volkswagen for the AGV control center in Saxony: Even large overview images, so-called BigPictures, can be displayed without distracting frames.
Photo 12 | JST MultiConsoling®: Same perspective, different focus: myGUI®, the user interface for control room management with JST MultiConsoling®, provides the operator with a perfect graphical overview of the entire control room infrastructure. This allows intuitive and secure access to all applications.
AGVs: Autonomous transport robots increase efficiency in logistics and assembly
A digital, flexible and highly efficient high-tech factory! Volkswagen is turning this image into reality in Zwickau, Saxony. Production and intralogistics are closely interlinked. Around 1,700 of the latest generation of production robots and more than 500 automated guided vehicles (AGVs) pave the way for human-robot cooperation. Components are brought to the assembly line completely autonomously. To ensure that there are no disruptions in this precisely calibrated process, the automotive group has once again drawn on the expertise of JST – Jungmann Systemtechnik®; with the AGV control center, assembly.
Shorter process times combined with advantages for employees, who are relieved of physically heavy and ergonomically unfavourable work. The benefits of automated guided vehicles are obvious: Whether windscreen, headliner or tailgate – everything moves through the assembly halls at the Volkswagen plant in Zwickau as if by magic. Induction loops in the floor make it possible to organize the internal material flow more efficiently.
Industry 4.0 also for warehouse logistics and assembly
At Europe’s largest e-car factory, warehouse logistics and assembly are also fully in line with Industry 4.0. Manually moved transport cranes, forklifts or the familiar warehouse “ants” are a thing of the past at the high-tech site in Saxony. Autonomous transport robots – equipped with load handling devices, laser scanners and smart sensors – are the formula of the future. They move everything from small parts to loads weighing tons.
"The systems communicate with each other for this purpose"
One person who knows the processes on site and the “cooperation with the steel colleagues” inside out is Michael Beier (Head of Material Control Center and Monitoring, AGV Control Center Assembly Zwickau). He describes the automated processes: “The required vehicle parts are assembled and packed in the external warehouse. They are then transported to the plant by lorry. From unloading onwards, the automated guided vehicle systems take over and transport the load units to the desired location on a time-controlled basis. The time control and order management systems communicate with each other for this purpose.”
Control room follows the Smart Factory concept
The entire process is monitored by a team of operators who work in three shifts in the newly created AGV control center for assembly. The new control room, which follows the Smart Factory concept, was installed in co-operation with JST – Jungmann Systemtechnik®. This is not the first time that VW Saxony has drawn on the know-how of the control room experts. The warehouse control center for materials management was implemented jointly a few years ago. With great success: “We wanted to work with JST again, particularly because of our positive experience with the material control center,” reports Michael Beier.
You are currently viewing a placeholder content from YouTube. To access the actual content, click the button below. Please note that doing so will share data with third-party providers.
More InformationOperator team benefits from fast familiarization
The operator team for the current project is made up of “old hands” and “new heads”. “This has the advantage that the employees benefit from the experience of their colleagues and were able to support each other during familiarization,” says Michael Beier. As a result, everyone quickly appreciated the ergonomic and technical options available to them with the JST installation.
Control center helps to visualize processes in the system
Whether Stratos X11® console, the ergonomic bestseller in terms of control room furniture, large screen technology or its flexible control with the JST MultiConsoling® – Michael Beier knows the value of the new equipment: “The control station with its functionality helps us to visualize the various sub-processes within the system. We don’t have to guess where the fault might be; the large display wall shows us this directly.” What might a malfunction look like? “It is possible, for example, that a bicycle is in the way, meaning that the lane is blocked. The control center personnel can then intervene on site and initiate the corresponding system adjustments in time or order control so that the process can start up again.”
Praise for execution and installation time
However, it was not just the performance of the individual components that was particularly important to the project manager. The trusting cooperation with JST Consultant Volker Weimer was also an essential aspect for him and – last but not least: “The installation of the new AGV control station went really quickly!”
Some of the operators in the new AGV control room were already familiar with the optimizations made by the JST technology components from the material control station that was installed a few years ago. This allowed the employees to support each other during the familiarization phase. The photo shows from left to right: Willi Tröger (AGV planning project team), Uwe Menge (Production Supervisor Automated Guided Vehicles, Assembly) Michael Beier (Head of Material Control Center and Monitoring, AGV Control Center Assembly) and Silvio Schmidt (Production Supervisor Automated Guided Vehicles, Assembly).
Unsere Referenzen heute (Auswahl)
A
B
C
E
H
I
M
N
P
R
S
- s.Oliver, Rottendorf
- SachsenEnergie, Dresden
- SAG, Berlin
- SAG, Nürnberg / Nürnberg Messe
- Salzgitter Flachstahl
- Senvion SE, Osterrönfeld
- SGL Carbon Group, Bonn
- SIEMENS
- SIEMENS, Wegberg
- Spenner Zement, Erwitte
- Städtische Werke Magdeburg
- Stadtwerke Gießen
- Stadtwerke Ratingen
- Stadtwerke Schwerin, Kraftwerk Süd
- Stadtwerke Steinburg GmbH, Itzehoe
- Stadtwerke Wolfenbüttel
- Starlim Sterner, Marchtrenk
- STORAG ETZEL, Friedeburg
- Straßenverkehrsamt Frankfurt am Main
V
Unsere Referenzen (Archive)